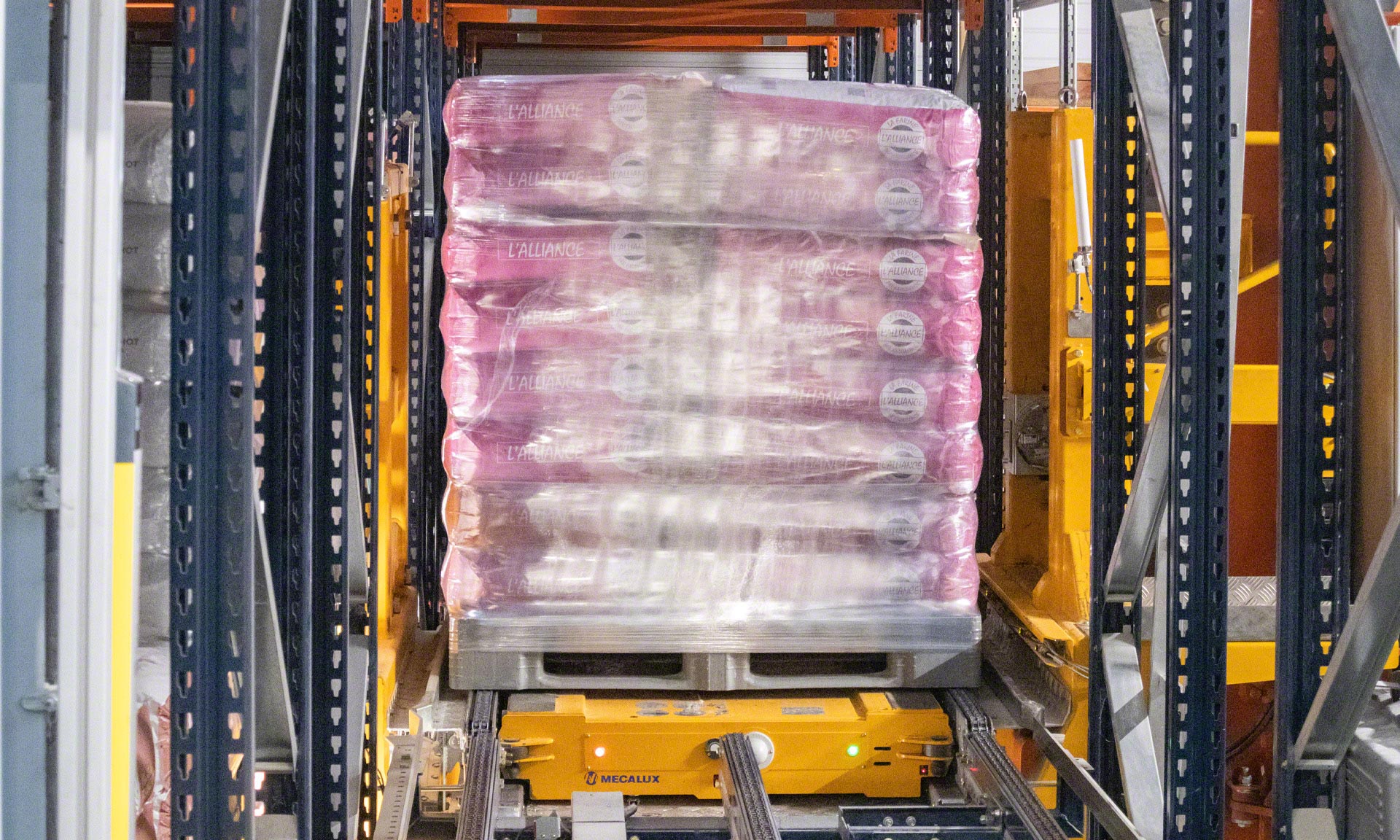
Minoterie Planchot automatise son entrepôt de stockage de farine de Saint-Paul-en-Pareds
Le meunier, Minoterie Planchot, optimise le stockage de sacs de farine et la préparation des commandes à l’aide du système Pallet Shuttle automatique, un robot de picking et du logiciel Easy WMS.
Minoterie Planchot, un fabricant de farine français renommé, a automatisé son usine de production de Saint-Paul-en-Pareds (France). L’entreprise a automatisé le stockage des produits finis à l’aide du système Pallet Shuttle automatique et du logiciel de gestion Easy WMS.
