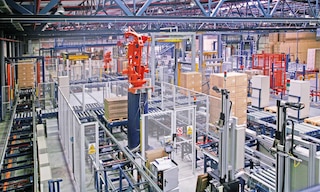
25 consignes de sécurité pour votre entrepôt
Pour protéger l’intégrité physique des opérateurs, assurer la préservation des marchandises stockées et garantir le bon fonctionnement des systèmes de stockage et de transport, il convient de respecter quelques consignes de sécurité dans l’entrepôt.
En gardant ces recommandations à l’esprit, non seulement vous favorisez un environnement sûr, mais aussi vous augmentez la productivité de votre entrepôt grâce à des conditions de fonctionnement optimales des différentes activités.
En logistique, les principaux risques sont les suivants :
- Chute de marchandises en raison d’un mauvais empilage de la charge stockée, de chocs contre la structure des rayonnages, etc.
- Accidents causés par des chutes, des glissades, des coups, des coupures, des happements ou des collisions résultant de la circulation des opérateurs dans l’entrepôt ou de l’utilisation de machines, d’outils ou d’engins de manutention.
- Incendies provoqués par la combustion incontrôlée de substances inflammables, l’accumulation de vapeurs ou les tremblements de terre, des électrocutions ou des brûlures causées par une installation électrique défaillante, etc.
Dans cet article, nous passons en revue 25 consignes de sécurité à appliquer dans l’entrepôt et expliquons comment les mettre en place.
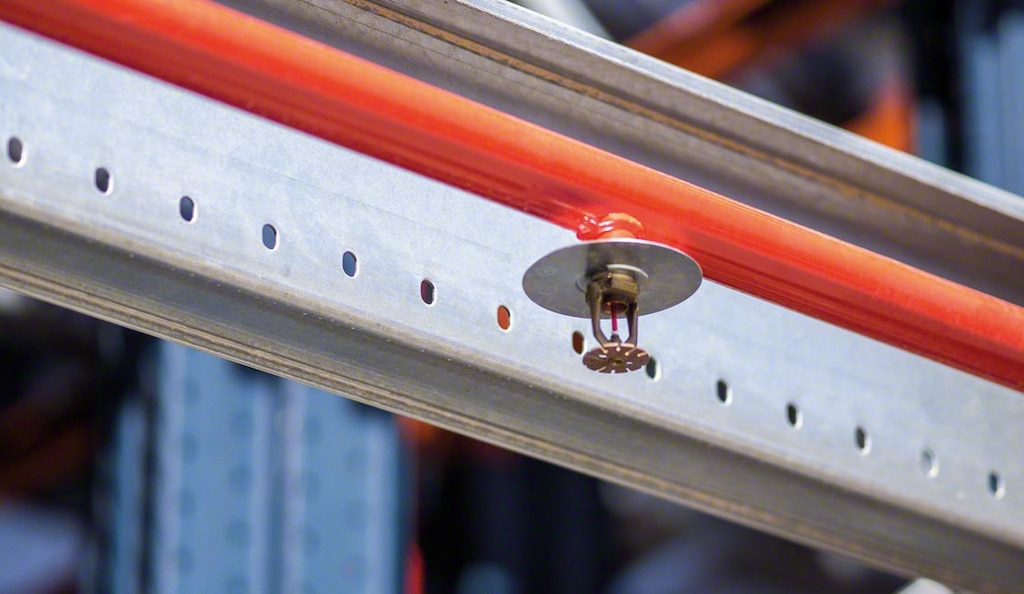
Les consignes pour un environnement sûr dans l’entrepôt
Nous proposons premièrement quelques consignes permettant de réduire considérablement le risque de chute ou d’effondrement de marchandises des rayonnages :
- Port d’EPI adaptés. L’utilisation d’EPI dans l’entrepôt protège l’opérateur contre les risques pouvant menacer sa santé au travail. Les équipements de protection individuelle les plus courants sont les casques, les gants, les lunettes, les chaussures, les casques anti-bruit et les bouchons d’oreilles.
- Respect des inspections techniques régulières des systèmes de stockage. La norme UNE-EN 15635 oblige le propriétaire de l’entrepôt à effectuer annuellement une Inspection Technique des Rayonnages (ITR) assurée par des techniciens qualifiés pour évaluer l’état des éléments de l’installation.
- Respect des capacités et des dimensions maximales des rayonnages. Chaque système de stockage est conçu pour supporter un certain poids et certaines dimensions des marchandises.
