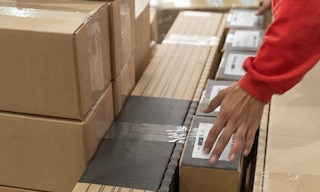
Le « double handling », un exemple de gaspillage dans la logistique « lean »
Le double handling est une pratique qui consiste en la manipulation excessive de marchandises et qui impacte négativement la productivité d’une installation logistique. En effet, les inefficacités lors du déplacement des marchandises ou de la préparation des commandes entraînent des surcoûts, des pertes de matériaux, des livraisons en retard… Il en résulte un service de moindre qualité au client final.
L’introduction de nouvelles technologies dans l’entrepôt réduit l’impact du double handling. Un logiciel de gestion d’entrepôt (WMS) guide les opérateurs dans leurs tâches, automatise la prise de décision et assure l’exécution des commandes dans les meilleurs délais et avec une productivité maximale. Aussi, les solutions robotiques telles que les convoyeurs, les robots mobiles ou les équipements de manutention automatisés évitent la manipulation excessive des marchandises, puisqu’ils suppriment les mouvements inutiles et garantissent un fonctionnement à plein régime de l’installation.
Qu’est-ce que le « double handling » dans l’entrepôt ?
L’effet double handling est lié à des inefficacités dans le réapprovisionnement ou la préparation des commandes. Cela veut dire que les opérateurs effectuent des mouvements en trop ou consacrent trop de temps lors du transport interne des marchandises. Cette mauvaise pratique est due, en partie, au manque d’itinéraires optimisés dans l’installation logistique, ce qui implique une perte de temps et augmente le risque de dommage aux marchandises ou aux systèmes de stockage pendant les transferts.
Les processus et déplacements superflus dans l’entrepôt allongent les délais d’exécution des commandes, le service au client final étant donc impacté. Un exemple de double manutention dans un entrepôt de marchandises palettisées est présenté dans l’article de recherche An efficient approach to investigate the tradeoff between double handling and needed capacity in automated distribution centres : « Il y a double manutention lorsque la demande quotidienne est inférieure à la taille de la palette et qu’il n’est extrait qu’une partie des cartons (à l’aide de dépalettiseurs), le reste demeurant stocké pour les besoins ultérieurs ». En minimisant la double manutention, les entreprises peuvent améliorer leur service logistique, assurer des livraisons à temps et, par conséquent, gagner une plus grande part de marché.
« Double handling », Muda et la méthode Lean
La double manipulation des produits et les déplacements inutiles des opérateurs sont deux exemples de « gaspillage lean ». En ce sens, la méthode du lean logistics vise à identifier et à éliminer les activités et les processus qui n’apportent pas de valeur ajoutée et qui sont susceptibles d’affecter l’efficacité des procédures. Une mauvaise planification des itinéraires dans l’entrepôt, par exemple, peut signifier des déplacements inutiles et donc des inefficacités dans la préparation des commandes.
Dans le contexte du lean, le terme muda est courant pour décrire tout processus provocant une sorte de gaspillage ou qui n’apporte pas de valeur ajoutée au produit ou service. La double manutention augmente les coûts et implique des inefficacités logistiques. Mais, les déplacements en trop ne représentent pas le seul muda pouvant exister dans l’entrepôt. Une accumulation injustifiée de marchandises et, en général, une mauvaise gestion des stocks, peuvent également donner lieu à une perte d’espace ou à l’obsolescence des produits stockés.
Quelles sont les causes du « double handling » ?
Lors de leur réception dans l’entrepôt, les marchandises doivent suivre un itinéraire prédéfini pour éviter tout déplacement ou manipulation injustifié. En général, les causes principales du double handling sont les suivantes :
- Absence de stratégie d’emplacement et de réapprovisionnement des produits. Une planification non optimale des stocks se traduit souvent par un stockage au mauvais endroit, occupant un emplacement destiné à d’autres produits, ce qui oblige à repositionner les articles ailleurs.
- Problèmes de communication entre l’entrepôt et les autres départements de l’entreprise, tels que la production. Une mauvaise communication peut générer des goulets d’étranglement ou un manque de stock aux lignes de production.
- Manque d’espace de stockage ou, à défaut, une mauvaise distribution des produits. Les erreurs concernant la planification logistique ou l'agencement de l’entrepôt peuvent conduire à des déplacements inutiles d’opérateurs et de marchandises.
- Mauvaise utilisation d’aménagements, de dispositifs d’assistance ou d’équipements de manutention. Dans un entrepôt traditionnel, par exemple, l’utilisation de chariots élévateurs inadaptés peut ralentir les opérations.
