L’une des questions les plus importantes à se poser lors de l’élaboration du cahier des charges pour la construction d’un nouvel entrepôt est de savoir quelle solution est la plus adaptée pour maximiser la capacité de stockage. Toutefois, ce critère ne doit pas être le seul à être pris en compte pour la conception d’un entrepôt. D’autres facteurs existent et son tout aussi essentiels, tels que la vitesse de manutention des palettes en fonction des configurations.
D’autre part, la capacité physique d’un entrepôt (le nombre maximum de palettes pouvant être stockées) n’est pas toujours équivalente à sa capacité effective, autrement dit, la capacité obtenue lors d’un cycle de travail normal, selon le nombre maximal et minimal de références et l’espace que l’on doit leur réserver.
C’est pourquoi, la méthode d’affectation des emplacements est primordiale, car toutes ne sont pas bénéfiques de la même manière :
- La méthode d’emplacement dite « fixe » exige de réserver un certain nombre d’alvéoles pour chaque référence, sauf pour celles qui peuvent partager des emplacements. Lorsque la marchandise entre dans l’entrepôt, toutes les alvéoles disponibles sont remplies mais, au fur et à mesure de la préparation de commandes, ces alvéoles se vident. Comme elles sont réservées pour une référence spécifique, elles ne peuvent donc pas servir pour le stockage d’autres références, et la capacité effective sera différente de la capacité physique. Plus précisément, la capacité effective représente celle du stock minimal plus la moitié de la différence entre ce stock minimal et le nombre d’alvéoles assigné à cette référence. La capacité effective de la stratégie d’assignation des emplacements fixe se situe donc entre 55 et 65 % de la capacité réelle.
- La méthode d’emplacement dite « chaotique » ou aléatoire, exige l’installation d’un logiciel de gestion d’entrepôt (WMS). Celui se charge d’attribuer de manière aléatoire le premier emplacement vide à chaque palette réceptionnée et d’enregistrer puis d’informer l’opérateur de l’emplacement de cette dernière au moment où il en aura besoin. Avec cette stratégie, il n’y a quasiment plus d’alvéoles vides et la capacité effective représente alors 80 à 92 % de la capacité physique.