- Non-modification sans consulter le fournisseur. Les rayonnages ont été configurés par une équipe de professionnels ayant pris en compte des particularités techniques pour garantir la sécurité. Pour cette raison, il est fortement déconseillé d’apporter des modifications sans consulter le fournisseur au préalable.
- Lecture et prise en compte des informations affichées sur la plaque signalétique. Fournie par le fournisseur, elle contient les spécifications techniques de l’installation. La plaque doit être clairement visible et inspectée périodiquement pour vérifier que les informations correspondent bien à l’installation réelle.
- Contrôler l'état des palettes. Cette procédure peut être automatisée au moyen d’un poste d’inspection d’entrée (PIE), qui valide l’état des marchandises et garantit ainsi leur circulation dans l’installation sans risque d’accident.
- Chargement adéquat des palettes. Pour éviter l’effondrements des marchandises et assurer la stabilité de l’ensemble, il est fondamental de charger correctement les palettes.
- Installation d’éléments de protections des rayonnages. Il existe différentes protections pour les rayonnages conçues pour absorber différents types d’impacts et pour préserver l’intégrité de la structure qui supporte les charges. Les protections latérales préservent les parties inférieures des côtés des rayonnages, tandis que les protections pour montants et échelles sont ancrées au sol et couvrent le montant du rayonnage.
- Mise en place de grillages antichute. Installés à l’arrière des rayonnages, partie coïncidant avec la zone de travail ou de transit, ils évitent la chute accidentelle des marchandises. Il est également nécessaire de les installer au niveau de la partie inférieure des passerelles de sécurité.
Par ailleurs, il est aussi essentiel de suivre certaines recommandations pour minimiser les risques liés à la circulation de personnes dans l’entrepôt ou à l’utilisation de différents équipements et engins :
- Éclairez correctement l'entrepôt. Avec des conditions d'éclairage optimales dans un entrepôt, nous évitons au maximum que des accidents se produisent. La visibilité de toute la surface de celui-ci est fondamentale et essentielle afin de garantir des environnements de travail optimaux pour les employés et de préserver les rayonnages.
- Utilisation de grillages / cloisons de sécurité. Placés sur le périmètre d’un entrepôt automatisé ou dans la zone de fonctionnement d’un engin robotique, ils protègent les opérateurs contre la chute éventuelle de matériaux détachés. Les cloisons industrielles grillagées, quant à elles, créent un espace protégé à accès restreint.
- Installation de miroirs aux croisements et dans les allées. Ils augmentent la visibilité et éliminent les angles morts aux endroits où circulent les chariots élévateurs et autres engins de manutention.
- Aménagement de passerelles de sécurité. Elles traversent les allées de stockage des rayonnages et peuvent servir d’issues de secours. Elles sont indispensables lorsque les allées de stockage sont très longues.
- Bonne signalisation de l’entrepôt. L’objectif étant d’informer les opérateurs sur les risques éventuels en identifiant clairement les zones à accès restreint, les zones de travail des chariots élévateurs ou les espaces de préparation et de conditionnement des commandes. La signalisation de l’entrepôt est effectuée au moyen de panneaux colorés et de formes géométriques.
- Utilisation des engins de manutention avec précaution. L’opérateur doit être très prudent lors de la conduite des chariots élévateurs dans l’entrepôt, afin d’éviter de heurter d’autres opérateurs, des rayonnages ou d’autres engins de manutention.
