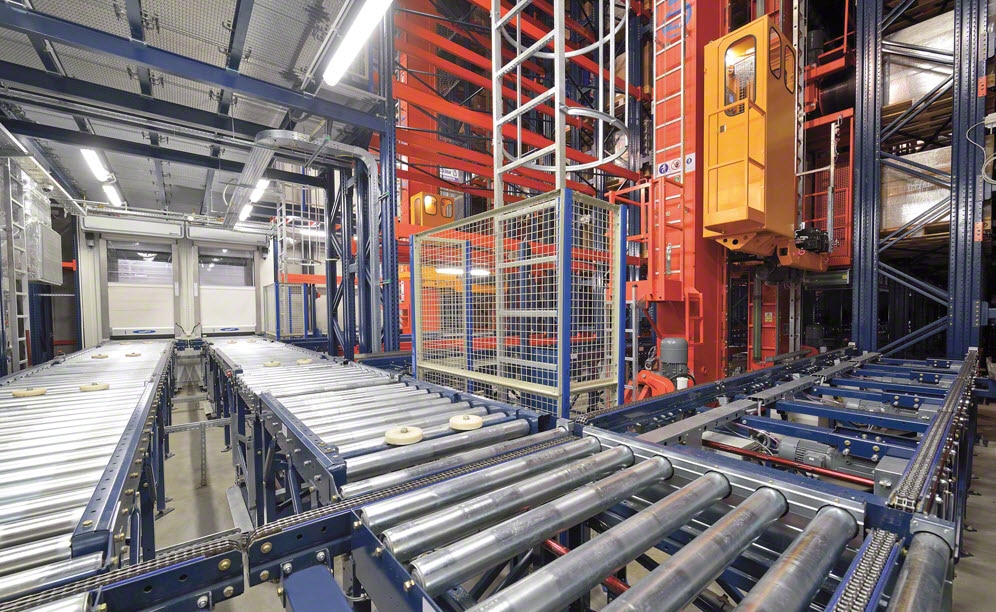
Une entreprise pharmaceutique japonaise commande un magasin clé en main à Mecalux en Pologne
Un magasin automatique de 32 mètres de haut pour l'entreprise pharmaceutique Takeda
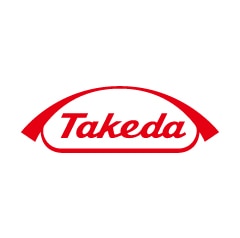
Takeda, une des entreprises pharmaceutiques les plus importantes au monde a fait confiance à Mecalux pour la construction d’un entrepôt clé en main dans son nouveau centre de production de Lyszkowice, proche de la ville de Lowicz en Pologne. La solution adoptée est un entrepôt autoportant à température contrôlée d’une hauteur de 32,5 mètres. D’une capacité de stockage de plus de 6 500 palettes, il est équipé d’un système de réfrigération et est protégé contre les incendies grâce à la possibilité de réduire la teneur en oxygène dans l’air (inertage), empêchant ainsi toute combustion. La livraison comprenait aussi le système de gestion d’entrepôt Easy WMS, édité par Mecalux. Ce système gère tous les processus se déroulant dans le centre.
Qui est Takeda ?
Takeda Pharmaceutical Company Limited, dont le siège se situe à Osaka (Japon) est une entreprise mondiale spécialisée dans la recherche et le développement de produits pharmaceutiques. Au milieu du XXème siècle, cette entreprise a connu une croissance importante qui l’a projeté rapidement en position de leader mondial du secteur pharmaceutique et entreprise pharmaceutique la plus importante du Japon.
Takeda est présent dans plus de 70 pays d’Asie, d’Amérique du Nord et d’Europe, en Russie, en Chine et également dans des pays émergents comme en Amérique Latine.
La solution : un entrepôt autoportant
Afin d’obtenir un contrôle parfait de la marchandise stockée, l’entreprise Takeda a directement pensé à l’automatisation lorsqu’elle a projeté d’agrandir son centre de production. Aussi, l’espace au sol disponible pour la construction de l’entrepôt étant limité, cette solution a permis d’atteindre la hauteur maximale possible.
La solution proposée par Mecalux a été la construction d’un entrepôt autoportant de 32,5 mètres de hauteur situé à côté des bâtiments de fabrication et de l’entrepôt assigné aux pré-chargements préliminaires aux expéditions. Dans ce type de constructions, ce sont les rayonnages eux-mêmes qui forment la structure de l’entrepôt.
L’installation comporte deux allées sur lesquelles deux transtockeurs automatiques se déplacent en toute autonomie. Ces transtockeurs manipulent les palettes stockées dans les rayonnages double profondeur (deux palettes en profondeur par niveau). Grâce à une utilisation optimale de l’espace, l’entrepôt de Takeda a une capacité de stockage de plus de 6 500 palettes sur une surface de 950 m² seulement.
L’entrepôt a été équipé d’un système de contrôle de la température et de l’humidité de l’air (HVAC – Chauffage, Ventilation et Air Conditionné) qui maintient la température entre 16 et 24 °C et empêche que le niveau d’humidité de l’air ne dépasse 70 %, ce qui pourrait endommager les marchandises stockées. On y trouve également un système innovant contre les incendies (inertage) qui réduit la teneur en oxygène de l’atmosphère à 15%, afin d’empêcher l’apparition de flammes. Les tubes du système de contrôle de la température et de l’humidité de l’air ont été installés dans la partie supérieure. Ils ont été centrés sur les allées, puis introduits dans les espaces libres des fermes du bâtiment.
Pour le calcul structurel d’un entrepôt autoportant, on tient compte du poids de la structure, de celui de la marchandise stockée, de la force du vent qui provoque aussi bien des mouvements de pression que de succion au niveau de la base installée sur sa zone de construction. On tient compte également du poids de la neige indiqué par les normes, des poussées des transtockeurs et de la présence éventuelle du risque sismique sur le territoire où est située l’installation.
