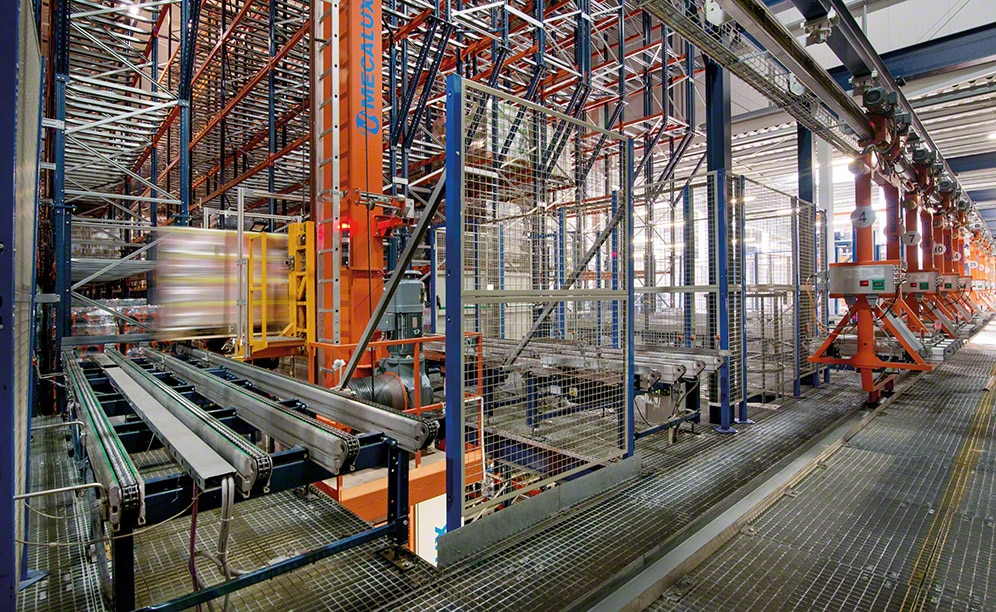
Un grand entrepôt pour les jus de fruits Sokpol en Pologne
L'entrepôt de jus de fruits de Sokpol est connecté avec le centre de production par un circuit de balancelles automotrices
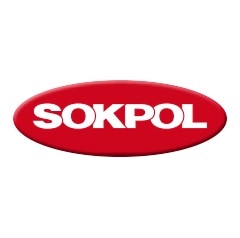
Sokpol est l’un des fabricants de jus, nectars et eau minérale les plus connus de Pologne. Son centre de production situé à Myszków est équipé d'une technologie de pointe afin de renforcer sa productivité. Ce projet, en constante expansion, s’est développé et adapté au fur et à mesure des exigences de Sokpol et aux nouveaux besoins du marché. Actuellement, le centre est composé de deux entrepôts, l’un équipé du système Pallet Shuttle semi-automatique pour les produits finis les plus demandés et l’autre d’une capacité de plus de 28 400 europalettes à fonctionnement entièrement automatique.
À propos de Sokpol
Les jus, rafraîchissements et purées de fruits de Sokpol sont parmi les plus populaires de Pologne. L’entreprise a été fondée en 1992 et, développe et commercialise en permanence de nouveaux produits.
Ces dernières années, l’entreprise a renforcé sa présence internationale et ses produits sont distribués dans une grande partie de l’Europe et aux États-Unis.
Les besoins de Sokpol
Sokpol possède un centre de production dans la ville de Myszków, dans le Sud de la Pologne, où elle fabrique la plupart de ses produits. Son emplacement idéal favorise une distribution rapide de la marchandise sur tout le territoire européen.
Au départ, le centre disposait d'un entrepôt à côté de la zone de fabrication, destiné au stockage des produits finis. Toutefois, l'espace était insuffisant pour faire face à l’augmentation de la production.
L’entreprise a dû élargir son catalogue de produits et a augmenté le volume de ses ventes en raison de son développement international. Désireuse de relever le défi et de renforcer ses perspectives d'avenir, elle a sollicité la collaboration de Mecalux.