Si les différences entre les deux méthodes d’affectation des emplacements ne sont pas correctement évaluées, la solution de stockage choisie risque de ne pas être adaptée aux besoins. Toutes les installations peuvent fonctionner selon les deux stratégies, cependant les systèmes de stockage par accumulation, par exemple, ne sont pas flexibles et il peut arriver, bien qu’ils aient une plus grande capacité physique que d’autres, que leur capacité effective soit moindre.
Cas pratiques
Afin d’illustrer les différences pouvant apparaître selon la méthode d’affectation choisie, prenons l’exemple d’un entrepôt aux dimensions déterminées traitant un type de charge spécifique, présenté ci-dessous. Dans ce cas, différentes solutions de stockage sont possibles (configurations et engins de manutention), avec des résultats propres à chaque installation.
La capacité de stockage est calculée en fonction de la surface et, est définie à partir d’un niveau de stockage, sachant que la hauteur de l’installation est une variable qui dépend du bâtiment et de la capacité de levage des engins de manutention. Pour faciliter la comparaison entre les différents systèmes, l’espace nécessaire aux zones de réception et d’expédition de la marchandise n’a pas été pris en compte. L’unité de charge choisie est la palette Europe aux dimensions de 1 200 x 800 mm, qui permet de stocker dans le rayonnage à palettes conventionnel jusqu’à trois palettes par alvéole de 2 700 mm de large.