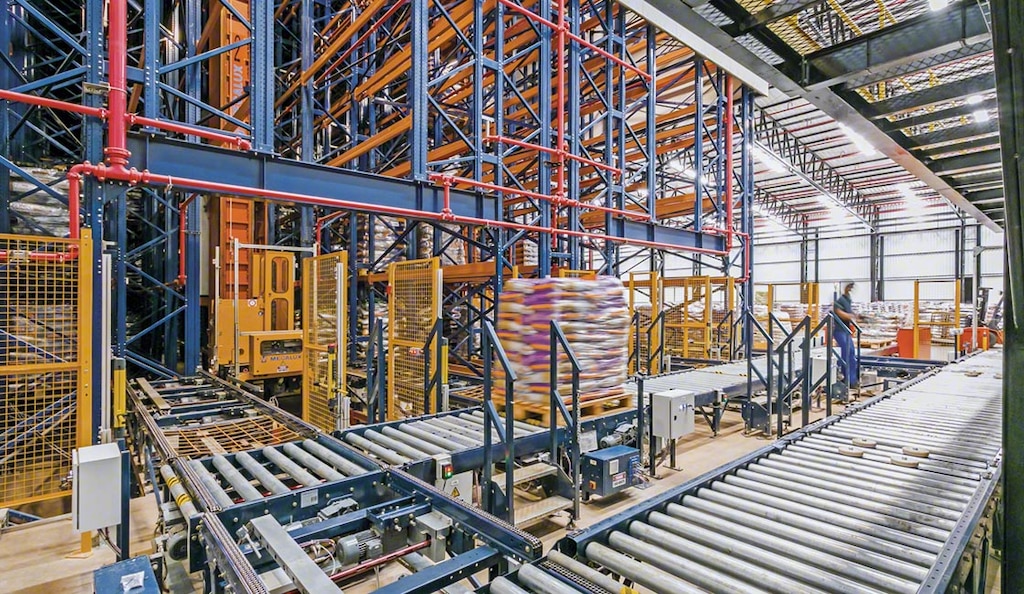
De même, il ne faut pas négliger d’autres consignes de sécurité dans l’entrepôt, plus générales, mais tout aussi pertinentes, de la maintenance préventive des machines et des équipements à la formation du personnel et à la bonne tenue des installations :
- Installation de systèmes anti-incendie. Il existe différents systèmes de lutte contre l’incendie indispensables dans tout entrepôt : manuels (extincteurs ou lances d’incendie), des systèmes d’alarme et de détection automatique (détecteurs de fumée), des systèmes de contrôle out d’extinction automatique d’incendies (les sprinklers automatiques) ou des systèmes de contrôle de la température et d’évacuation des fumées.
- Maintenance périodique des engins. La mise en œuvre d’un plan de maintenance préventive industrielle, à savoir un ensemble d’actions destinées à réparer l’usure due à l’utilisation d’équipements et de systèmes de stockage dans le but de prévenir les pannes, est essentielle pour augmenter les performances des machines et améliorer la sécurité de l’installation.
- Ordre et propreté permanents des installations. Un entrepôt ordonné et propre réduit les risques d’accidents et favorise la productivité. Le nettoyage industriel de l’entrepôt est donc important pour maintenir l’ordre dans les espaces de travail et de manutention des marchandises, ainsi que pour garantir la propreté des planchers, des plafonds, des murs, des rayonnages, des canalisations, de l’éclairage et des machines.
- Température de travail adéquate. L’automatisation des entrepôts frigorifiques permet de protéger les opérateurs d’une exposition prolongée au froid.
- Formation adéquate du personnel. Les opérateurs doivent être correctement formés à la bonne utilisation des équipements. En matière de logiciels, par exemple, Mecalux offre un service de formation permettant aux opérateurs d’utiliser correctement Easy WMS et ses outils de conception et de paramétrage, ainsi que d’autres produits Mecalux.
Enfin, il est recommandé d’automatiser différents processus et opérations afin d’augmenter considérablement le niveau de sécurité d’une grande partie des tâches d’entrepôt :
- Utilisation de systèmes de transport automatiques. Le risque d’accidents augmente lorsque le nombre d’engins de manutention conduits par des opérateurs est plus important. Pour réduire les déplacements, des systèmes de transport automatiques tels que des convoyeurs, des AGV ou des robots mobiles peuvent être mis en œuvre pour transférer les marchandises d’un endroit de l’installation à un autre.
- Mise en place de postes de travail ergonomiques. Les stations de picking doivent assurer une préparation des commandes efficace et en toute sécurité, mais aussi rapide et confortable pour l’opérateur. C’est pourquoi l’utilisation de bras hydrauliques pour manipuler les charges lourdes ou de tables réglables en hauteur est fréquente pour un picking ergonomique.
- Utilisation de capteurs de sécurité. Ils ont pour but de détecter tout élément gênant le déplacement d’un engin automatique afin d’arrêter le système et éviter les accidents. L’un des dispositifs les plus utiles est le capteur installé dans de multiples systèmes automatiques tels que les différents types de transstockeurs ou les rayonnages à palettes mobiles.
- Automatisation des itinéraires de picking. La mise en œuvre d’un logiciel de gestion d’entrepôt permet d’optimiser les itinéraires des opérateurs lors de la préparation des commandes. De cette façon, le nombre de personnes dans l’entrepôt est moins important et le risque d’accident est donc réduit.
- Automatisation du flux de marchandises à dans les rayonnages. L’utilisation de systèmes de stockage automatisés, tels que les transstockeurs pour palettes, les miniload ou le système Pallet Shuttle, limite également considérablement la circulation des chariots élévateurs et des transpalettes dans l’entrepôt.