Au vu des dimensions imposantes du bâtiment (14,5 mètres de large sur 32,4 mètres de haut), une structure hautement renforcée a été construite, et un nombre important d’ancrages de grandes dimensions a été installé, afin d’absorber au mieux les forces exercées par le vent.
Les entrées et les sorties sont extrêmement proches et leur conception est très simple. Elles permettent d’utiliser des chariots élévateurs classiques et des empileurs palettes. Le convoyeur est équipé d’un poste d’identification qui garantit l’état optimal de toutes les palettes introduites dans l’entrepôt automatique.
La communication avec l’intérieur de l’entrepôt se fait grâce à une double ligne de convoyeurs (d’entrées et de sorties) qui passent à travers les portes équipées d’un rideau vertical double. L’espace entre deux rideaux est à peu près aussi grand qu’une palette. Le système donne le signal d’ouverture et de fermeture de façon alternée, ce qui permet de limiter la montée de la température intérieure.
Afin de prévenir une perte de capacité, une plateforme supérieure a été installée. Elle est conçue pour les tâches de maintenance et elle sert d’accès sécurisé à chaque allée.
Easy WMS
La gestion, la synchronisation et le contrôle de tout l’entrepôt, y compris des éléments qui interagissent avec les engins de manutention, se fait grâce au système de gestion d’entrepôt Easy WMS, développé par Mecalux.
Les principales fonctionnalités d’Easy WMS sont :
- Réception et enregistrement de toutes les palettes qui entrent dans l’entrepôt.
- Dépôt des palettes dans les rayonnages, en fonction d’algorithmes ou de règles paramétrables.
- Gestion des sorties basées sur des critères FIFO et de traçabilité.
- Le module de contrôle Galileo permet d’exécuter tous les mouvements des éléments mécaniques, ainsi que d’optimiser tous les parcours internes.
- Liaison avec le logiciel de contrôle des portes de l’entrepôt, pour qu’elles fonctionnent automatiquement.
De plus, Easy WMS communique en permanence avec l’ERP SAP, système de gestion principalement utilisé chez Takeda qui échange les ordres et les informations indispensables à la gestion globale.
Entrepôt clé en main
Takeda souhaitait qu’une seule entreprise pilote toutes les phases de développement et de construction de l’entrepôt, mais aussi fournisse le logiciel nécessaire à la gestion de toutes les opérations internes. C’est la raison pour laquelle Mecalux s’est chargé d’exécuter les travaux du début à la fin, et de livrer un bâtiment clé en main.
Phases d’exécution de l’entrepôt :
- Préparation du sol par le pilotage : en raison de la faible capacité portante du sol et des exigences statiques élevées, une cimentation profonde sur des pilotis a été faite.
- Installation de la plaque de cimentation en béton armé : une armature supérieure et inférieure a été construite, renforcée par des tiges en acier, puis le sol a été bétonné.
- Finition : polissage et solidification de la plaque de cimentation, afin d’obtenir une surface sans poussière.
- Montage des rayonnages : dans les entrepôts autoportants, ce sont les rayonnages qui forment l’ossature des entrepôts.
- Montage du revêtement de l’entrepôt : dans les entrepôts autoportants, les murs de panneaux et le toit de type sandwich sont liés directement à la structure des rayonnages. Dans le cas de Takeda et vu que le système d’inertage a été utilisé, le revêtement devait être le plus étanche possible.
- Introduction des équipements de manutention : les convoyeurs et les transtockeurs ont été montés dans l’entrepôt.
- Installation du système d’inertage : un système de protection contre les incendies a été installé. Ce système permet d’injecter de l’azote à l’intérieur de l’entrepôt, pour que la concentration en oxygène soit réduite à moins de 15 %.
- Installation du système de climatisation HVAC : ce système contrôle la température, pour qu’elle soit toujours comprise entre 16 et 24 °C.
- Montage de l’installation électrique et de l’ensemble de paratonnerres.
- Montage de l’installation de drainage.
- Construction de vannes : séparation de la partie de l’entrepôt équipée du système d’inertage de l’entrepôt annexe qui est utilisé dans des conditions environnementales normales.
Avantages pour Takeda
- Capacité de stockage élevée dans un espace réduit : l’entrepôt autoportant permet de stocker 6 584 palettes de dimensions 800 x 1 200 mm, avec un poids de 800kg, maximum, dans un espace de 980 m².
- Sécurité de la marchandise : les produits pharmaceutiques stockés par Takeda sont protégés et isolés par l’entrepôt automatique. Seules les personnes autorisées peuvent accéder à l’entrepôt.
- Entrepôt clé en main : Mecalux a géré les phases de développement et de construction de l’entrepôt. Elle a géré la livraison des systèmes de stockage, de réfrigération et de protection contre les incendies, ainsi que l’installation du WMS.
- Contrôle total : grâce à Easy WMS, logiciel WMS de Mecalux, Takeda contrôle l’ensemble des processus et des opérations qui se déroulent dans l’entrepôt, de la sortie du produit des lignes d’emballage, jusqu’à son expédition.
Entrepôt automatique de Lyszkowice, Pologne | |
---|---|
Capacité de l’entrepôt :: | 6 584 palettes |
Poids max. par palette :: | 800 kg |
Nombre de transtockeurs :: | 2 |
Type de transtockeurs :: | double mât |
Type de fourche :: | double profondeur |
Hauteur de l’entrepôt :: | 32 mètres |
Galerie

Les entrées et les sorties de l’entrepôt se fait grâce à une double ligne de convoyeurs
Demandez conseil à un expert