La capacité (et donc le taux d’occupation) est spécifiée par niveau, autrement dit, par la surface et non pas par le volume total de l’installation.
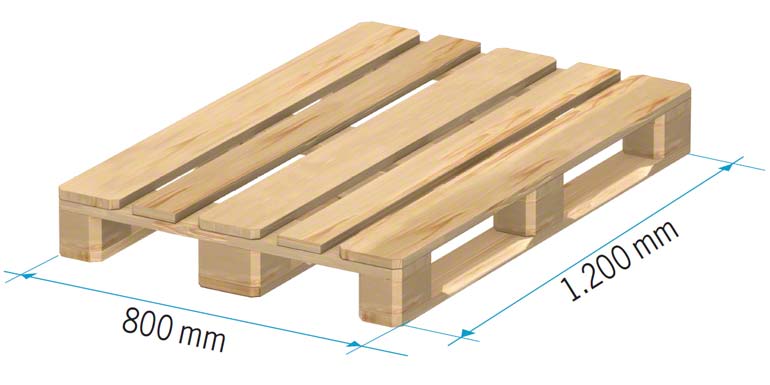
Unité de charge : palette de 1 200 x 800 mm
Exemple 1. Rayonnage à palettes avec chariot élévateur à contrepoids |
Système : Rayonnage à palettes Allée : 3 500 mm, avec un minimum de 3 600 mm entre les rayonnages Manutention : Chariot élévateur à contrepoids Capacité de stockage : 594 palettes par niveau |
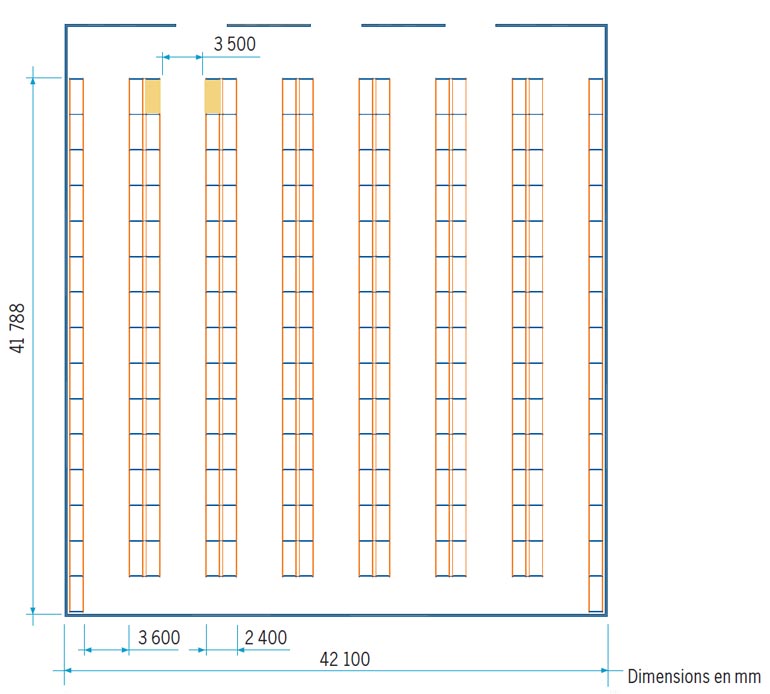
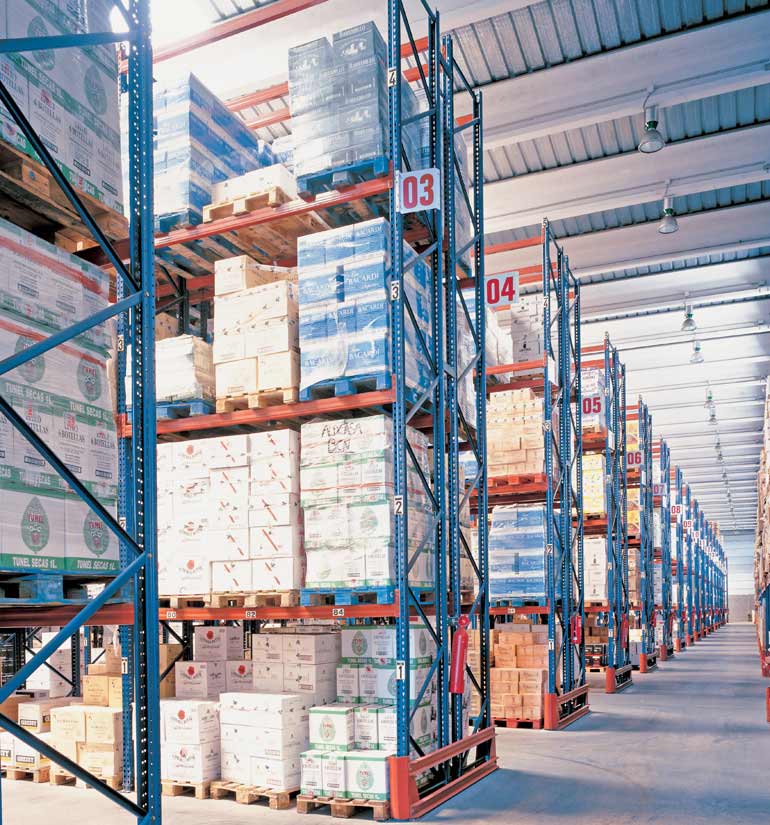
Entrepôt d'une entreprise de distribution
Exemple 2. Rayonnage à palettes avec chariot à mât rétractable ou transstockeur |
Système : Rayonnage à palettes Manutention : Chariot élévateur à mât rétractable Allée : 2 750 mm, avec un minimum de 2 850 mm entre les rayonnages Capacité de stockage : 678 palettes par niveau |
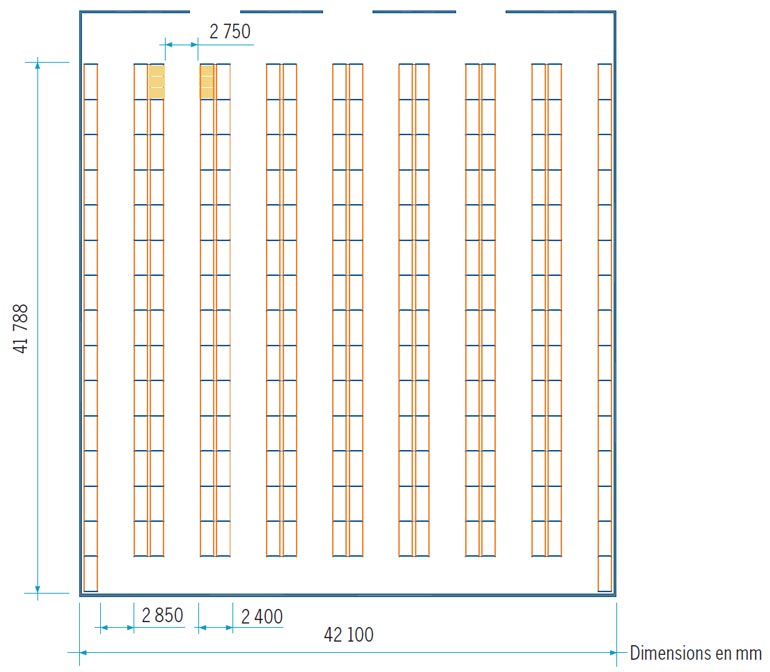
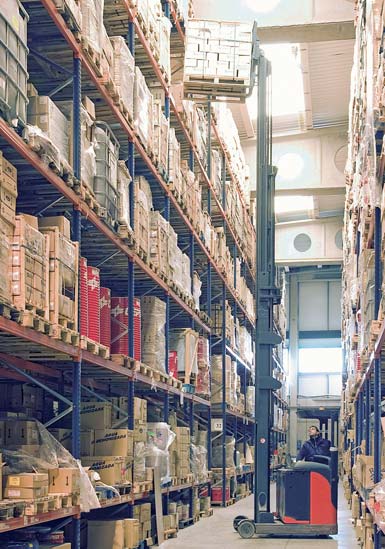
Entrepôt d'un prestataire logistique
Exemple 3. Rayonnage à palettes avec chariot tridirectionnel ou transstockeur |
