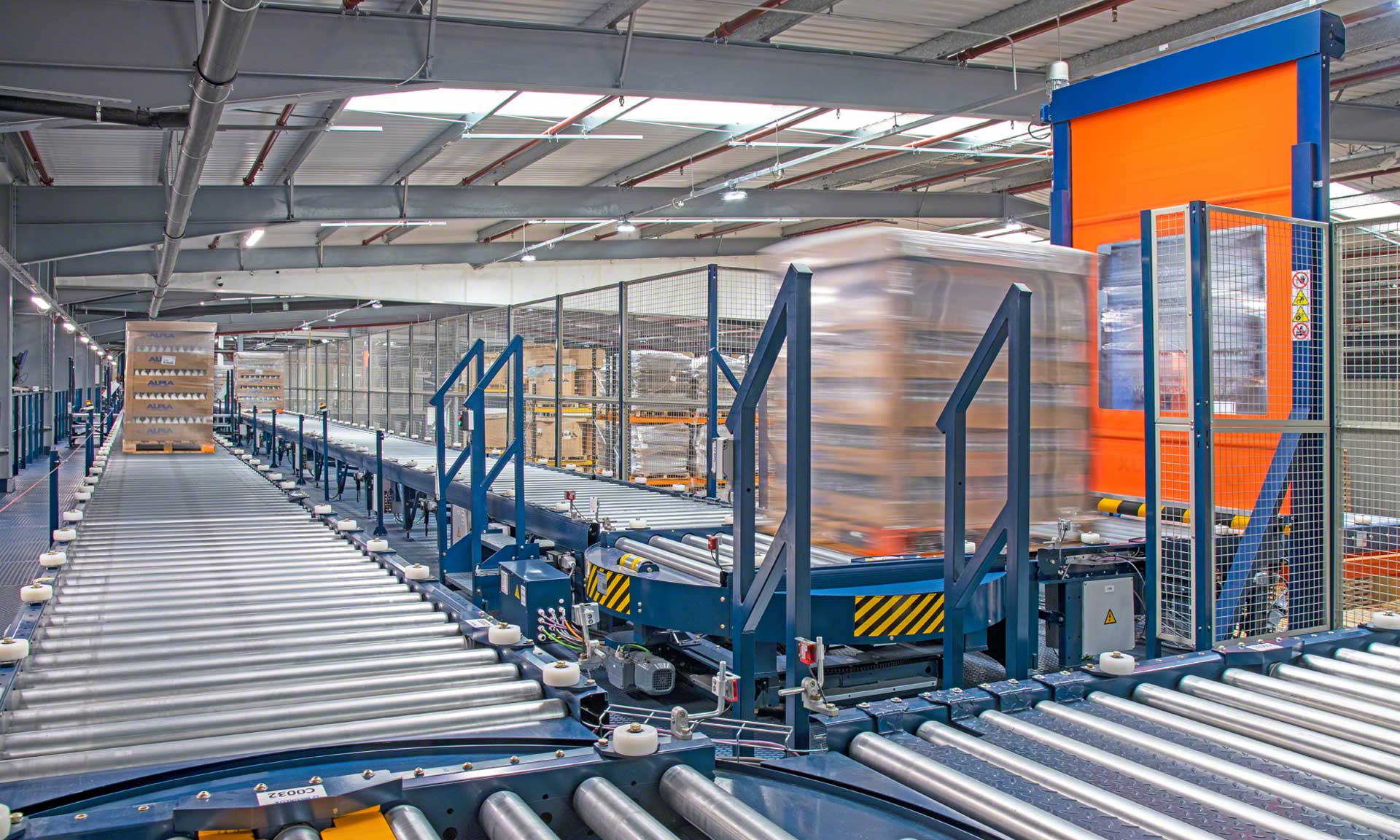
ALPLA installe des convoyeurs automatiques dans son usine de Golborne (Royaume-Uni)
ALPLA, leader en solutions d'emballage plastique, déplace chaque jour 2 500 palettes grâce au circuit de convoyeurs automatiques.
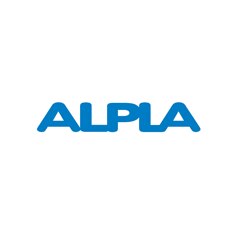
ALPLA a installé un circuit de convoyeurs automatiques pour relier son entrepôt aux ligne de production de son centre de Golborne. Le leader mondial des solutions d'emballage plastique peut déplacer chaque jour 2 500 palettes grâce aux convoyeurs automatiques.
