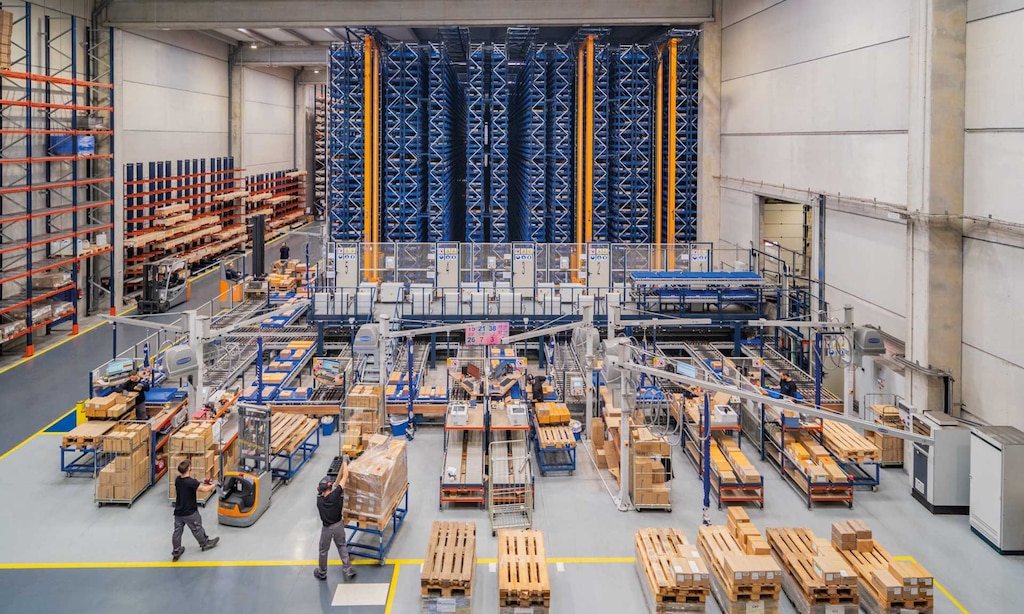
DOSSIER LOGISTIQUE
Diego Pacheco, Daniel Møller Clausen et Jendrik Bumann
Les entrepôts constituent un pilier central de la chaîne d’approvisionnement et de l’expérience client finale. Cependant, les responsables de ces installations sont confrontés en permanence à des difficultés qu’ils doivent gérer au quotidien. Parmi les plus critiques figurent les contrôles qualité insuffisants, les processus redondants, les conceptions non conformes et l’inexactitude des informations sur les stocks. Sans mesures correctives, chacun de ces aspects peut entraîner des coûts supplémentaires, des pertes de performances et générer une insatisfaction chez les utilisateurs.
Dans le système de production Toyota, les activités non génératrices de valeur ajoutée sont appelées « muda » (gaspillage). Parmi les sept types de gaspillage identifiés figurent les temps d’attente, la surproduction, la manutention excessive de marchandises, les transferts inutiles, les mauvais traitements, les défauts et le surstockage.
Prendre conscience de l’état actuel de son entrepôt est une étape essentielle pour identifier les gaspillages qui s’y produisent. Ceci s’obtient par l’analyse de données, l’observation des entrepôts, des entretiens ou des sondages, l’analyse de Pareto des produits et des outils « lean » telles que la cartographie de la chaîne de valeur (VSM) ou le Genba Shikumi, un outil quantitatif basé sur des vecteurs et des matrices de corrélation successive, entre autres méthodes. Et si l’on recherche une haute performance et compétitivité dans les opérations, il est nécessaire de mettre en œuvre des programmes d’amélioration continue.
Les goulets d’étranglement des entrepôts de distribution
Dans cette étude, nous avons examiné le fonctionnement d’un entrepôt de distribution d’une PME danoise qui opère en Europe et vend des produits en B2B et en B2C. L’installation emploie un responsable d’entrepôt à temps plein et un assistant à temps partiel. Dans un premier temps, des stratégies ont été développées pour identifier et réduire les gaspillages opérationnels, puis les conclusions ont été appliquées à cette entreprise.