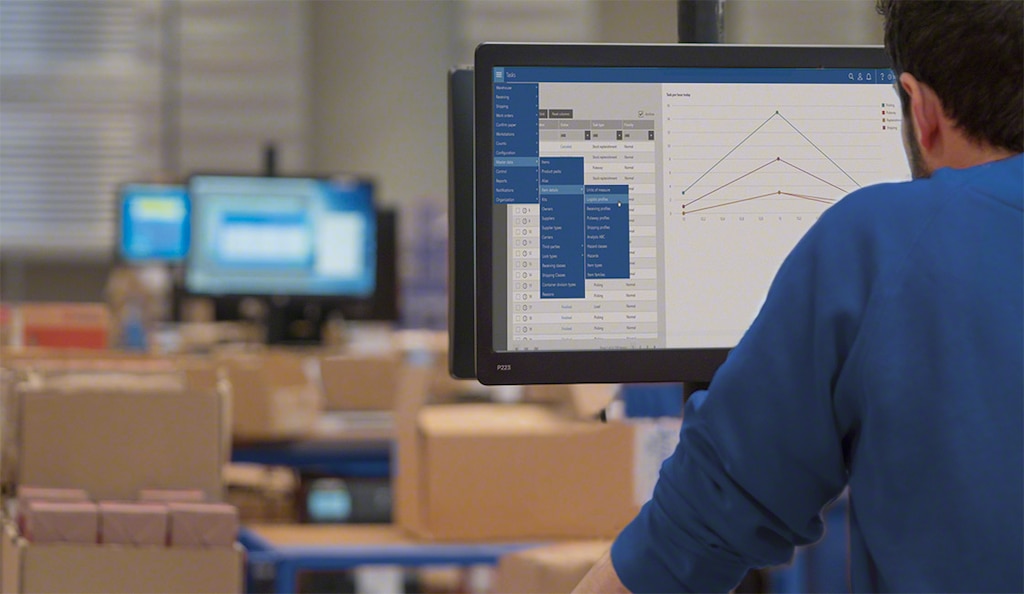
Comment réduire le « double handling » ?
Pour éviter la double manipulation des marchandises et les déplacements inutiles, il est conseillé d’opter pour une solution numérique telle qu’un logiciel de gestion d’entrepôt. Ce programme logistique coordonne le fonctionnement de l’installation dans son ensemble, y compris l’attribution des emplacements de stockage. Le logiciel détermine, sur la base d’un ensemble de règles et de critères préétablis par le responsable logistique, le meilleur emplacement. Le risque d’inefficacité (erreurs ou doubles manipulations) est ainsi diminué lors du réapprovisionnement.
Un logiciel de gestion avancée prend également en charge la planification des itinéraires de picking et des trajets des engins de manutention, et ce, avec un double objectif : l’efficacité et la sécurité des déplacements des opérateurs et des marchandises. Pour déterminer l’itinéraire à suivre par chaque opérateur et maximiser ses performances, l’outil tient compte du nombre de commandes à préparer, mais aussi de la distribution des produits.
Les solutions automatisées telles que les convoyeurs, les transstockeurs ou les robots mobiles éliminent le risque de double manutention et assurent un déplacement optimisé des marchandises. Dans une installation équipée ainsi, le logiciel de gestion joue le rôle de cerveau qui coordonne les mouvements des engins robotiques et des marchandises. Les solutions robotiques permettent l’application d’une stratégie goods-to-person, selon laquelle les produits sont acheminés aux opérateurs en toute autonomie. En bref, l’automatisation réduit le nombre de déplacements et de manipulations pour garantir une rentabilité maximale des opérations de l’entrepôt.
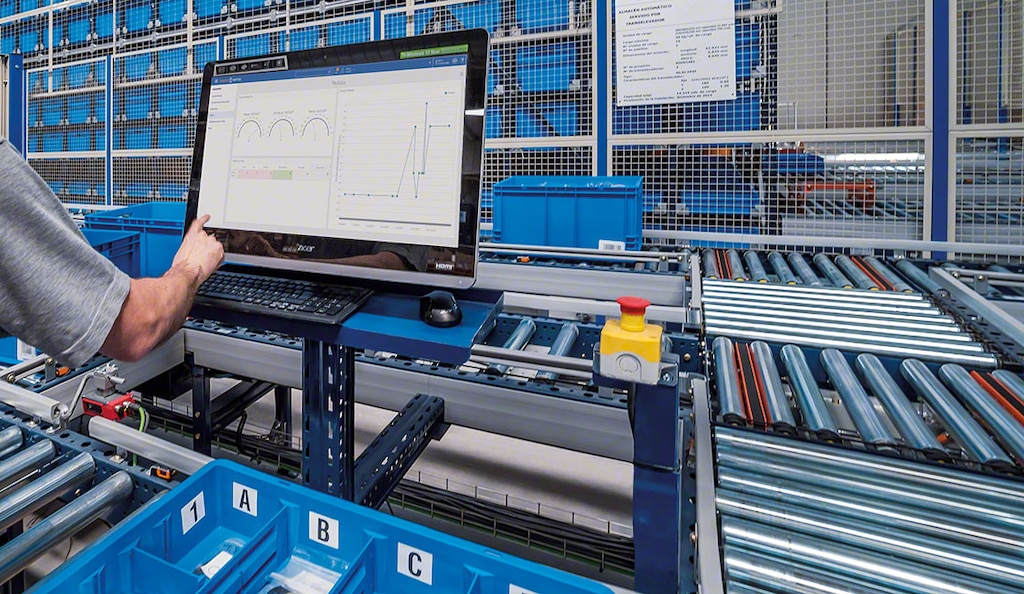
Des solutions avancées pour éviter les inefficacités dans l’entrepôt
Le manque de déplacements optimisés dans l’entrepôt est un symptôme évident de « gaspillage lean », et donc d’inefficacité logistique. En ce sens, les nouvelles technologies diminuent le risque d’erreur lié au double handling. Dans les entrepôts traditionnels, un logiciel de gestion comme Easy WMS coordonne la circulation de marchandises et d’opérateurs dans le but d’éviter les processus improductifs.
De même, le choix de solutions automatisées telles que des transstockeurs, des convoyeurs ou des robots mobiles signifie l’automatisation des déplacements de marchandises et renforce les performances de l’installation. Mecalux possède une vaste expérience dans la conception de solutions de stockage et logicielles pour tout type d’entreprise. Contactez-nous, un expert vous conseillera sur la meilleure solution pour votre entrepôt.