La solution
Compte tenu des exigences de Sokpol, Mecalux a conçu et construit un entrepôt automatisé d’une capacité de plus de 28 400 europalettes (800 x 1 200 mm) ou 56 800 demi-palettes (400 x 600 mm). C'est une solution très moderne, fonctionnelle, qui garantit une productivité élevée, tout en dépassant toutes les attentes.
Le centre de Sokpol est situé sur une grande parcelle de terrain et le nouvel entrepôt se trouve loin de l’usine de production. Couvrir cette distance au moment de transporter la marchandise pouvait entraîner un coût très élevé qu'il était nécessaire de minimiser.
Pour cela, Mecalux a construit un pont surélevé et couvert – à 5 m au-dessus du sol – qui relie la sortie de production au nouvel entrepôt, en traversant le premier entrepôt par l’un de ses côtés. À l'intérieur, un circuit monorail électrique permet de transporter très rapidement la marchandise.
Entrepôt 1
Sokpol a construit un premier entrepôt situé à côté de son usine, équipé du système Pallet Shuttle semi-automatique.
Il sert de tampon (stockage de courte durée) et y sont stockés, principalement, les produits finis les plus demandés, en attendant d’être envoyés à la zone d'expédition.
C'est un système très adapté pour ce type de produit, à forte rotation et avec de nombreuses palettes pour chaque référence. Il exploite au maximum tout l'espace disponible pour obtenir une plus grande capacité de stockage. De plus, son fonctionnement est simple, souple et requiert une intervention humaine minimale, permettant ainsi l’entrée et la sortie permanente d'articles.
La marchandise est gérée conformément au principe FIFO (first in, first out), c'est-à-dire que la première palette à entrer est la première à sortir. Il y a deux allées de travail : l'une de chargement et l'autre de déchargement, ce qui évite les interférences entre les deux opérations.
L’entrepôt dispose d’une zone de préchargement, située face aux quais. Les palettes sont regroupées au sol pour un chargement plus rapide des camions de distribution.
De même, il possède deux étages. Des opérations différentes sont effectuées à chacun d'entre eux :
Étage inférieur
L’usine de production et l'entrepôt occupent cet espace. Les opérateurs bénéficient d'une communication directe et sans obstacles pour transporter la marchandise d’un endroit à l’autre. À l'aide de chariots à mât rétractable, les opérateurs récupèrent les palettes et les déposent dans le canal des rayonnages assigné par le logiciel de gestion d’entrepôt (WMS). Ensuite, la navette motorisée dirige automatiquement la charge jusqu’au premier emplacement libre.
Mecalux a également installé un circuit de convoyeurs, juste à la sortie de production, dans lequel sont introduites les palettes qui se dirigent directement jusqu'à l'entrepôt 2. Les convoyeurs acheminent les palettes vers deux élévateurs qui transportent les charges jusqu'à l’étage supérieur, où se trouve le circuit monorail électrique.
À côté des quais, un troisième élévateur envoie les produits à l’étage supérieur. Cette entrée est destinée aux produits provenant d'autres centres de fabrication qui doivent être stockés dans l’entrepôt 2.
Avant d'atteindre l'élévateur, les palettes traversent un poste d'inspection. Les opérateurs y vérifient qu'elles sont en bon état et que leur poids et dimensions correspondent aux exigences de qualité requises dans l'entrepôt automatisé.
Les convoyeurs comme les élévateurs sont protégés par des panneaux grillagés, des barrières optiques et des portes d'accès sécurisé qui évitent l'entrée de personnes non autorisées dans leur champ d'action.
Premier étage
Les systèmes monorails électriques parcourent l’un des côtés de l’entrepôt et se dirigent jusqu'au pont surélevé. De l'autre côté du pont se trouve l'entrepôt 2.
En installant le circuit monorail électrique à une hauteur plus élevée, Mecalux a exploité au maximum la surface de l’entrepôt et a également évité les interférences avec les autres opérations qui y sont effectuées.
Pont surélevé et circuit monorail électrique
Le pont surélevé est la meilleure solution pour relier les trois bâtiments entre eux. De même, il relie les entrepôts 1 et 2, qui sont séparés par une allée.
Le circuit monorail électrique a été installé à l'intérieur. Il s'agit d'un système de transport très souple et rapide qui atteint jusqu'à 100 m/min et garantit un flux constant de marchandise.
