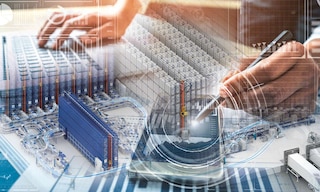
« Value stream mapping » : outil d’identification des inefficacités dans l’entrepôt
La value stream mapping (VSM, en anglais) est une méthode de visualisation des processus de fabrication d’un produit, depuis la réception des matières premières à la production, au stockage et à la livraison au client.
Généralement utilisé dans les centres de production et les entrepôts, cet outil facilite l’analyse des différentes étapes de production afin d’améliorer les processus.
VSM : qu’est-ce que la « value stream mapping » ?
La value stream mapping, également appelée cartographie de la chaîne de valeur, est un outil visuel conçu pour identifier les inefficacités et détecter les opportunités d’amélioration dans le processus de production et dans la gestion logistique d’un produit. Dans les années 90, cet outil a commencé à être utilisé dans les méthodologies de travail Lean et Six Sigma, qui partagent le même objectif : éliminer les surcoûts et mettre en place des systèmes de fabrication efficaces.
La VSM consiste en un organigramme qui représente les différentes activités et étapes par lesquelles passe un produit tout au long du processus de production, de l’achat de la matière première à la livraison au client final. Cet outil permet de visualiser le mouvement des matières premières et d’analyser l’efficacité des processus de production.
La cartographie de la chaîne de valeur enregistre chacune des activités et tâches nécessaires à la création et à la distribution d’un produit, de sorte que le responsable de la production peut isoler les processus qui n’apportent pas de valeur ajoutée au client. La VSM utilise un système de symboles qui reproduisent les flux d’informations, de travail et de mouvements générés tout au long de la supply chain (chaîne d’approvisionnement).
Pour identifier les erreurs et les inefficacités dans la fabrication d’un produit, l’équipe en charge de l’évaluation peut cartographier et comparer différentes versions de la VSM. Par exemple, un diagramme peut refléter le flux réel tandis qu’un autre peut illustrer l’état futur ou idéal. Cette comparaison permet de visualiser plus rapidement les opportunités d’amélioration et de savoir à quel stade spécifique du processus de production elles peuvent être mises en œuvre.
Avantages de l’utilisation de la technique VSM
La création d’une carte de la chaîne de valeur permet aux personnes chargées de superviser les processus de production, par exemple les responsables logistiques, de :
- Avoir une vue d’ensemble de la production : l’organigramme comporte des informations sur tous les processus impliqués dans la production, le responsable est ainsi mieux informé lorsqu’il prend des décisions.
- Identifier les inefficacités, les surcoûts et les erreurs : cet outil de Lean manufacturing aide à détecter les processus qui font augmenter les coûts ou qui n’ajoutent pas de valeur au produit. Cette analyse profite à la fois au fabricant et au client, car le résultat final est un produit ou un service amélioré.
- Favoriser une stratégie logistique et de production efficaces : la cartographie de la chaîne de valeur implique une analyse de l’état actuel du processus de production et une cartographie de l’état idéal que l’on souhaite atteindre. Avec ces informations, il est possible de définir les actions idéales pour optimiser les flux de production de l’entreprise.
En somme, l’application de la value stream mapping à un processus de production consiste en l’application de techniques de Lean logistics aux chaînes de production, afin d’identifier les inefficacités pour éliminer les erreurs et les surcoûts.
Comment mettre en œuvre la VSM : 5 étapes à suivre
Voyons les étapes à suivre pour analyser le niveau d’efficacité du processus de fabrication pour une VSM réussie :
1) Identifier le processus à cartographier
Avant de commencer l’analyse, il est nécessaire de définir et de délimiter les étapes à inclure dans l’étude. Pour ce faire, l’entreprise doit avoir déjà désigné le produit ou le service à améliorer.
2) Définir l’objectif et la portée de l’étude
Une fois le processus à améliorer sélectionné, il faut définir les limites de l’étude, en mettant en lumière les étapes actuelles du processus de production et celles qu’il faudrait mettre en place pour parvenir à un état idéal. Par exemple, un objectif pourrait être d’optimiser l’approvisionnement en matières premières d’une chaîne de production. Dans ce cas, l’analyse porterait sur les performances des équipes de travail et de gestion qui interviennent dans cette opération pour détecter les axes d’amélioration.
3) Désigner les personnes chargées de l’étude
La Value Stream Mapping nécessite de faire appel à des experts qui analyseront les étapes du processus de production. À ce stade, il est important de déterminer le rôle de chacun et son niveau de responsabilité en fonction de ses connaissances dans chaque domaine.
4) Procéder à l’analyse
La phase d’exécution est l’une des plus complexes, car l’étude de chaque tâche nécessite, à son tour, trois analyses différentes du processus de production :
- Comment le voyez-vous ?
- Comment est-il en réalité ?
- Comment il devrait être ?
Ces trois analyses permettent au responsable de comparer le processus de production idéal, son état réel et, surtout, la façon dont l’entreprise perçoit ses opérations de fabrication.
5) Préparer le plan d’action
Après avoir réalisé les trois analyses, les participants doivent élaborer un plan d’action pour passer le processus de production de la version 2 (comment il est réellement) à la version 3 (comment il devrait être).
Le plan d’amélioration doit être établi dans le respect des normes de la value stream mapping : les actions doivent être spécifiques, mesurables, atteignables, réalisables et temporellement définies (de l’acronyme anglais SMART).
