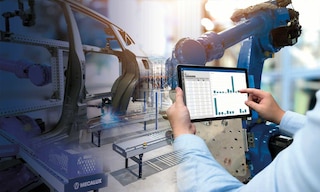
Stratégie Push and Pull appliquée à la logistique de production
Les stratégies push et pull en logistique sont les deux méthodes de production les plus utilisées à l’impact direct sur la gestion des stocks, la pierre angulaire de l’entrepôt. Un produit doit-il être fabriqué à l’avance ou au moment de son achat ? Choisir l’une ou l’autre stratégie a des conséquences importantes, non seulement sur la manière de produire, mais aussi sur l’organisation de l’entrepôt et de la logistique. Le choix aura également un impact direct sur les coûts et la rentabilité de l’entreprise.
Dans cet article, nous analysons et expliquons les avantages, les inconvénients et les différences entre le système push et le système pull, et leur impact sur la logistique de production de chaque entreprise.
Stratégie Push et Pull : définition et comment les différencier ?
Push et Pull sont des processus de production qui se caractérisent par une organisation de la fabrication en fonction de la demande. La différence réside dans le choix du moment où la production commence : avant ou après l’achat du produit.
Avec la méthode push (flux poussé en français), le produit est fabriqué à l’avance. Par conséquent, ce modèle est basé sur la prévision de la demande, car il devient nécessaire de savoir au préalable et avec la plus grande précision quels produits les clients auront besoin, quand et en quelle quantité.
La méthode pull (flux tiré en français), quant à elle, adapte la production à la demande réelle, ce qui signifie que le produit est fabriqué seulement lorsqu’un achat est effectué, dès réception de la commande, qui se voit ainsi attribuer une date de livraison spécifique. Cette approche ne tient pas compte de la disponibilité du stock de produits finis, et elle est la plus utilisée par les entreprises spécialisées dans les produits à la demande ou entièrement personnalisés. Cette méthode est très courante également dans l’industrie automobile.
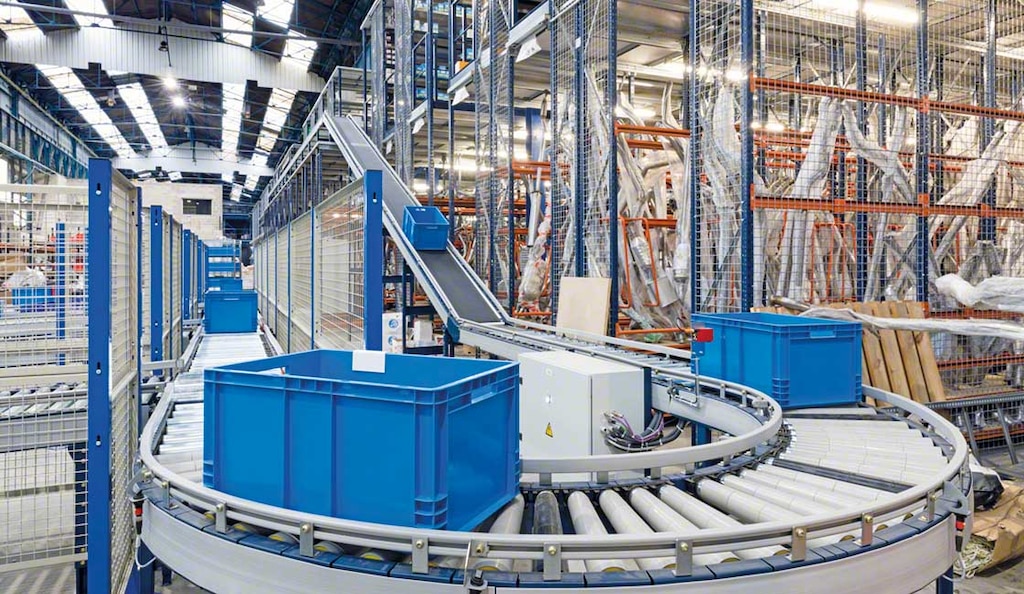
Avantages et inconvénients du système push
L’avantage le plus notable du système push est que les coûts de production par unité de produit sont réduits au minimum car il peut être fabriqué en grandes quantités. C’est ce qu’on appelle l’économie d’échelle : le fournisseur diminue ses coûts en augmentant son volume de production. Pour s’adapter aux éventuelles variations de la demande, il est primordial que le système de production soit rapide et flexible. De cette façon, l’entreprise optimisera son approvisionnement logistique, pourra satisfaire la demande et minimiser les coûts opérationnels et de stockage en ayant une plus grande planification de l’activité.
Le principal inconvénient de cette stratégie est lié aux risques associés à d’éventuelles erreurs dans la planification de la demande, telles que le risque de rupture de stock (la demande dépasse les prévisions de vente) ou bien le risque de surstock (la production dépasse significativement la demande estimée).
Avantages et inconvénients du système pull
Les principaux avantages du système pull sont l’élimination de la surproduction et la réduction des coûts de stockage. Autrement dit, la forte dépendance entre la fabrication et l’analyse prédictive (destinée à anticiper les changements dans les habitudes de consommation) est minimisée. La grande majorité des entreprises qui travaillent selon le modèle pull adoptent la stratégie du just-in-time (JIT), qui optimise les coûts de gestion et est étroitement lié à la philosophie de Lean logistics, dont l’objectif principal est de réduire les coûts logistiques en éliminant les processus qui n’apportent pas de valeur réelle.
Un autre atout de la stratégie pull et de la production à la demande est la capacité de personnaliser un produit au goût du client, devenant ainsi un avantage concurrentiel.
De même, la stratégie pull est généralement choisie lorsque l’on opte pour des pratiques logistiques plus durables en vue de minimiser l’impact environnemental aux étapes de fabrication et de stockage des produits.