Le circuit est composé de rails suspendus au plafond par lesquels se déplacent des navettes autonomes qui transportent les palettes. Il est possible d'augmenter le nombre de navettes en fonction des besoins et de la croissance de l’entreprise.
Dans cet entrepôt, les opérateurs travaillent surtout avec des europalettes et des demi-palettes. Pour pouvoir les transférer, les navettes des systèmes monorails électriques comme les convoyeurs sont munis de quatre brins de chaînes. Les principaux avantages des systèmes monorails électriques sont leur grande efficacité, leur grande polyvalence et la réduction d'erreurs qu'ils entraînent. Le circuit parcourt toute la zone périphérique de l’entrepôt 2, en introduisant ou en retirant les palettes dans les convoyeurs d'entrée et de sortie de chaque allée.
À la fin de l’itinéraire, Mecalux a aménagé une zone de maintenance où sont acheminées les navettes qui nécessitent une réparation et où sont regroupées les navettes en attente.
Ce circuit a été conçu très méticuleusement, en tenant compte des flux et du nombre de palettes qui doit être déplacé entre les deux entrepôts. C’est pourquoi, deux raccourcis, qui évitent que les navettes parcourent le circuit complet, ont été créés.
Entrepôt 2
L'entrepôt automatisé, de 15,5 m de haut, se compose de neuf allées dotées de rayonnages à simple profondeur des deux côtés.
Les références sont déposées aux emplacements correspondants des rayonnages en fonction des critères de rotation A, B et C. Les produits à forte rotation sont situés dans la partie avant de l’entrepôt et ceux à faible rotation, à l'arrière. Cette organisation optimise les déplacements des engins de manutention et augmente le nombre de cycles.
Dans chaque allée, le transstockeur monocolonne circule en travaillant à une vitesse de translation de 160 m/min et à 38 m/min en levage.
Les transstockeurs retirent les palettes des convoyeurs d'entrée et les déposent à l'emplacement qui leur a été assigné par le logiciel de gestion d'entrepôt Easy WMS de Mecalux. Par la suite, ils effectuent le même mouvement pour la sortie de la marchandise, mais en sens inverse.
La zone périphérique de l’entrepôt se compose de deux étages. À l'étage supérieur, les systèmes monorails électriques permettent de réaliser les entrées et sorties de la marchandise de l'entrepôt. Quant à l'étage inférieur, Mecalux en a profité pour poser les armoires de puissance et de contrôle, ainsi que les portes d'accès aux zones de maintenance.
Les tableaux électriques envoient et reçoivent des signaux, tout en transmettant la puissance électrique aux engins de l’entrepôt, comme les convoyeurs, les transstockeurs, les systèmes monorails électriques ou encore les élévateurs.
Un bâtiment de faible hauteur a été construit. Il est adossé à un côté latéral de l’entrepôt et est divisé en deux étages développant des opérations différentes :
Premier étage
Il dispose d'un espace diaphane où se trouvent les postes de picking. Les systèmes monorails électriques approvisionnent cette zone de l’entrepôt avec les palettes nécessaires pour réaliser la préparation des commandes. Les convoyeurs d’entrée intègrent une table hydraulique qui permet de travailler avec des transpalettes.
Étage inférieur
Il est destiné aux sorties vers les expéditions et la zone de préchargement. Deux élévateurs descendent les palettes jusqu'à l’étage inférieur, où deux navettes organisent cette zone en déposant la marchandise dans le canal dynamique correspondant.
Les navettes relient deux points et peuvent se déplacer de manière bidirectionnelle. Elles se déplacent sur des rails et sont dotées de quatre brins de convoyeurs à chaînes pour déplacer les palettes. 40 canaux dynamiques de préchargement ont été installés avec une légère inclinaison qui facilite le déplacement par gravité des palettes de la partie la plus élevée à la plus basse (qui donne sur les quais). Une fois à ce niveau, les rouleaux sont divisés pour que les fourches des chariots puissent retirer les palettes.
Easy WMS de Mecalux
Face à l'envergure de ce centre, l'utilisation d'un système informatisé très efficace est fondamentale.