Système : Rayonnage à palettes Manutention : Chariot tridirectionnel ou transstockeur Allée : 1 700 mm, avec un minimum de 1 800 mm entre les rayonnages Capacité de stockage : 840 palettes par niveau Remarque : Pour un transstockeur, la largeur de l’allée minimum est de 1 500 mm, la largeur totale de l’installation peut donc être de 40 000 mm au lieu 42 100 mm pour obtenir le même résultat. |
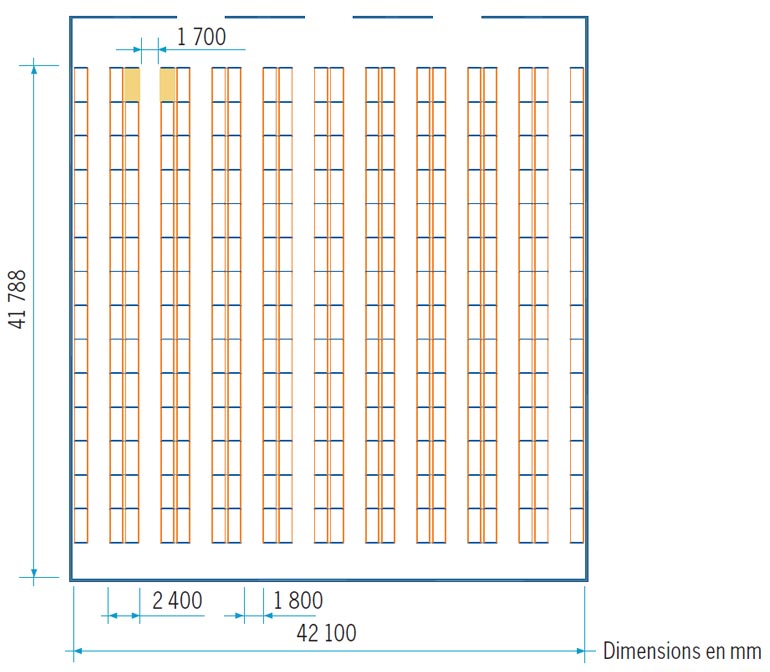

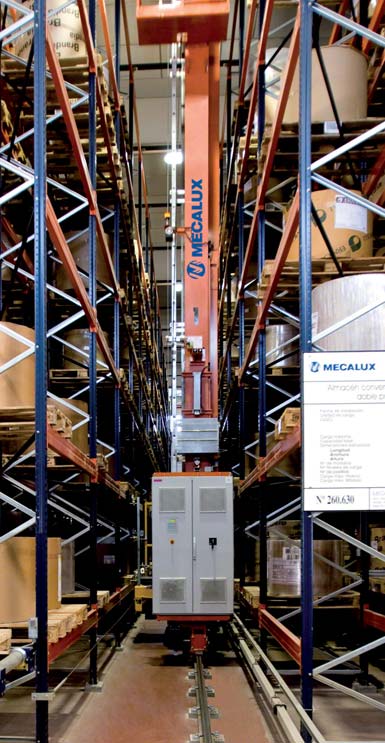
Magasin automatique pour le stockage de bobines de papier
Exemple 4. Rayonnage à palettes à double profondeur avec transstockeur |
Système : Rayonnage à palettes à double profondeur Manutention : Transstockeur Allée : 1 500 mm avec un minimum de 1 600 mm entre les rayonnages Capacité de stockage : 1v008 palettes par niveau Remarque : Comme dans l’exemple 3, la largeur totale du magasin peut être de 40 000 mm au lieu de 42 000 mm. |
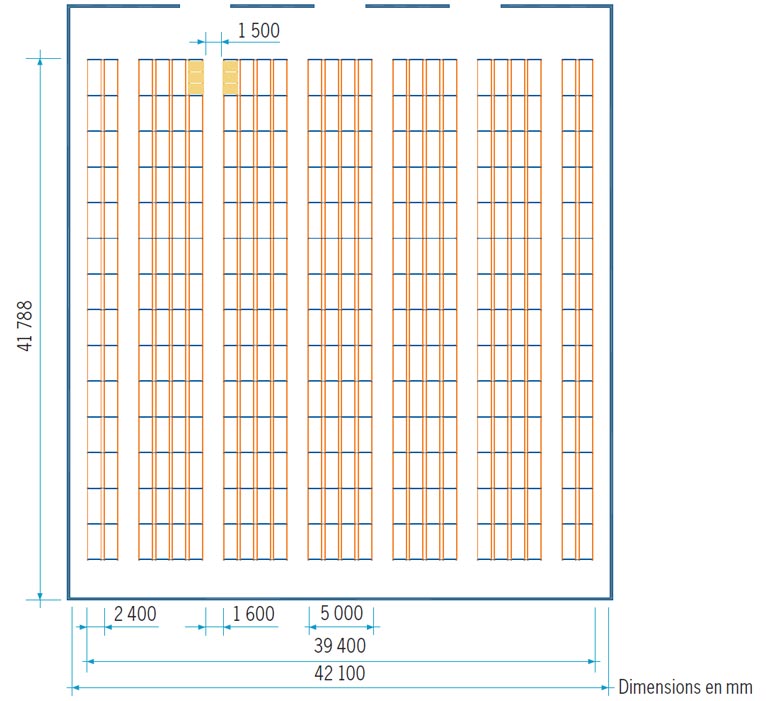
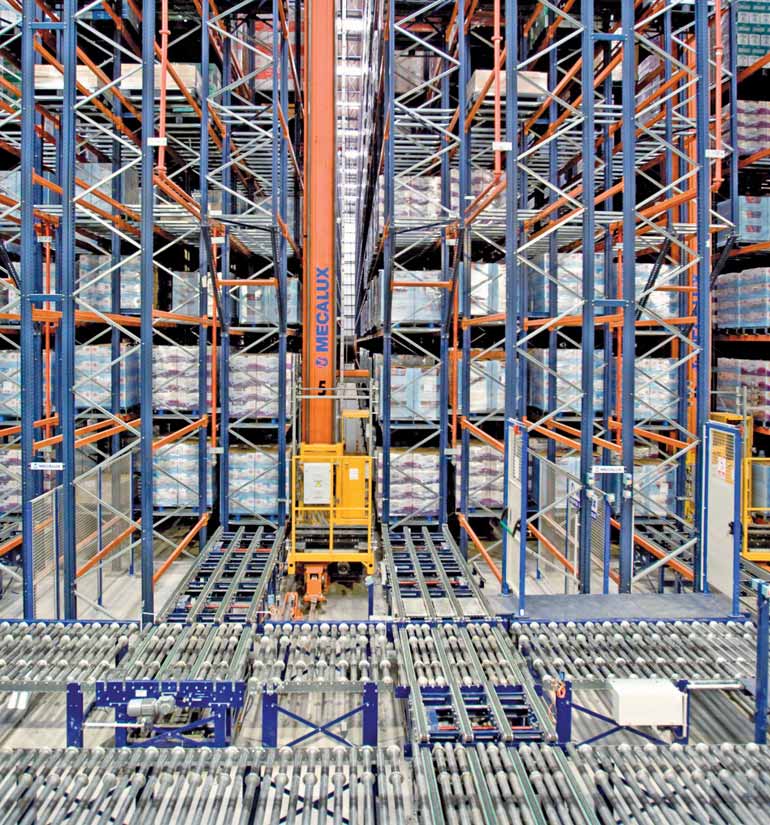
Rayonnages pour le stockage de produits de grande consommation
Exemple 5. Rayonnage à palettes sur bases mobiles |
