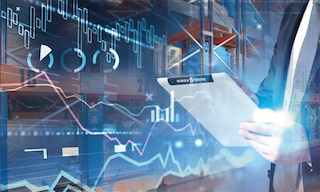
7 formules pour une gestion efficace des stocks
Il existe plusieurs formules pour calculer les paramètres clés de la gestion des stocks dans un entrepôt. Il s’agit notamment du calcul du stock de sécurité pour chaque référence, du point de commande d’un produit, des coûts économiques suite à une rupture de stock et du niveau de service de l’installation.
Il est essentiel de mettre en place une méthode de calcul périodique de ces indicateurs de performance afin que e responsable logistique puisse prendre des décisions basées sur la productivité réelle des opérations.
Les principales formules de gestion des stocks dans l’entrepôt
Une bonne gestion des stocks dans l’entrepôt accroît la productivité des opérations logistiques et élimine les surcoûts. Voici les principales formules à connaître pour déterminer le succès du contrôle des stocks :
1. Délai de livraison (lead time d’approvisionnement)
Le délai de livraison, également connu en logistique sous le nom de lead time ou temps de cycle, est un indicateur qui mesure le temps qui s’écoule entre le moment où l’entrepôt passe une commande à un fournisseur et celui où la marchandise est reçue.
La formule du délai de livraison est la suivante :
Lead time = date de livraison - date de commande
Si une entreprise passe une commande de matières premières le 15 de chaque mois et la reçoit le 23, le lead time sera calculé comme suit :
23 - 15 = 8 jours de lead time
Cet indicateur logistique, mesuré en jours, donne au responsable logistique un aperçu de l’efficacité de la chaîne d’approvisionnement de l’entreprise.
2. Stock de sécurité
Le stock de sécurité correspond à des stocks de réserve présents dans un entrepôt. Avec cette marchandise supplémentaire, l’entreprise peut faire face à des évènements imprévus tels que des pics de demande pour un produit, des changements inattendus dans la rotation d’une référence ou encore des retards de livraison de la part des fournisseurs.
Formule du stock de sécurité
Stock de sécurité = (délai de livraison maximum - délai de livraison moyen) x demande moyenne pour le produit
Par exemple, un centre de production a besoin de 200 unités d’un produit pour exécuter les ordres de production existants. Si le délai de livraison moyen est de 5 jours et que le délai de livraison maximum du fournisseur est de 8 jours, le stock de sécurité sera le suivant :
(8 - 5) x 200 = 600 unités de stock de sécurité
Ce KPI de sécurité vise à garantir une certaine quantité de stock afin d’éviter les ruptures de stock, c’est-à-dire la confirmation de commandes qui ne peuvent pas être traitées en raison d’un stock insuffisant.
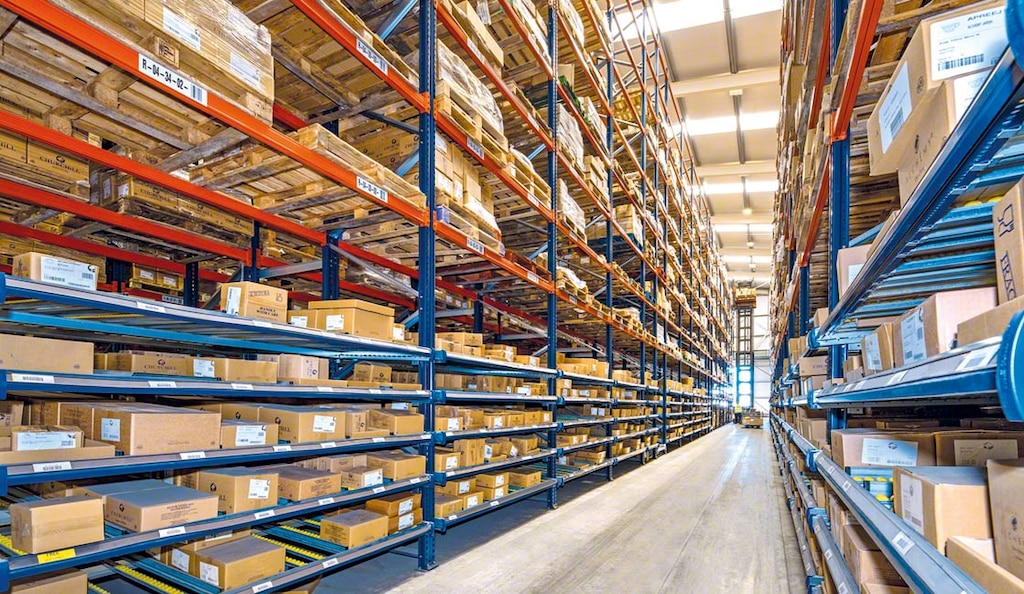
3. Rupture de stock
Une rupture de stock se produit lorsque l’entrepôt reçoit une commande mais ne dispose pas du produit dans les quantités nécessaires pour répondre à cette demande.