ALPLA : des solutions d’emballage innovantes
Fondée en Autriche, ALPLA est l’un des leaders mondiaux dans le domaine des solutions d’emballage. L’entreprise est mondialement reconnue pour ses emballages en plastique et leur qualité. Ils sont utilisés dans un large éventail d’industries telles que l’alimentaire, le secteur pharmaceutique ou cosmétique. La priorité de l’entreprise est le développement d’une activité durable et respectueuse de l’environnement grâce à ses usines de recyclage.
- Année de création : 1955
- Présence internationale : 45 pays
- Sites de production : 177
- Effectif : 22 100
- Chiffre d’affaires : 4 milliards d’euros en 2021
DÉFIS
|
SOLUTIONS
|
AVANTAGES
|
---|
Comment relier automatiquement un entrepôt à une usine de production lorsque les deux bâtiments sont séparés par une distance de 70 m et une route ? ALPLA, leader en solutions d’emballage, a relevé ce défi grâce à une solution Mecalux. « Grâce à la solution logistique installée, comprenant des convoyeurs et des élévateurs pour palettes, nous avons considérablement réduit nos coûts de manutention et nos émissions de dioxyde de carbone. Notre activité est désormais plus durable et plus respectueuse de l’environnement », explique Liam Grimwood, directeur ingénierie de l’usine britannique d’ALPLA.
Présente dans 45 pays, ALPLA a réalisé un chiffre d’affaires de quatre milliards d’euros en 2021, soit 8,4 % de plus par rapport à l’année précédente. Au Royaume-Uni, l’entreprise mène un projet de croissance sans précédent et dispose, depuis quelques années, d’une usine de production moderne à Golborne.
Le complexe logistique est composé de deux bâtiments séparés par une voie publique : l’un destiné aux lignes de production, l’autre à la zone de stockage. « Auparavant, nous dépendions largement des véhicules lourds pour transporter manuellement les marchandises du site de production à l’entrepôt », explique M. Grimwood.
Au fur et à mesure de la hausse des volumes, les allers-retours des camions entre le bâtiment de production et celui de stockage d’ALPLA augmentaient aussi. Cette méthode est vite devenue intenable. « Nous avions besoin d’un système pour connecter les deux bâtiments et déplacer automatiquement les marchandises de l’usine de production vers l’entrepôt. Nous voulions abandonner la manutention manuelle et les véhicules lourds », reconnaît le directeur ingénierie de l’usine britannique d’ALPLA.
La solution aux besoins d’ALPLA a été la construction d’un tunnel surélevé de huit mètres de haut au-dessus de la voie publique pour relier l’usine de production à la zone de stockage. « Nous avons choisi Mecalux en raison des bons retours d’expériences sur des projets similaires. Le savoir-faire et les compétences de l’équipe technique et du chef de projet qui nous ont accompagnés et conseillés tout au long du projet, ont également été décisifs », reconnaît M. Grimwood.
Communication par des systèmes automatisés
« Chaque jour, nous déplaçons environ 2 500 palettes grâce à un système de transport automatisé qui fonctionne 24 heures sur 24, sept jours sur sept », explique M. Grimwood.
Le système installé par Mecalux consiste en un double circuit de convoyeurs assurant le transfert des marchandises de la production à l’entrepôt. « Sa fonction principale est de transporter des palettes contenant des plateaux en carton avec des bouteilles vides, des caisses et conteneurs métalliques avec des préformes en polyéthylène téréphtalate », explique le directeur ingénierie de l’usine britannique d’ALPLA. À l'avenir, la solution choisie pourrait transporter jusqu'à 5 000 palettes par jour, c'est-à-dire qu'ALPLA doublerait ses flux entre l'usine de production et l'entrepôt.
Les convoyeurs sont un système automatisé de transport de marchandises composé d’une série de rouleaux supportant la charge et l’entraînant le long du circuit. Le système est équipé de moteurs électriques pour déplacer les unités de charge de manière contrôlée et sécurisée. Les convoyeurs à rouleaux offrent un gain de temps et d’efficacité lors des transferts de charges répétitifs et sur des circuits préétablis.
Outre les convoyeurs, sept élévateurs automatiques ont été installés pour monter et descendre les palettes. Ils servent à combler l’écart existant entre le circuit de convoyage au rez-de-chaussée et le tunnel surélevé. De cette manière, les palettes sont déplacées de l’usine de production à l’entrepôt, le tout de manière entièrement robotisée.