Cinq générations de meuniers
Minoterie Planchot, entreprise familiale française basée à Saint-Paul-en-Pareds (Vendée), est spécialisée dans la production de farines pour boulangerie, pâtisserie et viennoiserie. Collaborant étroitement avec les agriculteurs locaux, elle met en œuvre des pratiques durables garantissant la qualité de ses produits. Reconnue dans le secteur pour son engagement en matière de traçabilité, Minoterie Planchot propose une large gamme de farines traditionnelles et biologiques, adaptées aux besoins des artisans boulangers et des industriels de l’agroalimentaire. Fondée en 1912, la Minoterie Planchot produit 100 000 tonnes de farine par an.
DÉFIS
|
SOLUTIONS
|
AVANTAGES
|
---|
Avec une production annuelle de 100 000 tonnes de farine de blé 100 % françaises, Minoterie Planchot s’impose comme l’un des leaders de l’industrie meunière en France. Depuis son usine moderne de Saint-Paul-en-Pareds, le fabricant approvisionne aussi bien les artisans boulangers, les grandes surfaces que les industriels agroalimentaires ainsi qu’à l’export.
À la suite de la hausse de 35 % de son volume de production, couplée à une diversification croissante de ses produits, la minoterie Planchot a repensé sa logistique. Yves Fradin, directeur industriel, se souvient : « Auparavant, nous stockions et déplacions les palettes manuellement. Nous disposions d’une simple zone de stockage au sol et de rayonnages classiques. Nous avions besoin d’une solution pour automatiser la manipulation des palettes de sacs de farine issus de la production et accélérer la préparation des commandes sur des palettes complètes ou mixtes ».
Mecalux a dynamisé la logistique de Minoterie Planchot grâce à une solution intégrée comprenant le système Pallet Shuttle, un robot de picking et le logiciel de gestion d’entrepôt Easy WMS. « La robotisation nous a apporté de nombreux avantages, notamment une augmentation de la productivité et une réduction significative de la manipulation des produits », déclare Yves Fradin.
Les performances offertes par les systèmes de stockage ont été déterminantes : « Nous avons sélectionné Mecalux comme prestataire logistique après avoir visité l’entrepôt d’une entreprise de notre secteur et constaté par nous-mêmes l’efficacité de leurs systèmes de stockage ».
Productivité et ergonomie
« La fonction principale de l’entrepôt automatisé est de stocker les produits finis, les ingrédients et les emballages, tout en facilitant la préparation des commandes », précise Yves Fradin.
Le système Pallet Shuttle automatique dans l’usine de Minoterie Planchot se distingue par sa conception compacte : une seule allée de 30 mètres de long et des rayonnages de 18 mètres de haut allient performance et grande capacité dans un espace optimisé. L’entreprise parvient ainsi à stocker jusqu’à 1 189 palettes de sacs de farine sur seulement 260 m².
En suivant cette stratégie de maximisation de l’espace, les postes d’entrée et de sortie des marchandises ont été aménagés sur les côtés de l’entrepôt, ce qui permet d’optimiser les flux logistiques sans compromettre la capacité de stockage.
« Chaque jour, nous recevons et expédions environ 250 palettes », explique le directeur industriel de Minoterie Planchot. « Grâce aux convoyeurs automatiques, 90 % de nos opérations de manutention sont effectuées sans intervention manuelle, ce qui a réduit l’effort physiques et amélioré l’efficacité ».
Un autre processus logistique optimisé par la robotisation est la préparation de commandes de sacs de farine. Pour cette opération, une navette fait office de tampon et un robot de picking charge automatiquement les sacs, améliorant ainsi l’ergonomie et la productivité. « L’automatisation a réduit de 80 % l’effort physique. En effet, aujourd’hui, 85% des commandes sont préparées par le robot de picking », se réjouit Yves Fradin.
« Chaque jour, nous préparons une trentaine de commandes qui sont expédiées sur 125 palettes à destination du nord-ouest de la France et des marchés d’export », ajoute le directeur industriel de la minoterie Planchot.
Traçabilité de 250 références
Le logiciel de gestion Easy WMS gère les entrées et les sorties de produits, garantissant ainsi une traçabilité totale des 250 références stockées. De cette façon, Minoterie Planchot maîtrise rigoureusement chaque palette de l’entrepôt, facilitant l’identification précise des lots et le suivi de chaque SKU, de la production jusqu’au client final.