« Value stream mapping » appliquée à la logistique
Bien que la value stream mapping soit directement liée au Lean manufacturing, cet outil qualité a également un impact sur la logistique d’un produit. Dans quelle mesure ? L’analyse VSM prend en compte les opérations logistiques telles que l’approvisionnement en matières premières, les conditions de stockage et la distribution des commandes.
L’application de cette technique visuelle peut également conduire le responsable logistique à identifier les erreurs et les étapes qui n’apportent pas de valeur ajoutée dans le parcours du produit dans l’entrepôt. La value stream mapping permet de détecter les surcoûts ou les pertes de temps qui peuvent être éliminés avec l’installation de systèmes stockage automatisé, le déploiement d’un système de gestion d’entrepôt ou la mise en œuvre d’une nouvelle méthode de préparation des commandes.
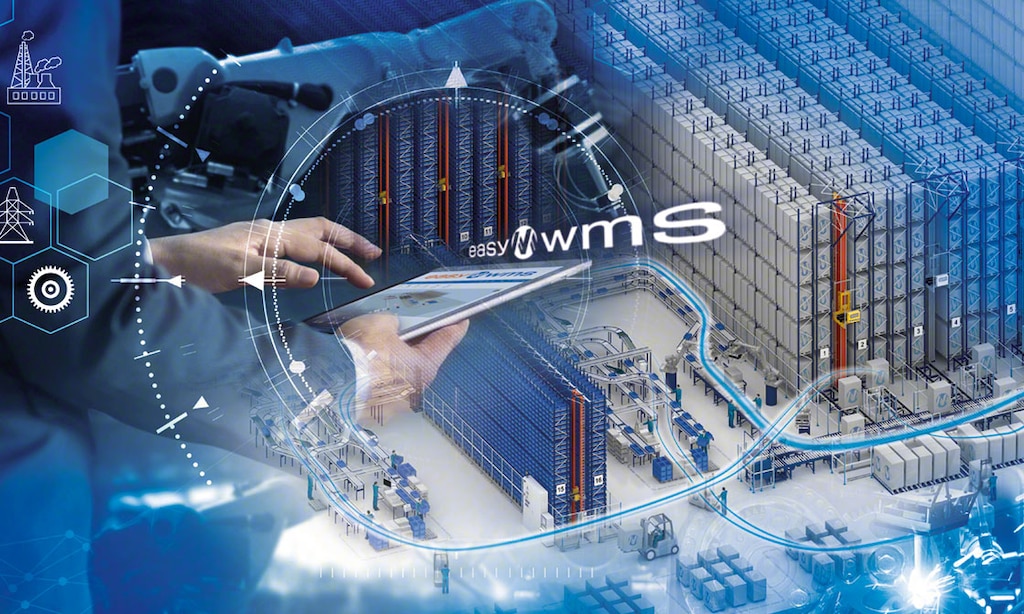
Selon l’étude Value stream mapping in ordering process, publiée par l’Université de Belgrade, la VSM peut servir à détecter les anomalies et améliorer les processus d’entrepôt : « Il est crucial de minimiser les étapes qui n’apportent pas de valeur ajoutée à l’entrepôt et d’augmenter la vitesse et la productivité. Étant donné que de nombreux flux de marchandises et d’informations différents coexistent dans l’entrepôt, ces améliorations peuvent être réalisées à l’aide de la VSM. Selon les chercheurs, l’application de la value stream mapping en logistique améliore les livraisons et optimise les coûts logistiques. « Le but est de livrer des produits de bonne qualité, rapidement et à bas prix. L’une des méthodes les plus fréquemment utilisées pour réduire les délais et les coûts est la VSM ».
Cet outil visuel met en évidence les axes d’amélioration et fournit une analyse de l’état idéal du processus de production. Pour augmenter la productivité, les auteurs proposent plusieurs solutions afin de remédier aux inefficacités dans l’entrepôt tels que : « La création d’un espace libre ou d’une nouvelle salle de conditionnement, la mise en place de nouvelles stratégies d’emplacement ou l’amélioration du système d’information, ainsi que la définition d’indicateurs clés de performance ».
La value stream mapping est également employée dans le secteur du e-commerce. Dans la publication Application of value stream mapping in e-commerce, des étudiants de l’Université de San José (États-Unis) décrivent comment la VSM peut améliorer l’efficacité de la chaîne d’approvisionnement d’un commerce électronique : « Les parties et les activités impliquées, les liens entre elles et le flux d’informations et de produits dans le processus de la chaîne d’approvisionnement sont représentés en créant la VSM. L’ensemble du flux de la chaîne d’approvisionnement est mieux compris et les éventuelles lacunes sont facilement identifiées ».
L’étude, publiée dans la revue universitaire Sustainability, confirme que la méthodologie value stream mapping peut contribuer à réduire les coûts et à améliorer l’efficacité de la gestion de la chaîne d’approvisionnement ainsi que la satisfaction des clients.
VSM, élimination des surcoûts logistiques et de production
La value stream mapping est un outil couramment utilisé pour détecter les axes d’amélioration dans les processus de production. Dans le domaine de la logistique et du stockage, la VSM peut débusquer les inefficacités, par exemple, dans les processus de réception, d’emplacement des produits ou d’expédition des marchandises.
Une planification logistique efficace nécessite une analyse préalable des flux de travail dans l’entrepôt et dans le centre de production afin de maximiser la productivité. Cet outil permet de visualiser les erreurs dans le processus de production qui freinent ses performances. Une fois l’analyse effectuée, Mecalux dispose d’une large gamme de solutions intralogistiques pour accroître la productivité de l’entrepôt et éliminer le risque d’erreur dans les opérations logistiques. N’hésitez pas à nous contacter, un expert vous conseillera sur la meilleure solution pour vos installations.