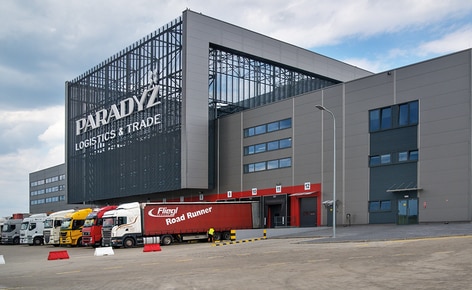
Ceramika Paradyż toujours à la pointe de la technologie avec son nouvel entrepôt automatisé autoportant en Pologne
Grande capacité et des vitesses de picking élevées dans l'entrepôt autoportant automatisé de Ceramika Paradyż
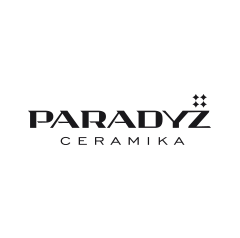
Mecalux a installé pour Ceramika Paradyż un entrepôt automatique autoportant d’une capacité de plus de 20 200 palettes dans la commune de Tomaszów Mazowiecki (Pologne). En périphérie de l'entrepôt se trouve un bâtiment de deux étages qui permet d’organiser efficacement l’entrée et la sortie de la marchandise, tout en accélérant les opérations de préparation des commandes. Le logiciel de gestion d’entrepôt EASY WMS de Mecalux pilote l’installation.
Les besoins de Ceramika Paradyż
Ceramika Paradyż est un fabricant de céramiques polonais de renom, qui exporte ses produits dans plus de 50 pays à travers le monde. Cette entreprise est reconnue pour la technologie de pointe qu’elle utilise dans tous ses processus de production afin d’offrir des produits innovants et de très haute qualité.
Afin de poursuivre son rythme de croissance, elle a choisi Mecalux pour l’accompagner dans la construction d’un entrepôt automatique de grande capacité, composé également d’une zone de picking pour préparer rapidement les commandes.
La solution de Mecalux
Après avoir étudié attentivement les besoins de Ceramika Paradyż, l’équipe technique de Mecalux a conçu et construit un entrepôt automatique autoportant qui répond aux besoins de l’entreprise.
L'entrepôt mesure 25 m de haut, 97 m de long et 35 m de large, et est composé de huit allées équipées de rayonnages simple profondeur sur les deux côtés.
Avec cette solution, la société dispose de la capacité de stockage nécessaire pour approvisionner son marché, essentiellement européen.
Adossé à l'entrepôt, un bâtiment de plus petite taille a été construit. Celui-ci est divisé en deux étages où ont lieu plusieurs opérations.
C’est à l’étage inférieur que se trouve la zone d'entrées et de sorties des marchandises. Y ont été installés des postes de contrôle, un empileur et dépileur de palettes, ainsi que des canaux de préchargement.
C’est au niveau supérieur que se préparent les commandes. Ici, a été aménagée une zone dotée d’un circuit de balancelles automotrices, de navettes, de postes de picking, de tampon de palettes et une zone de consolidation et d’emballage.
L'entrepôt
L'entrepôt de 3290 m2 est composé de huit allées de rayonnages simple profondeur des deux côtés. Dans la longueur, on compte 45 modules, chacun haut de quatorze niveaux et pouvant recevoir deux palettes.
Les articles sont déposés dans les emplacements prévus selon les critères de rotation A, B et C, ce qui permet d’optimiser les mouvements des engins de manutention.
Dans la mesure où il s’agit d’une construction autoportante, les rayonnages doivent supporter leur propre poids, celui de la marchandise, des cloisons grillagées de sécurité et de la toiture. Au moment de leur conception, d’autres facteurs pouvant nuire à la structure ont été pris en compte, comme la force transmise par le vent, les risques sismiques de la zone en question et les normes locales en vigueur.
