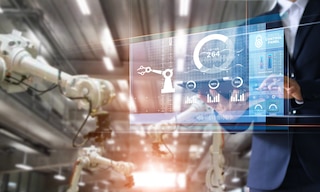
Contrôle de processus dans la chaîne d’approvisionnement
L’optimisation de la chaîne d’approvisionnement passe par des opérations plus précises. Pour cette raison, les responsables logistiques et de production se tournent vers le contrôle de processus pour s’assurer que leurs opérations sont efficaces, sans erreur et conformes aux normes de sécurité en vigueur.
Également connu sous le nom de système de contrôle industriel, ce terme désigne un ensemble d’outils (détecteurs, contrôleurs et régulateurs) utilisés pour surveiller l’état des processus se déroulant dans l’entrepôt ou le centre de production.
Qu’est-ce que le contrôle de processus ?
Le contrôle de processus est une méthode d’analyse couramment employée en logistique et en production. Son objectif principal est d’exécuter et de surveiller un ou plusieurs processus industriels afin d’identifier les anomalies et les erreurs et d’éliminer ainsi les inefficacités.
Grâce à l’utilisation d’équipements et de détecteurs sur les postes de travail, les systèmes de contrôle de processus (en anglais, Process Control Systems) supervisent l’état des opérations et analysent les données produites dans des processus tels que les déplacements de marchandises et la production de masse. Les entreprises installent des détecteurs et autres dispositifs automatiques pour éviter les erreurs dues à la gestion manuelle. L’un des systèmes de contrôle les plus fréquemment utilisés dans les entrepôts est le contrôleur logique programmable (ou PLC, en anglais). Les PLC sont des processeurs qui pilotent les mouvements des systèmes automatisés, en suivant les instructions d’un programme de niveau supérieur (par exemple, un logiciel de gestion d’entrepôt).
Tel que défini dans l’article de recherche Standards-based integration of advanced process control and optimization, publié dans la revue Journal of Industrial Information Integration, le contrôle de processus avancé (dont le sigle anglais est APC) « fait référence aux techniques et technologies mises en œuvre dans les applications de l’industrie de transformation, telles que la pétrochimie, l’énergie, la pharmaceutique ou l’agroalimentaire, entre autres ».
Selon les auteurs, « les systèmes de contrôle de processus peuvent être un système de contrôle distribué (DCS), un contrôleur logique programmable (PLC) et/ou un système de contrôle et de surveillance ». La publication souligne également les avantages de l’APC : « Le large éventail de technologies et de techniques que possèdent les solutions avancées de contrôle des processus permet aux fabricants d’améliorer la capacité de production, de surveiller les paramètres des processus et de fonctionner avec plus de souplesse et de sécurité ».
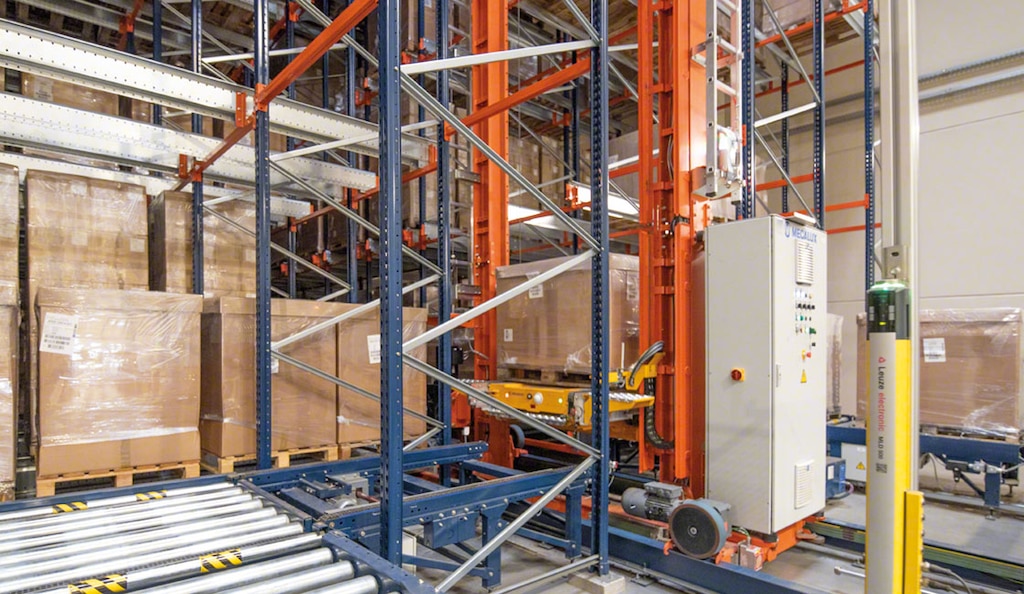
Pourquoi le contrôle des processus est-il si important ?