Ainsi, Easy WMS, le logiciel de gestion d’entrepôt développé par Mecalux, contrôle et intervient dans tous les processus qui se déroulent dans l'entrepôt, y compris l'entrée de la marchandise provenant de fabrication et de l’extérieur, l'assignation d’emplacements, le contrôle du stock, l'extraction, l'envoi aux expéditions, etc.
Pour stocker la marchandise aux emplacements correspondants, Easy WMS de Mecalux intègre des règles et des algorithmes qui tiennent compte des caractéristiques des produits, des critères de consommation et de leur rotation.
Le logiciel WMS indique quels produits doivent quitter l’entrepôt. Ceux-ci sont transportés automatiquement jusqu'à la zone de préchargement. Ils demeurent ainsi en attente jusqu'au moment où le camion se range contre le quai pour être chargé.
Pour que ce centre puisse fonctionner correctement, Easy WMS de Mecalux est en communication permanente avec le logiciel Easy WMS, l’ERP de Sokpol et, à son tour, avec le module de contrôle Galileo.
Galileo est le logiciel de commande de Mecalux, il est chargé de donner les ordres aux machines (convoyeurs, transstockeurs, systèmes monorails électriques et élévateurs) des deux entrepôts, ainsi que d'enregistrer les éventuels incidents.
Il fournit toute l’information en temps réel de chacun des équipements et est capable de simuler le fonctionnement électromécanique de l’installation automatique complète par le biais d'un système de commande dénommé SCADA.
Les avantages pour Sokpol
- Un système de transport efficace : le circuit monorail électrique relie les deux entrepôts de production, en garantissant le nombre de mouvements de palettes nécessaire pour Sokpol.
- Sécurité de l’installation : les éléments électromécaniques sont protégés pour éviter les incidents, ainsi que l’accès du personnel non autorisé.
- Un fonctionnement optimal : la distribution de la marchandise en fonction de ses caractéristiques et rotation dans l’entrepôt augmente la productivité des deux entrepôts.
Galerie
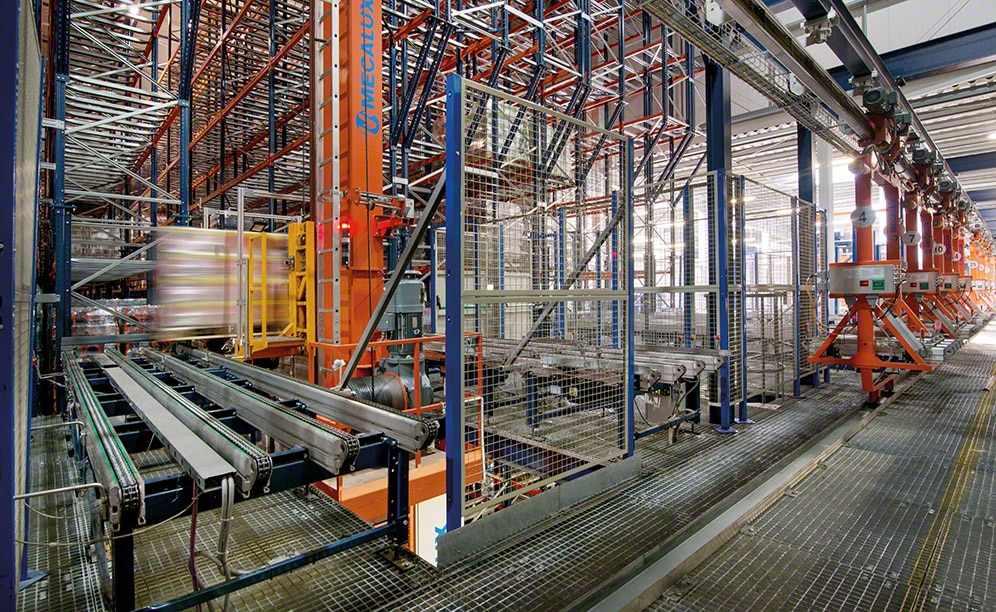
L'entrepôt automatique de Sokpol a une capacité de stockage de 28.400 palettes
Demandez conseil à un expert