Système : Rayonnage à palettes sur bases mobiles Manutention : Chariot élévateur Allée : Deux allées de 3 750 mm chacune. Dans ces allées, deux chariots peuvent se croisent (si les marges sont respectées). Capacité de stockage : 1 144 palettes par niveau |
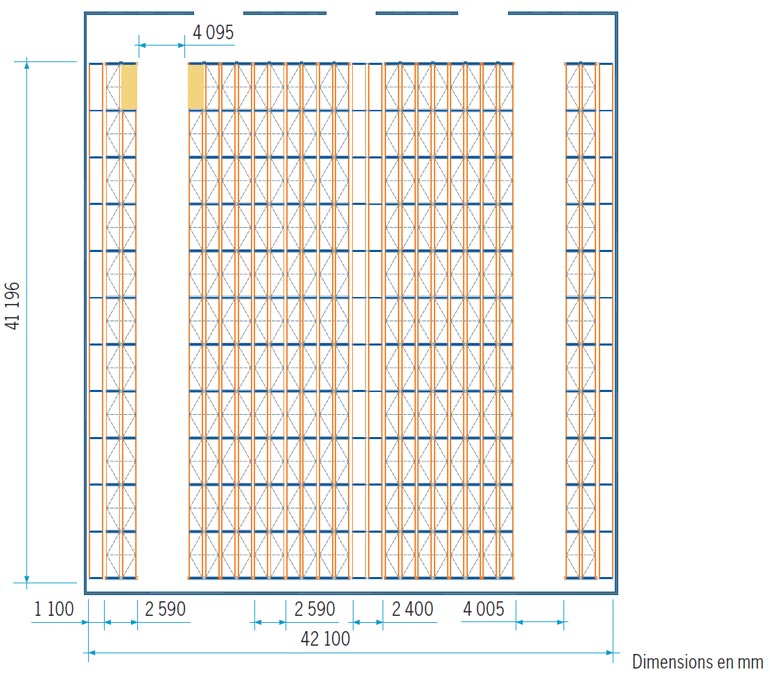
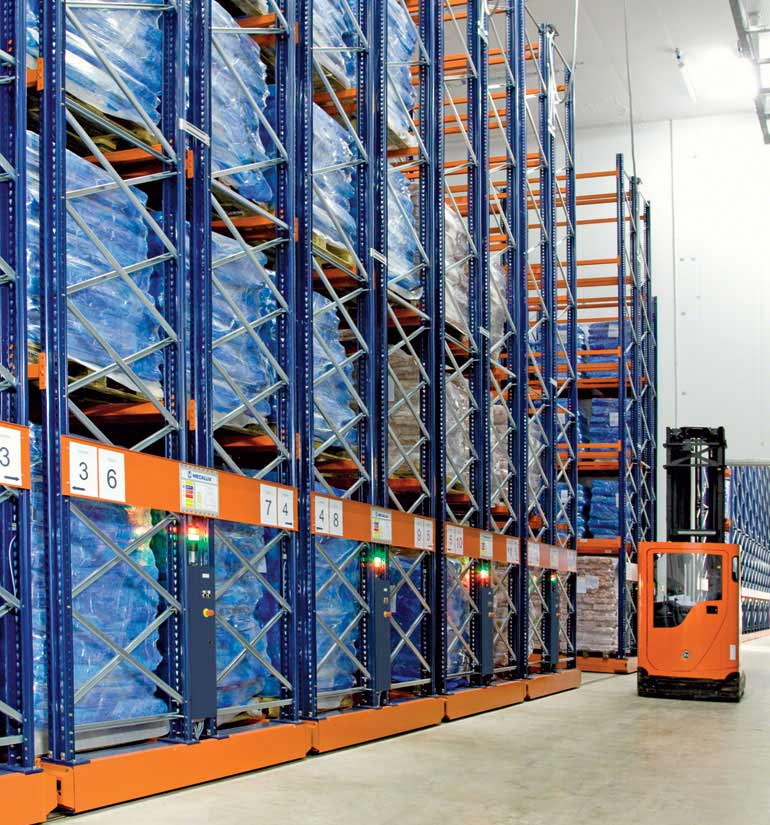
Rayonnages sur bases mobiles pour le stockage de viande congelée
Exemple 6. Rayonnage à palette par accumulation |
Système : Rayonnage à palettes par accumulation Manutention : Chariot élévateur Allée : 3 500 mm, avec la possibilité que deux chariots se croisent Capacité de stockage : 960 palettes par niveau |
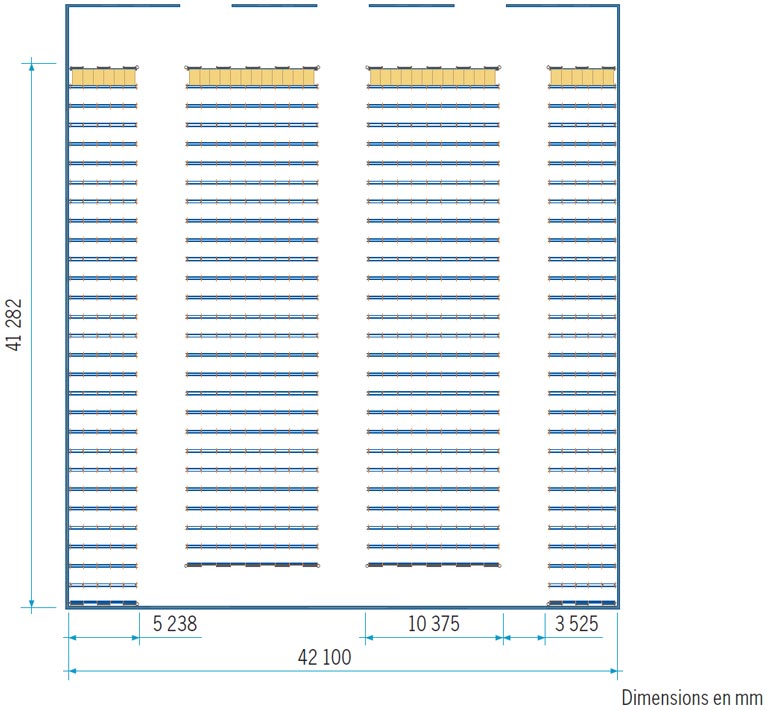
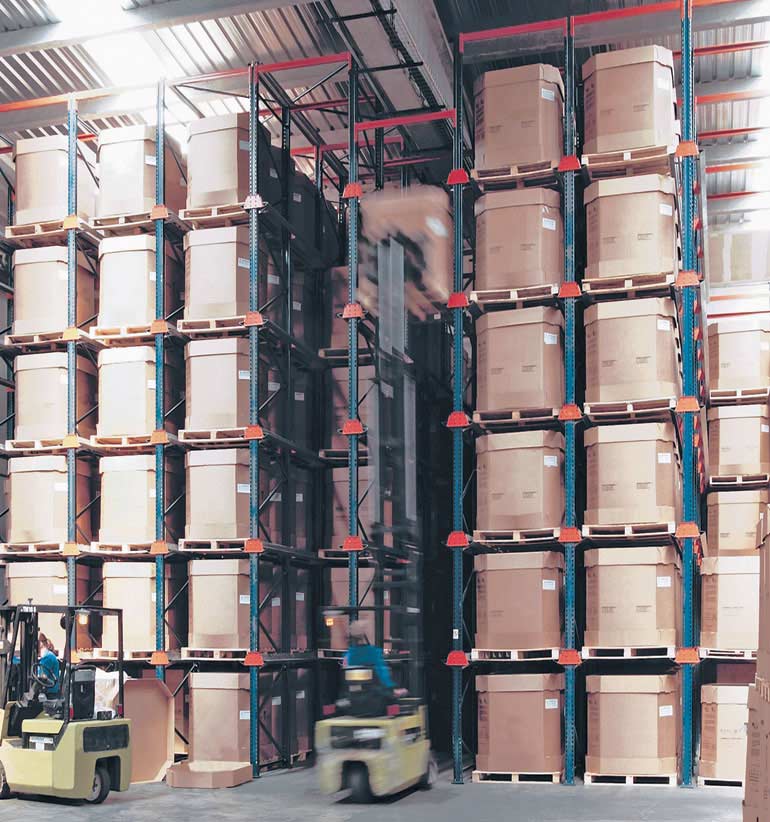
Rayonnages par accumulation
Exemple 7. Système Push-back à chariots |
Système : Push-back à chariots Manutention : Chariot élévateur Allée : 3 500 mm, au minimum Capacité de stockage : 848 palettes par niveau |
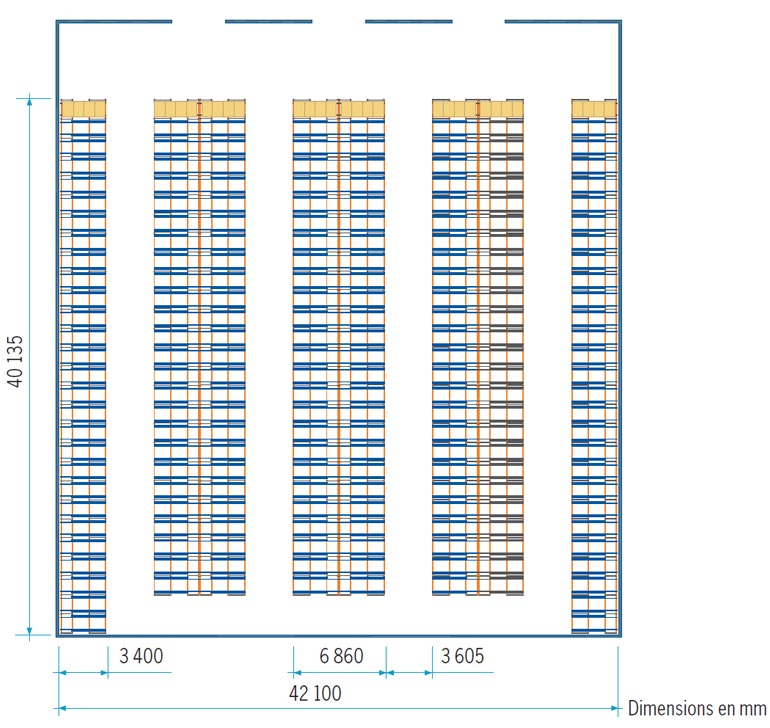
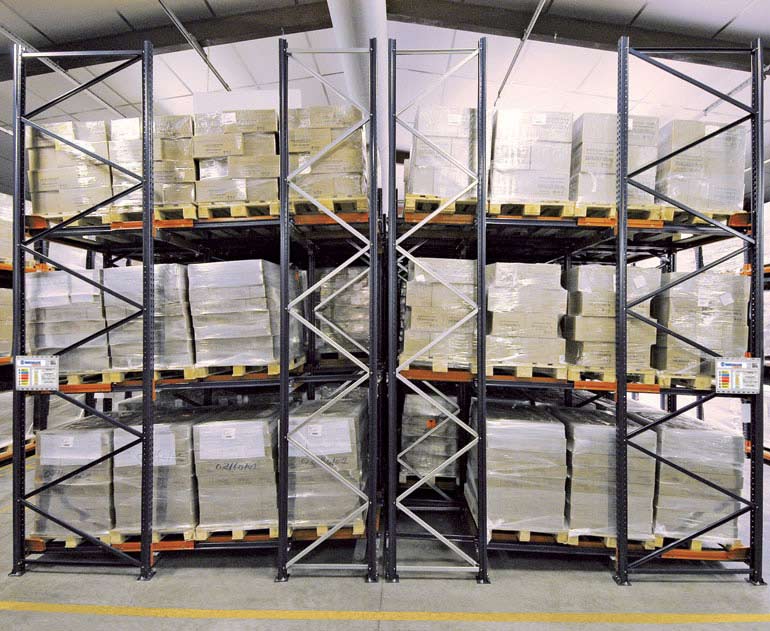
Exemple 8. Système Push-back à rouleaux |
Système : Push-back à rouleaux Manutention : Chariot élévateur Allée : 3 400 mm, au minimum Capacité de stockage : 893 palettes par niveau |
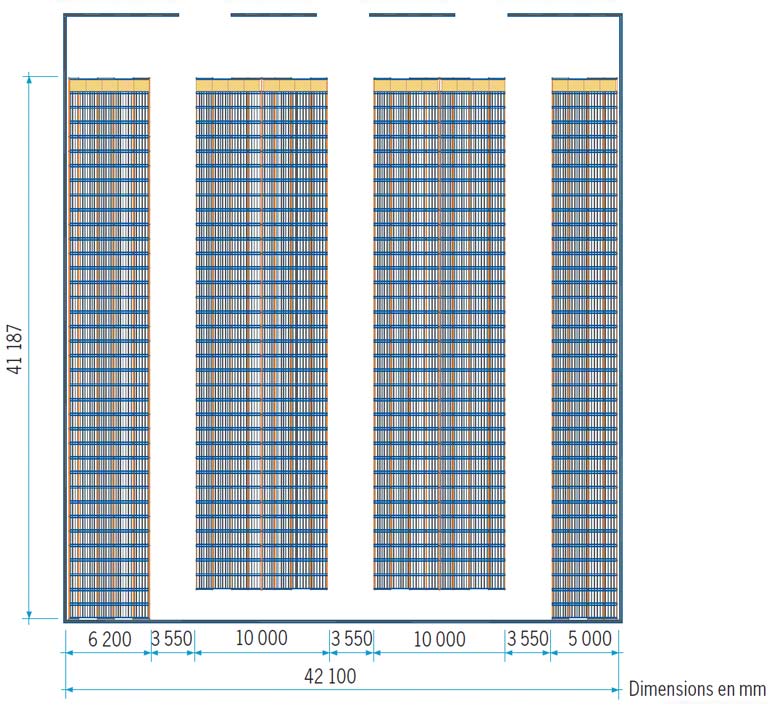