Le système de contrôle des processus est essentiellement appliqué dans les lignes de fabrication automatisées, où les marchandises sont produites sans interruption. Et de plus en plus d’entreprises ont recours à des méthodes de contrôle de processus pour garantir la qualité optimale de leurs produits.
Dans les smart factories, les entreprises installent des capteurs dans différentes zones pour contrôler les processus et mesurer les conditions de stockage ou de fabrication des produits : acidité, densité, tension, température, poids, taux d’oxygène, parmi de nombreuses autres propriétés qui peuvent être évaluées.
Pour quelle raison ? L’utilisation de détecteurs ou d’autres dispositifs configurés pour surveiller l’état des processus est essentielle pour prévenir les erreurs et renforcer la sécurité dans l’installation. L’utilisation d’un système de contrôle de processus présente de nombreux avantages pour les entreprises :
- Optimisation des dépenses énergétiques.
- Renforcement de la sécurité dans l’installation.
- Respect des normes de qualité.
- Réduction des coûts de fabrication.
Comment fonctionne un système de contrôle de processus ?
Un système de contrôle de processus est activé lorsque des outils de mesure sont installés dans le cadre d’un processus de production. L’objectif de ce système est de collecter des informations sur l’état du processus de production et de prendre des mesures lorsque les niveaux dépassent les limites prédéfinies par le responsable de la production.
Dans un système de contrôle industriel, on parle de point de consigne le niveau exact marqué par un paramètre pour indiquer que l’opération est correctement exécutée. En outre, des variations prédéterminées doivent être acceptées pour chacune des propriétés à analyser, ce qui facilite la mesure et le contrôle du processus.
Cette méthode de contrôle du processus de production comprend trois types de composants pour chacune des variables à surveiller :
- Un dispositif de mesure : il suit en permanence une propriété spécifique du processus de production (par exemple, la température, le taux d’oxygène ou le taux d’acidité) pour s’assurer qu’elle se situe dans les valeurs prédéterminées.
- Contrôleur : ce composant compare les valeurs enregistrées à intervalles réguliers par le dispositif de mesure avec les valeurs prédéfinies. Si elles ne concordent pas, le contrôleur déclenche une action préconfigurée pour que l’état de la production revienne aux niveaux définis. Par exemple, lorsque le débit d’un liquide descend en dessous du volume défini, le système commande l’ouverture des vannes ou de la pompe d’injection afin d’augmenter la quantité de produit ou de matière première.
- Régulateur : cet élément dépend du contrôleur et s’adapte à chaque processus de production. Le régulateur coordonne l’exécution du processus, il suit les instructions du contrôleur lorsque le processus de production ne respecte pas les normes indiquées par le responsable ou le fabricant.
Exemple de système de contrôle de processus
Dans un environnement industriel, un système de contrôle de processus a pour rôle de surveiller et d’ajuster automatiquement un processus de production afin de maintenir les normes de qualité et de productivité. Dans un contexte de production industrielle, un exemple de contrôle de processus consisterait à établir des mécanismes pour maintenir une température constante de -15 °C sur les lignes de production afin de conserver un produit spécifique dans les meilleures conditions.