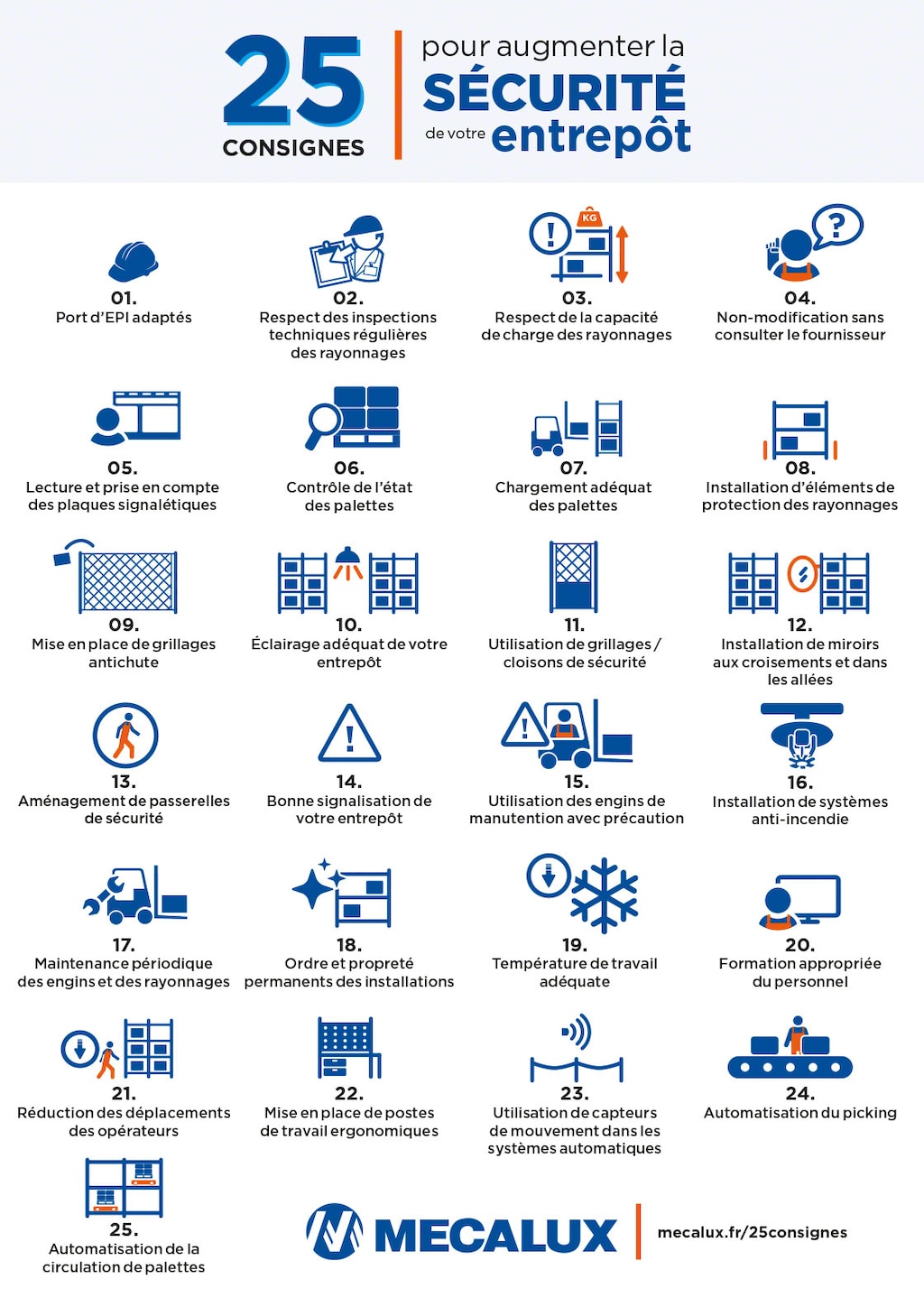
Cap sur un entrepôt entièrement sécurisé
En respectant les 25 consignes de sécurité ci-dessus, vous serez en mesure de renforcer la sécurité de vos opérateurs, de vos produits et de vos systèmes de transport et de stockage, ce qui se traduit par une productivité accrue de votre entreprise.
Un entrepôt sûr est synonyme d’efficacité logistique. Il contribue à une chaîne d’approvisionnement compétitive, tout en réduisant les erreurs, les surcoûts et une multitude de scénarios nuisibles à l’entreprise.
Vous souhaitez protéger votre entrepôt contre les risques ? Contactez-nous, un de nos experts étudiera vos besoins et vous proposera une solution adaptée.