Entrée et sortie de l'entrepôt
L'entrepôt comprend deux niveaux pour l'entrée et la sortie de la marchandise. Le niveau inférieur coïncide avec le rez-de-chaussée du bâtiment annexe, et c’est à cet endroit que se trouvent l'entrée de la marchandise provenant du centre de production ainsi que la sortie des palettes complètes et des commandes terminées en direction de la zone d'expédition.
À l’étage supérieur, qui coïncide avec le niveau supérieur du bâtiment annexe, se trouve la sortie des palettes utilisées pour le picking et l’entrée des commandes terminées.
Dans chaque allée, les transstockeurs déplacent la marchandise depuis les postes d’entrée et de sortie des deux niveaux jusqu’aux emplacements sur les rayonnages assignés par le logiciel de gestion d’entrepôt Easy WMS.
Ces engins sont des modèles monocolonnes MT3 qui travaillent à une vitesse de déplacement de 220 m/min et de 54 à 66 m/min en levage.
Premier étage : zone de picking
L’étage supérieur du bâtiment annexe de l'entrepôt est entièrement dédié à la préparation des commandes. Cette vaste zone est composée de six postes de picking que prochainement quatre autres viendront rejoindre afin de répondre à la demande et aux besoins logistiques de Ceramika Paradyż.
Le travail des opérateurs est facilité par la mise à disposition d’engins auxiliaires, comme des tables qui s'élèvent jusqu’à une position ergonomique et des manipulateurs de caisses équipés de ventouses pour déplacer les charges les plus lourdes.
Une bonne répartition et incorporation des engins automatiques est essentielle pour réaliser le nombre de cycles requis et garantir un processus de picking optimal. Les balancelles automotrices réceptionnent les palettes provenant de l'entrepôt directement sur les postes de sortie et les déposent sur l'un des quatre convoyeurs d’entrée de cette zone.
Deux navettes doubles organisent cette zone et distribuent les palettes entre les convoyeurs d’entrée, les stations d’attente et les postes de picking. Les palettes d’origine sont déjà utilisées aux postes de picking effectuent l'itinéraire inverse pour retourner à l'entrepôt.
Afin d’éviter les mouvements inutiles de transstockeurs et les constantes entrées et sorties de marchandise à cet étage, Mecalux a aménagé un buffer à 120 positions pour palettes à rotation élevée qui restent en attente, gérées aussi par deux navettes.
Deux autres navettes se chargent d’approvisionner les postes de picking en palettes vides et de récupérer les commandes lorsqu’elles sont terminées. Ensuite, elles les déposent sur les convoyeurs qui communiquent avec les balancelles automotrices qui les dirigent à la zone de consolidation, située sur un des côtés.
À côté de la zone de consolidation, ont été installés des rayonnages pour picking manuel où sont préparés les accessoires lorsque les commandes l’exigent.
Une fois les commandes terminées, les palettes sont envoyées vers la filmeuse. Ensuite, la marchandise sera envoyée en zone de préchargements lorsque cela sera nécessaire.
Communication automatique
Toutes les zones de l’étage de picking sont automatiquement connectées par le circuit de balancelles automotrices et par les navettes.
Les navettes, dont l’objet est de relier en ligne droite toutes les stations et tous les postes de préparation de commandes, sont intégrées à la zone de picking.
Leur principal avantage est qu’elles peuvent se déplacer latéralement sur la rail supérieur et relier toutes les stations. Elles se déplacent sur des rails à une vitesse de 120 m/min et intègrent des convoyeurs à chaînes et à rouleaux, ainsi que des fourches télescopiques pour déplacer les palettes.
Les balancelles automotrices circulent dans un circuit fermé autour de la zone de picking et relient cette zone avec l'entrée et la sortie de l'entrepôt, ainsi qu’avec la zone de consolidation.
La balancelle automotrice a été choisie car c’est un système de transport très rapide qui assure un flux constant de marchandise. Ce système permet des déplacements en courbes ainsi que l’installation de détours et de raccourcis.