Pour s’assurer que l’air reste à cette température, un système de contrôle comprenant un capteur de température et un contrôleur est mis en œuvre. Le capteur de température envoie régulièrement des informations au contrôleur indiquant la température de l’installation. Le contrôleur, dont le rôle est de vérifier que l’environnement est à une certaine température (avec quelques variations acceptées), envoie des instructions au régulateur (qui pourrait être un système de climatisation industrielle) pour ajuster la température lorsqu’elle monte ou descend trop.
Bien que cet exemple montre l’efficacité d’un contrôleur de processus sur une ligne de production simple, les systèmes de contrôle de processus sont généralement installés dans des environnements plus complexes. Par exemple, une ligne de fabrication de produits chimiques avec une formulation composée de plusieurs liquides pour créer un seul produit. Dans ce cas, le système de contrôle automatise la gestion des vannes, en utilisant des capteurs qui indiquent la quantité de produit disponible. Le contrôleur calcule la quantité des autres produits nécessaires en fonction de la mesure du capteur. Il indique ensuite aux vannes les quantités de matières nécessaires pour que le processus de production se poursuive comme prévu.
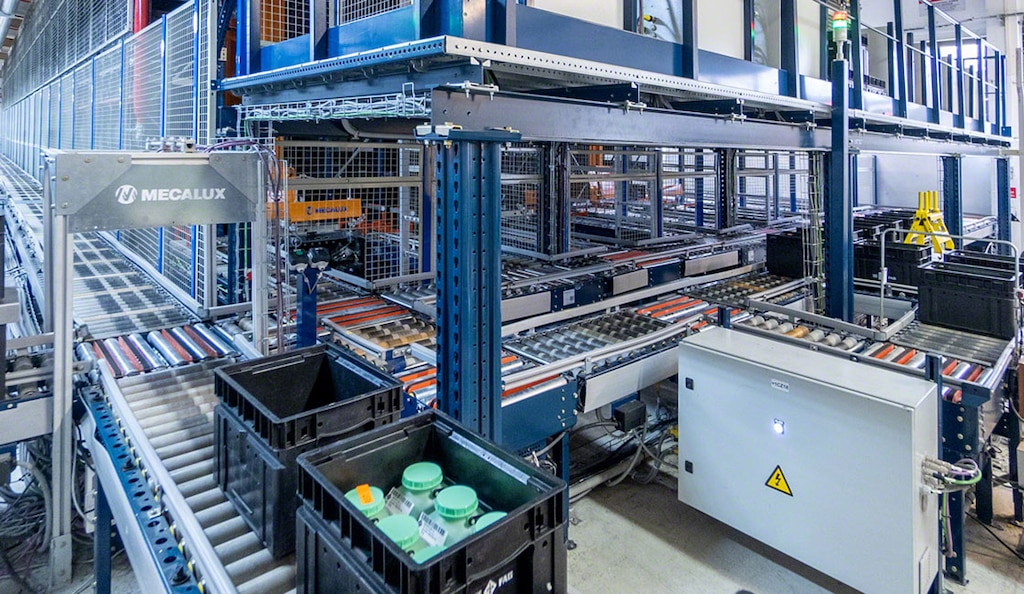
Le contrôle de processus pour une gestion efficace
De plus en plus d’entreprises emploient des contrôleurs automatiques pour exécuter et surveiller les performances de leurs processus. Pourquoi ? Un système de contrôle de processus automatisé élimine les erreurs dans la gestion des lignes de production.
L’utilisation d’outils tels que des détecteurs ou des processeurs permet non seulement de maintenir des standards de qualité dans la fabrication, mais aussi de réduire les coûts de production pour l’entreprise, ce qui est essentiel dans la logistique et la production 4.0.