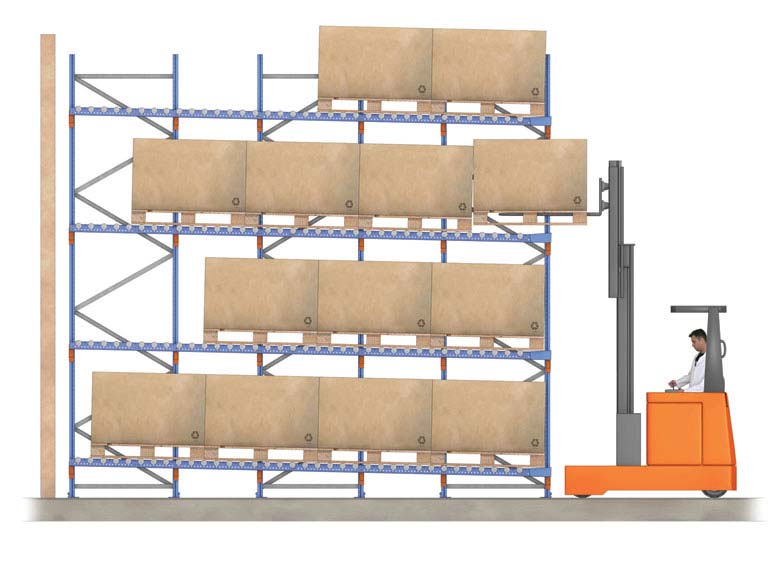
Exemple 9. Rayonnage à palettes avec système Pallet Shuttle |
Système : Rayonnage à palettes avec système Pallet Shuttle Manutention : Chariot élévateur Allée : 3 500 mm, au minimum (largeur pour que deux chariots se croisent) Capacité de stockage : 1 080 palettes par niveau |
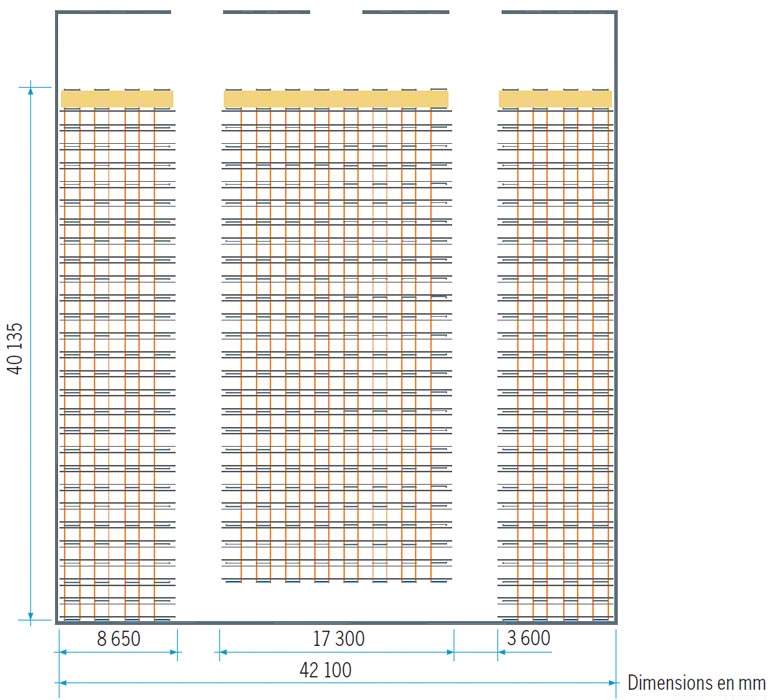
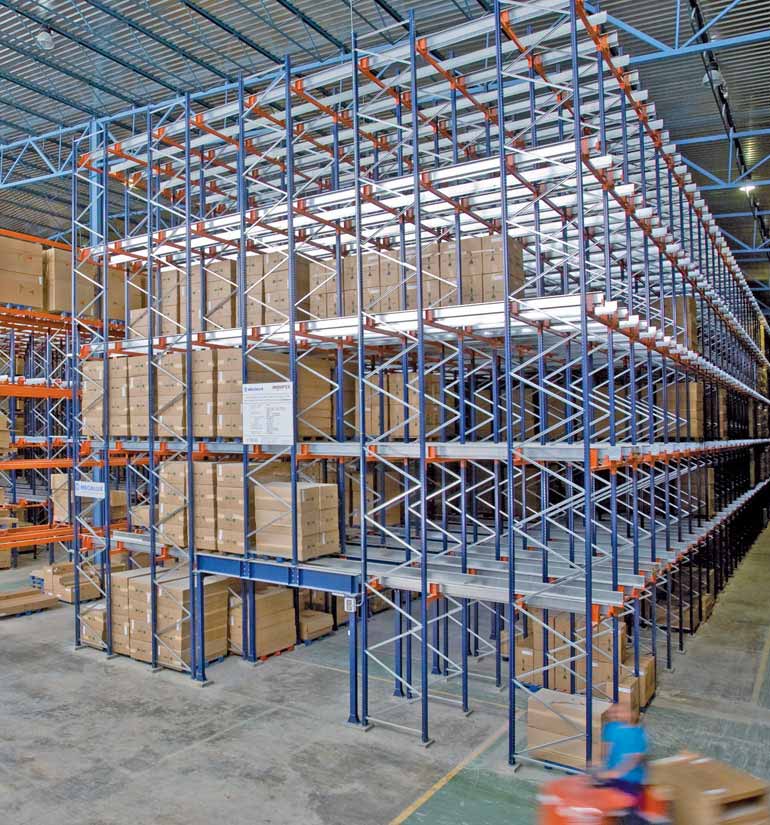
Rayonnages Push Back pour le stockage de mobilier en kit
Exemple 10. Rayonnage à palettes dynamique |
Système : Rayonnage à palettes dynamique Manutention : Chariot élévateur Allée : 3 400 mm au minimum Capacité de stockage : 910 palettes par niveau |
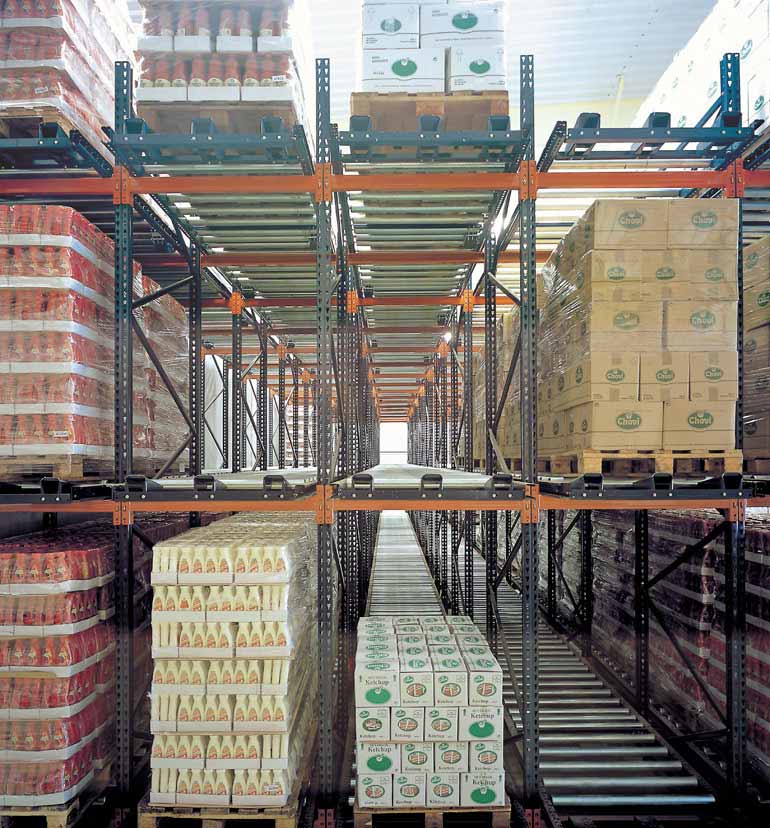
Rayonnages dynamiques d'un fabricant de jus
Tableau récapitulatif des différences de capacité physique |
|||
Système de stockage | Palettes par niveau | Superficie pour les palettes | Taux d'occupation de la surface totale |
Rayonnage à palettes avec chariot élévateur à contrepoids | 594 | 570 m2 | 32,2 % |
Rayonnages à palettes avec chariot à mât rétractable | 678 | 651 m2 | 39,2 % |
Rayonnages à palettes avec chariot tridirectionnel ou transstockeur | 840 | 806 m2 | 45,7 % |