Lors des premières prises de contact, notre équipe de recherche a constaté que la direction était consciente que plusieurs problèmes opérationnels affectaient les performances de l’activité. Sans réponse proactive à cette situation, ces difficultés risquaient d’entraver la capacité de développement de l’entreprise sur le marché.
La collecte des données à analyser s’est déroulée en plusieurs phases. Tout d’abord, un entretien a eu lieu avec le propriétaire de l’entreprise afin de comprendre l’organisation, son personnel et les problématiques de l’installation. Ensuite, trois visites ont été réalisées et davantage d’observations ont été recueillies. Un questionnaire a également été distribué pour collecter des informations auprès des fournisseurs et sur les expéditions, et des rapports de ventes et d’inventaires ont servi à déterminer la rentabilité de chaque famille de produits.
L’identification des mauvais traitements
Nous avons constaté qu’en l’absence de pluie, le déchargement et le tri des marchandises pouvaient avoir lieu en extérieur, offrant ainsi plus d’espace. Concernant le processus d’emballage et d’expédition, le facteur le plus déterminant était la disponibilité de cartons et de matériaux de calages appropriés. À l’arrivée d’un camion, il n’existait aucun système pour localiser les références, et lors de la préparation des commandes, la marchandise était parfois introuvable. Dans ces cas, le préparateur cherchait l’article, demandait l’aide d’un collègue ou considérait la commande comme terminée sans certains produits. En l’absence d’un emballage, l’opérateur devait se procurer un carton dans l’entrepôt.
En moyenne, l’entreprise expédie 128 produits par jour en un seul envoi. Tous les deux mois, elle reçoit de son principal fournisseur 9 715 articles répartis dans 367 colis, et bien que la communication avec ce dernier se fasse par e-mail, le flux d’informations au sein de l’entreprise reste manuel.
Sans un système de gestion des références, l’ensemble des informations sur les stocks repose sur le responsable, exposant ainsi l’entreprise à des risques en cas d’absence prolongée de celui-ci
Avec un seul employé à temps plein, le personnel de bureau doit aider au déchargement des camions. Si l’opération dure plus d’une heure, des frais supplémentaires doivent être payés au transporteur et, sans équipement adapté, l’épuisement physique est assuré. Par ailleurs, le chargement étant effectué de manière aléatoire, les produits ne sont triés par catégorie que lors du déchargement, ce qui prend un temps considérable.
À défaut d’un système de gestion des références, l’ensemble des informations sur les stocks repose sur le responsable, exposant ainsi l’entreprise à des risques en cas d’absence prolongée de celui-ci. Le manque d’informations sur les stocks et une formation limitée entraînent de nombreuses questions de la part des opérateurs, ce qui entrave le travail du responsable et du personnel de bureau.
Quant au picking, le processus démarre lorsqu’un employé de l’entrepôt récupère un bon de commande. Il l’utilise ensuite comme picking list et le dépose dans un plateau. Nous avons constaté que lorsqu’une nouvelle commande était placée sur le haut du plateau au lieu du bas, cela entraînait des retards pour les commandes précédentes. Par ailleurs, les étiquettes apposées sur les cartons sont petites et peu claires, rendant leur lecture difficile. Les cartons sont empilés les uns sur les autres, ce qui complique leur manipulation. Sans un système de gestion d’entrepôt, les opérateurs se fient à leur mémoire pour déterminer l’itinéraire le plus rapide, un défi supplémentaire pour les employés temporaires.
Résultats et cartographie de la chaîne de valeur
Les résultats ont révélé que la majorité des processus de l’entrepôt étaient perfectibles. Malgré sa croissance, l’entreprise n’a pas modifié ses méthodes de travail, ce qui a engendré de nombreux problèmes, tels que la double manutention (double handling) des marchandises. De plus, les opérateurs ne reçoivent pas de retour de la part des clients sur leur travail et ne peuvent donc pas identifier les erreurs commises.