Une zone de maintenance a été installée sur un des côtés du circuit. Les navettes y sont envoyées lorsqu’une réparation est nécessaire. En n’occupant pas le plancher, les balancelles automotrices facilitent les tâches de nettoyage.
Zone de réception
L’étage inférieur du bâtiment annexe à l'entrepôt est réparti de la façon suivante :
- Convoyeurs d'entrée
- Ensemble d’empileurs/dépileurs de palettes
- Poste d’inspection de palettes et de remise en état
- Circuit à double sens de redirection et d’union avec les convoyeurs à l’intérieur de l'entrepôt.
- Canaux de préchargement
- Empileur/dépileur de palettes
- Navette de tri
- Quais de déchargement et d’expédition
La marchandise provenant de l’unité de production entre dans l’entrepôt via des quais surélevés. Le déchargement des camions se fait à l'aide de chariots élévateurs qui permettent d’insérer les palettes directement dans le circuit d’entrée.
Dans cet entrepôt, la plupart des palettes utilisées sont d’une qualité insuffisante et le poids des produits est très élevé. Voilà pourquoi un ensemble d’empileur de palettes qui déposent la marchandise sur des palettes esclaves a été installé.
Par la suite, la marchandise passe par le poste d'inspection où l’on vérifie qu’elle respecte les exigences définies pour le projet avant d'entrer dans l'entrepôt.
Sorties de l'entrepôt
Les palettes préparées pour leur expédition quittent l'entrepôt par l’étage inférieur et rejoignent le circuit principal de convoyeurs qui les déplacent jusqu’à la zone d’expédition.
Une navette double transporte les palettes avec la charge et les classe en douze canaux de préchargement. Ces derniers sont composés de convoyeurs à chaînes et d’une table tournante aux extrémités. Les palettes peuvent ainsi être chargées par le côté adapté en fonction de leur emplacement dans le véhicule de transport.
Ce système permet de grouper les palettes d’une même commande ou d’un même itinéraire et d’accélérer les opérations de chargement dans les camions de distribution.
Easy WMS de Mecalux
Le logiciel de gestion d'entrepôt Easy WMS de Mecalux a été installé dans le centre logistique de Ceramika Paradyż, dont la mission est de diriger toutes les opérations internes.
Dans la mesure où l'entrepôt est entièrement automatisé, le module de contrôle Galileo a également été installé. Il contrôle le bon fonctionnement de tous les dispositifs mobiles utilisés et le respect des mesures de sécurité.
Easy WMS de Mecalux est en communication permanente et bidirectionnelle avec l'ERP de Ceramika Paradyż : les deux se transmettent des données et des informations essentielles pour exploiter et gérer l'entrepôt efficacement et pour obtenir la rentabilité maximale des processus logistiques.
Les avantages pour Ceramika Paradyż
- Performance maximale : l'entrepôt automatique de Ceramika Paradyż garantit un flux constant de produits et un système de préparation de commandes très rapide, avec une intervention minimale des opérateurs qui permet d’éliminer les risques.
- Grande capacité de stockage : l'entrepôt autoportant de 3 290 m2 et de 25 m de hauteur permet de stocker plus de 20 200 palettes d’un poids unitaire maximal de 1 500 kg.
- Système de gestion d'entrepôt WMS : les opérations de l'entrepôt sont pilotées et organisées par Easy WMS de Mecalux et le logiciel de commande Galileo, dont la fonction est de donner des ordres de mouvement à tous les dispositifs de l’installation.
Entrepôt automatique haute performance pour Ceramika Paradyż Sp. z o.o. | |
---|---|
Capacité de stockage: | 20 256 palettes |
Dimensions de la palette: | 800 x 1 200 mm et 800 x 1 250 mm |
Poids max. par palette: | 1 500 kg |
Longueur de l'entrepôt: | 97 m |
Largeur de l'entrepôt: | 35 m |
Hauteur de l’entrepôt: | 25 m |
Nb. d'allées: | 8 |
Galerie

Demandez conseil à un expert