La formule de coût de rupture de stock est la suivante :
Rupture de stock = quantité de stock non fournie x coût unitaire de stockage
Autrement dit, si une entreprise est dans l’incapacité de traiter 30 commandes et que chaque commande a une valeur de 2,5 €, le coût de rupture de stock sera de :
30 x 2,50 € = le coût de rupture de stock est de 75 €
Cet indicateur est souvent calculé en pourcentage, c’est-à-dire le nombre de ruptures de stock par rapport au nombre total de commandes reçues.
Taux de rupture de stock = (quantité de stock non fournie) / (quantité totale demandée) x 100
En suivant l’exemple ci-dessus, le pourcentage de rupture de stock peut être calculé. Si l’entreprise n’est pas en mesure de fournir 30 commandes sur 300, le calcul sera le suivant :
(30/300) x 100 = taux de rupture de stock de 10 %
Bien que cette formule soit utilisée pour indiquer le pourcentage de commandes non honorées, il faut tenir compte du fait que l’incapacité à fournir une marchandise ou un produit à un client entraîne d’autres conséquences, par exemple la méfiance à l’égard du service logistique.
4. Point de commande
Le point de commande est une formule appliquée dans l’entrepôt pour identifier le moment précis où une entreprise doit passer commande à ses fournisseurs. Le but est d’assurer la continuité du flux de travail ou de production et d’optimiser l’espace de stockage.
La formule du point de commande est la suivante :
Point de commande = stock de sécurité + (consommation moyenne x lead time)
Prenons un exemple qui illustre le calcul du point de commande : une entreprise a une consommation moyenne quotidienne de 1 000 unités et un lead time de 4 jours. Si le stock de sécurité est de 1 000 unités, le point de commande sera déterminé comme suit :
1 000 + (1 000 x 4) = 1 000 + 4 000 = 5 000 est la quantité exacte de stock qui doit servir d’indicateur pour déclencher une nouvelle commande au fournisseur.
Cette donnée, qui doit être réévaluée régulièrement, fournit au responsable logistique le volume de stock optimal pour passer une commande de réapprovisionnement de stock, en tenant compte de l’équilibre exact entre le coût d’investissement des marchandises et le risque de rupture de stock.
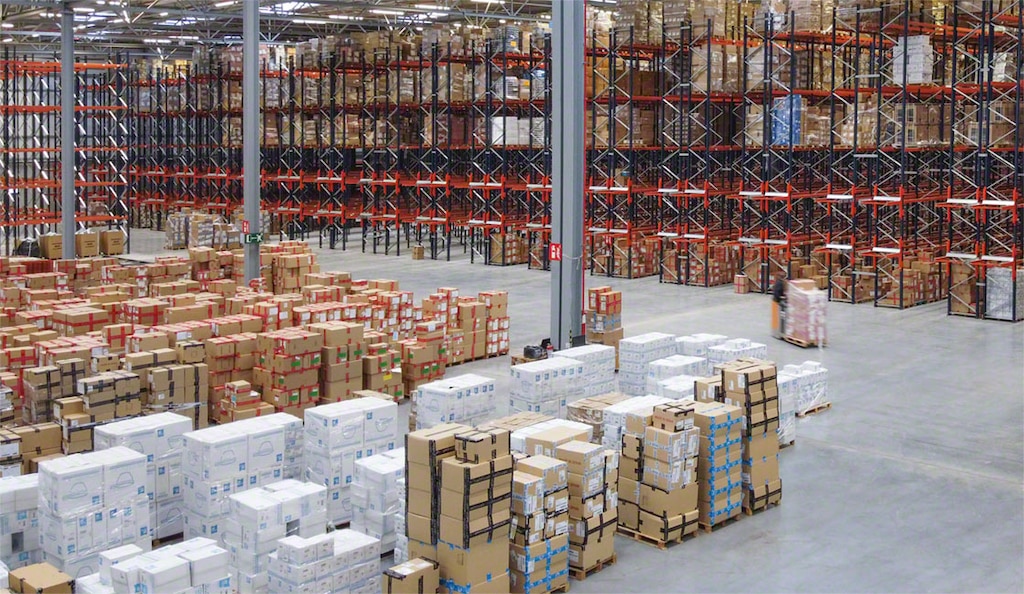
5. Stock maximum
Le stock maximum désigne le volume exact de marchandises qu’un entrepôt peut stocker sans entraîner de coûts de stockage supplémentaires pour l’entreprise.
La formule de calcul de stock maximum :
Stock maximum = Point de commande + quantité de réapprovisionnement - (demande minimum x Lead Time)
Pour calculer le stock maximum, nous prenons l’exemple de l’entreprise précédente qui avait un point de commande de 5 000 unités et un lead time de 4 jours. Si la quantité de réapprovisionnement pour chaque commande est de 8 000 unités et que la demande minimale est de 1 000 unités, le stock maximal sera de :
(5 000 + 8 000) - (1 000 x 4) = 13 000 - 4 000 = 9 000 unités de stock maximum dans l’entrepôt
Cet indicateur détermine le niveau maximal de stock pour fournir aux clients un service logistique au coût le plus bas possible.