L’étude a identifié que les trois sources principales de gaspillage de cette entreprise danoise étaient les temps d’attente, la manutention excessive des marchandises et les transferts inutiles. Outre les opérations générales, le déchargement et le tri des articles sont les domaines nécessitant des mesures urgentes. En conséquence, une série de changements a été proposée pour améliorer le fonctionnement de l’entrepôt, changements qui sont illustrés sur la future cartographie de la chaîne de valeur (voir figure).
Le changement majeur proposé dans la nouvelle cartographie de la chaîne de valeur est la mise en œuvre d’un logiciel de gestion d’entrepôt (WMS). Ce système améliore l’ensemble de la chaîne de valeur et intègre les données de toutes les références. Il fournit des informations anticipées sur les expéditions des fournisseurs, ce qui permet aux employés d’être prêts avant les réceptions. Il assure également une occupation optimale de l’espace de stockage en attribuant un emplacement à chaque produit avant sa réception, et dans cette configuration, il serait connecté à des systèmes de voice picking (picking vocal). Capable de lire les avis préalables d’expédition (ASN), il émet aussi des alertes relatives aux processus de déchargement et de tri.
Une autre conclusion a été la nécessité d’établir des procédures normalisées d’exploitation (PNE) pour le fournisseur, les processus de déchargement et de tri, ainsi que pour l’emballage. Ces procédures incluent notamment des exigences relatives à la taille et à la visibilité des étiquettes, ainsi qu’à la manière de structurer les références avant une expédition.
Utiliser un logiciel de gestion d’entrepôt
L’utilisation d’un WMS aurait un impact positif sur toutes les opérations de l’entrepôt, qu’il soit utilisé seul ou intégré à un progiciel de gestion intégré (PGI ou ERP en anglais). La mise en œuvre d’un WMS peut réduire les temps d’attente, la manutention excessive des marchandises et les transferts inutiles. Par ailleurs, l’élaboration de ventes prévisionnelles contribue à une meilleure précision des niveaux de stocks et évite la freinte de stock.
Un logiciel de gestion d’entrepôt peut résoudre les problèmes de slotting et prévoir l’emplacement des nouvelles références en suivant la méthode ABC. Il s’assure que les produits les plus lourds sont stockés à proximité des postes de picking, tandis que ceux qui sont souvent vendus ensemble sont placés les uns à proximité des autres. Enfin, un WMS peut également servir d’outil de planification grâce à sa capacité à déterminer s’il y a suffisamment de cartons de différentes tailles pour l’emballage des articles.
Les performances de l’entrepôt impactent plusieurs domaines : l’amélioration des processus bénéficie à l’entreprise dans son ensemble
L’étude et la compréhension de l’origine du gaspillage opérationnel permettent aux employés de prendre conscience de l’importance de leur rôle et de gagner ainsi en bien-être au travail. Les résultats de l’étude montrent que la mise en œuvre de techniques de diminution du gaspillage entraîne une meilleure allocation des ressources, ce qui stimule la croissance de l’entreprise et favorise les nouvelles opportunités commerciales.
Les performances de l’entrepôt ont une incidence sur plusieurs domaines, et l’amélioration de ses processus apporte des avantages à l’entreprise dans son ensemble. En ce sens, la cartographie de la chaîne de valeur du distributeur danois révèle un temps de production total de 1 721,29 heures, qui, après la mise en œuvre d’un WMS et l’introduction d’améliorations dans toutes les opérations, serait réduit de 41,4 %.
AUTEURS DE LA RECHERCHE :
Diego Pacheco, Daniel Møller Clausen et Jendrik Bumann. Département du développement des entreprises et technologie, École de commerce et de sciences sociales, Université d’Aarhus (Danemark).
Publication originale :
Jesús Pacheco, Diego Augusto, Møller Clausen, Daniel, Bumann, Jendrik. 2023. « A multi-method approach for reducing operational wastes in distribution warehouses», International Journal of Production Economics 256 (Elsevier).
© The Authors. Licensed under CC BY 4.0