En tête du circuit de convoyage et à l’endroit où les palettes quittent les lignes de production, un point d’inspection des entrées (PIE) a été installé. Ce système automatisé dle contrôle du gabarit et de la qualité des palettes est essentiel pour garantir le déplacement en toute sécurité des marchandises et des palettes. Le PIE vérifie que les dimensions, le poids et l’état des palettes sont conformes aux spécifications de l’installation.
Principaux composants des convoyeurs à rouleaux
- Rouleaux. Cylindres métalliques comprenant un axe et deux roulements. Placées l’un après l’autre, ils supportent le poids de la palette et la déplacent jusqu’à la fin du parcours.
- Structure et pieds en métal. Ils constituent le support des rouleaux, ils sont fabriqués en différents types d’acier selon le poids à supporter. Sa fonction étant de dessiner le circuit de convoyage.
- Composants électriques. Le déplacement des charges dans le circuit est entraîné par un ensemble de composants électriques, ainsi que par des moteurs et des boîtiers de puissance. La puissance nécessaire dépend de la vitesse requise et du poids des charges à déplacer.
- Éléments de sécurité. Les dispositifs mécaniques ou les capteurs, tels que les butées ou les cellules photoélectriques de détection, sécurisent l’installation. Aussi, ils permettent de connaître à tout moment où se trouve la charge et de communiquer cette information au logiciel de contrôle.
Une logistique de production performante
« ALPLA Golborne est en position de force et de croissance durable », déclare M. Grimwood. Pour consolider davantage sa présence sur le marché britannique, l’entreprise favorise la méthodologie lean dans sa logistique, c’est-à-dire qu’elle encourage les activités apportant de la valeur ajoutée à l’entreprise afin d’augmenter le flux de produits et de minimiser les coûts.
La solution Mecalux a permis à ALPLA de disposer d’une logistique performante reliée à la production par des systèmes de transport automatisés. En effet, l’industrie d’aujourd’hui exige un système de fabrication flexible et diversifié dans lequel le service efficace au client dépend des bons rouages de la logistique de production. Grâce à la solution installée, la chaîne d’approvisionnement d’ALPLA est plus efficace, optimisée et prête à relever les défis d’aujourd’hui et de demain.
Grâce à la solution de transport automatisé installée par Mecalux, nous avons réduit les coûts et les émissions de CO2 et sommes en mesure de transporter environ 2 500 palettes par jour, 24 heures sur 24 et 7 jours sur 7.
Galerie
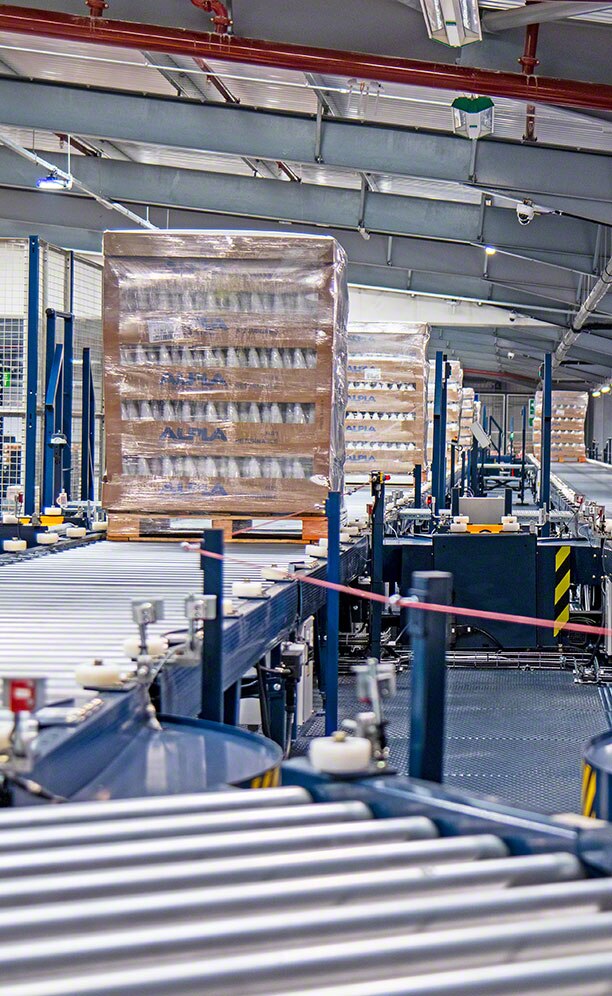
Convoyeurs automatiques pour palettes dans le centre logistique de ALPLA
Demandez conseil à un expert