6. Quantité de commande économique
La quantité économique de commande (EOQ) est un concept logistique qui détermine quand passer commande auprès d’un fournisseur et en quelle quantité. Elle est calculée à partir de la formule mathématique connue sous le nom de modèle de Wilson.
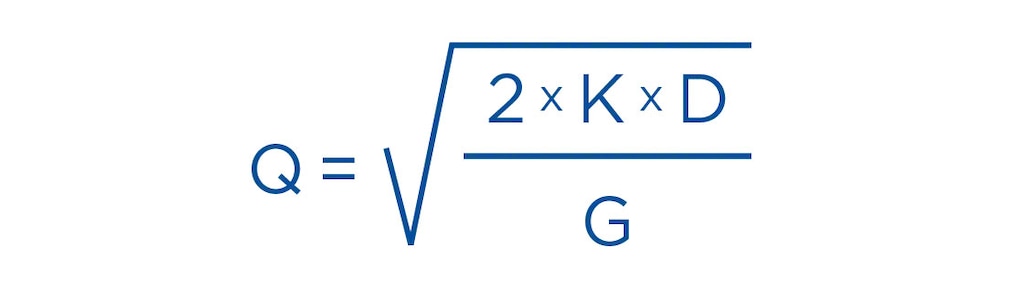
Q = quantité économique de commande
K= coût associé à chaque commande passée
D = demande annuelle de la matière première/produit
G = coût de stockage de la matière première dans l’entrepôt
Pour simplifier l’explication, prenons l’exemple suivant : une entreprise a besoin de 500 kg de produit pour répondre à la demande annuelle de ses lignes de production. Si le coût de passation de chaque commande est de 2 500 euros et le coût de stockage de la matière première de 25 000 euros par an, le calcul de la quantité économique de commande serait :
Racine carrée de (2 x 2 500 x 500 / 25 000) = 10 kg est la quantité économique de commande à commander pour avoir suffisamment de matière première sans augmenter les coûts de stockage.
La formule EOQ permet également de déduire le nombre de commandes qui doivent être passées annuellement pour répondre à la demande. Selon les calculs ci-dessus, l’entreprise devrait passer 50 commandes annuelles de 10 kg pour atteindre les 500 kg de produit nécessaires pour exécuter les ordres de production.
7. Taux de rotation des stocks
La rotation des stocks est un indicateur logistique qui définit le nombre de fois où les stocks ont été vendus sur une période donnée, généralement un an. Autrement dit, ce paramètre mesure le nombre de fois que les produits stockés complètent un cycle de vente (c’est-à-dire qu’ils sont vendus, quittent l’entrepôt et sont encaissés).
La formule du taux de rotation des stocks est la suivante :
Taux de rotation des stocks = valeur économique des références vendues / valeur moyenne des références stockées
Par exemple, si une entreprise vend tous ses produits en un an pour un montant total de 1 600 000 euros et que la valeur moyenne du stock dans l’entrepôt est de 400 000 euros, le taux de rotation des stocks sera calculé comme suit :
1 600 000 / 400 000 = 4 est le taux de rotation des stocks.
Ainsi, cette entreprise a un taux de rotation des stocks de 4, ce qui signifie qu’elle renouvelle son stock quatre fois par an (une fois par trimestre).
Un logiciel pour automatiser la gestion des stocks
La logistique 4.0 a fait apparaître de nouveaux défis dans la gestion des stocks. De nos jours, de plus en plus d’entreprises mettent en place une stratégie omnicanale (ou du moins, multicanale) qui permet d’expédier des commandes à la fois en ligne et en magasins physiques. Dans ce contexte, les responsables logistiques s’appuient sur des solutions numériques qui automatisent le contrôle des stocks et assurent la traçabilité des produits. Un exemple de ce type d’application est un logiciel de gestion d’entrepôt comme Easy WMS de Mecalux. Ce logiciel gère les opérations de l’entrepôt en fonction de paramètres tels que le stock de sécurité, le stock moyen ou le point de commande.
De plus, le logiciel Mecalux dispose de la fonctionnalité avancée Supply Chain Analytics. Ce module surveille les performances des opérations de l’entrepôt et collecte automatiquement toutes les informations générées dans l’installation. Grâce à ces données, le responsable logistique peut calculer plus rapidement et de manière plus fiable des paramètres clés tels que la quantité économique de commande ou les coûts de rupture de stock.
Formules de gestion des stocks : contrôle de tout ce qui se passe dans l’entrepôt
Les responsables logistiques utilisent plusieurs formules pour avoir un suivi quasi-instantané de l’état du stock dans l’entrepôt, pour connaître les coûts liés au stockage des produits ou le coût d’une rupture de stock.
Toutefois, de plus en plus de responsables mettent en œuvre un logiciel de gestion d’entrepôt pour les assister dans la gestion des stocks : Ces programmes numérisent les informations, automatisent les tâches et permettent à la direction de disposer de toutes les informations nécessaires à la prise des décisions stratégiques pour l’entrepôt.
Si vous souhaitez numériser vos opérations d’entrepôt pour optimiser les processus et améliorer la gestion des stocks, n’hésitez pas à nous contacter. L’un de nos experts vous conseillera sur la meilleure solution pour votre entreprise.