La traçabilité assure un contrôle rigoureux et méthodique de la qualité des marchandises réceptionnées. Les opérateurs, munis de terminaux radiofréquence, procèdent à l'inspection des articles en renseignant un questionnaire portant sur des critères essentiels tels que le type de support de charge, la conformité des documents fournisseurs (par exemple, la présence de la mention BIO) et la présence d'échantillons. La digitalisation de ce processus permet une identification rapide des marchandises non conformes, lesquelles sont ensuite isolées dans une zone dédiée à leur traitement.
L’intégration d’Easy WMS à l’ERP de Minoterie Planchot a permis de synchroniser en temps réel la production et la logistique. Désormais, l’entrepôt connaît à l’avance les informations sur les produits finis et sur les références à expédier. Grâce à cette synchronisation, l’entreprise a amélioré son efficacité et réduit les délais de traitement des commandes.
Un bond dans l’avenir
La solution complète de Mecalux, la Minoterie Planchot a transformé sa logistique afin de faire face efficacement à la croissance de 35 % de sa production. En automatisant des processus clés, le fabricant de farine a augmenté sa réactivité face à la demande et a optimisé la gestion logistique de ses 250 références. En somme, la traçabilité, l’amélioration de l’ergonomie et le gain de capacité de stockage sont désormais des piliers fondamentaux de la stratégie future de Minoterie Planchot.
La robotisation nous a apporté de nombreux avantages, notamment une augmentation de la productivité et une réduction significative de la manipulation des produits.
Galerie
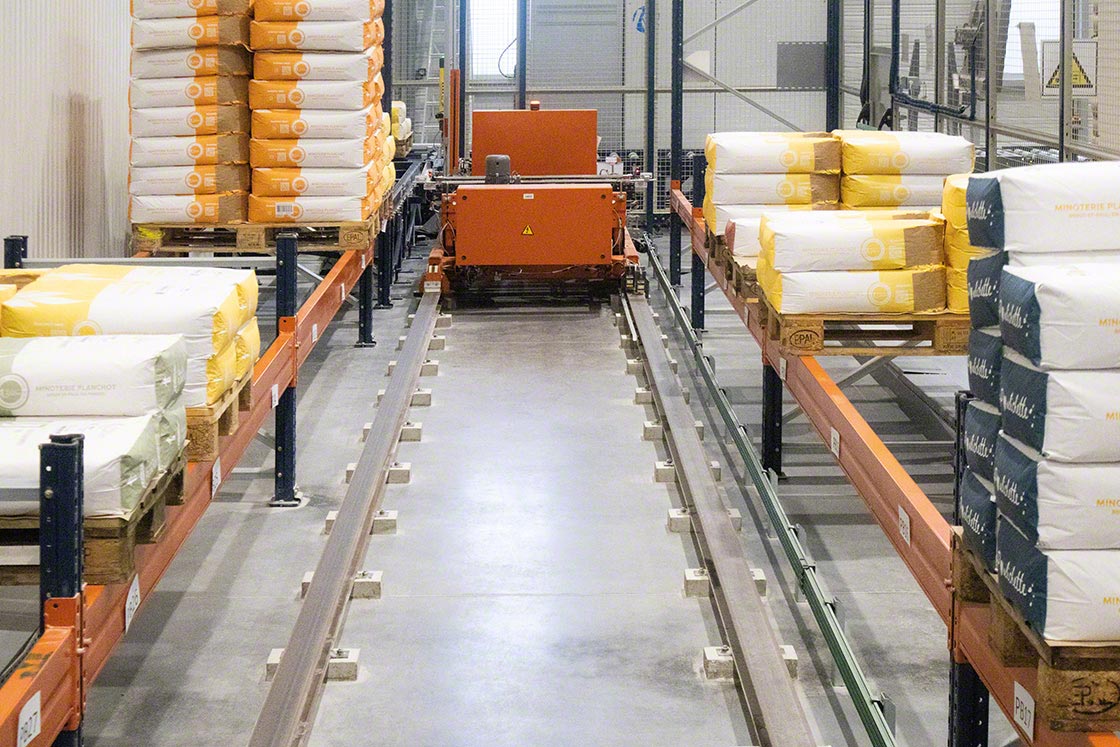
Minoterie Planchot accélère le transport des sacs de farine à l’aide de convoyeurs
Demandez conseil à un expert