Rayonnages à palettes à double profondeur desservis par un transstockeur | 1.008 | 968 m2 | 54,9% |
Rayonnages à palettes avec bases mobiles | 1.144 | 1.098 m2 | 62,2 % |
Rayonnages à palettes par accumulation avec chariot à mât rétractable | 960 | 922 m2 | 53,8 % |
Rayonnages à palettes Push-back à chariots | 848 | 814 m2 | 46,0 % |
Rayonnages à palettes Push-back à rouleaux | 893 | 857 m2 | 48,0 % |
Rayonnages à palettes avec système Pallet Shuttle | 1.080 | 1.037 m2 | 58,8 % |
Rayonnage à palettes dynamique | 910 | 874 m2 | 47,6 % |
La capacité de stockage n’est pas linéaire car d’autres facteurs jouent, tels que la hauteur de l’entrepôt et celle des palettes. Un autre facteur déterminant est le système de stockage choisi : les rayonnages dynamiques, par définition sont inclinés et impliquent une perte de hauteur ; dans les installations à double profondeur avec transstockeur, par exemple, une plus grande séparation entre les niveaux est nécessaire ; dans certains cas, l’utilisation de profils de support est nécessaire et ainsi qu’une certaine hauteur pour le premier niveau.
Ce tableau est présenté à titre indicatif et se réfère à la capacité physique, non pas à la capacité effective.