L’inconvénient le plus notable du système pull est, qu’en général, le temps de production est plus long, ce qui oblige les entreprises à avertir leurs clients que la livraison du produit ne sera pas immédiate. Par ailleurs, le coût de fabrication par unité augmente : le bien n’est pas fabriqué en masse et il n’est donc pas possible de réaliser des économies d’échelle.
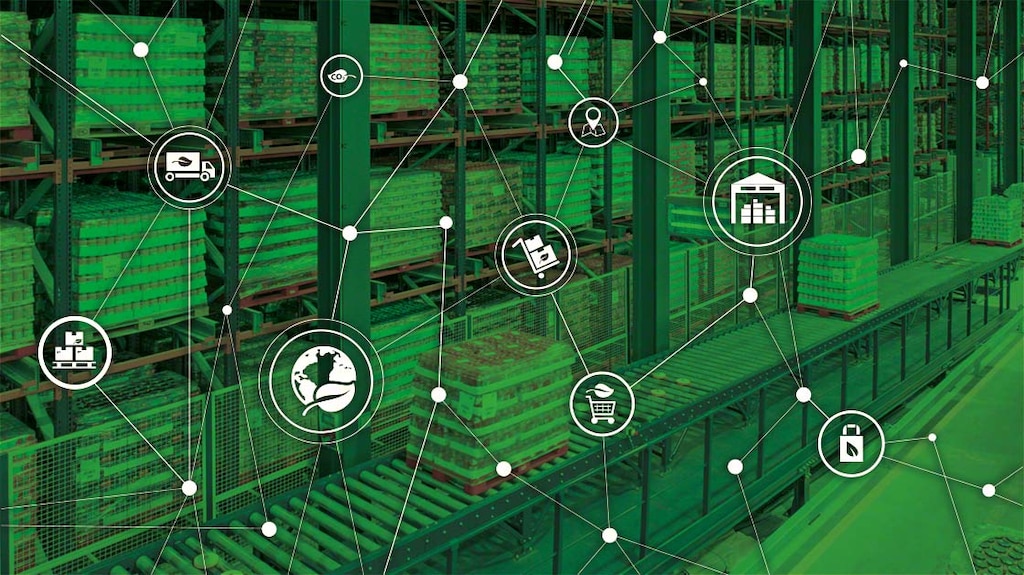
Adapter sa stratégie logistique à la méthode Push ou Pull
Au niveau logistique, le choix entre la stratégie de production push ou pull à une incidence sur les caractéristiques et les opérations de l’entrepôt :
- Capacité de stockage : si vous optez pour un système push, vous aurez besoin de plus d’espace de stockage, car tout le stock produit pour anticiper la demande sera stocké dans l’entrepôt. Les rayonnage à palettes compacts sont la solution idéale pour optimiser l’espace de stockage.
- Préparation des commandes : elle doit être rapide et efficace lors de la mise en place de la stratégie pull, pour fournir alimenter au bon moment les lignes de production en marchandise.
- Flux : l’utilisation de systèmes de stockage et d’équipements de manutention automatique, tels que des convoyeurs pour palettes ou des balancelles automotrices, permettent de relier l’entrepôt avec l’usine de production, élément clé pour l’application du modèle pull.
- Gestion des stocks : quelle que soit la stratégie choisie, il est essentiel de suivre les flux au sein d’un entrepôt et, en même temps, d’effectuer le suivi du stock. Pour cela, il est fortement recommandé de mettre en place des outils d’aide à la gestion comme un logiciel de gestion d’entrepôt (WMS), en plus d’un ERP et d’un MRP (Material Requirements Planning).
La logistique de toute entreprise de fabrication est directement liée à la stratégie de production adoptée. Pour cette raison, il est essentiel d’ajuster cette stratégie afin que la chaîne d’approvisionnement soit aussi efficace que possible.
Exemples d’application du système push et pull
Le choix du système de production est principalement déterminé par le type de produit fabriqué et sa demande.
Généralement, le modèle push est utilisé dans des industries ou des entreprises où la demande est plus facile à prédire, telles que celles liées aux produits à forte saisonnalité. Un exemple typique est Schaal Chocolatier, un leader de la production de chocolat haut de gamme qui utilise le système de production push pour anticiper l’augmentation de la demande à certaines périodes de l’année, en particulier à Pâques et à Noël. Afin d’avoir une chaîne d’approvisionnement efficace, Schaal Chocolatier dispose d’un entrepôt automatisé pour palettes, technologique et moderne, développé par Mecalux.
La méthode pull est fortement recommandée pour les entreprises qui commercialisent des produits à coût de production élevé, rendant impossible leur mise en stock dans l’attente d’une vente. Cette stratégie est également utilisée pour les produits avec un degré élevé de personnalisation afin de répondre au mieux aux demandes du client. C’est le cas pour le fabricant de meubles Forma 5. Sa logistique est basée sur la méthode just-in-time, c’est-à-dire que l’usine de production est reliée aux 35 entrepôts de ses fournisseurs par le biais du logiciel de gestion d’entrepôt Easy WMS de Mecalux afin de recevoir en temps voulu les produits semi-finis demandés.
D’ailleurs, certains secteurs utilisent une stratégie de gestion combinée push et pull. Dans l’industrie automobile, par exemple, des véhicules sont fabriqués en série, avec un équipement standard (système push), mais aussi d’autres qui sont personnalisés à la demande, avec des options (système pull). Le constructeur automobile Zbeda Group (Israël) s’est doté d’un magasin automatique pour bacs (également conçu et installé par Mecalux) qui fournit les lignes de production à la fois pour la production de véhicules à la demande et en série.
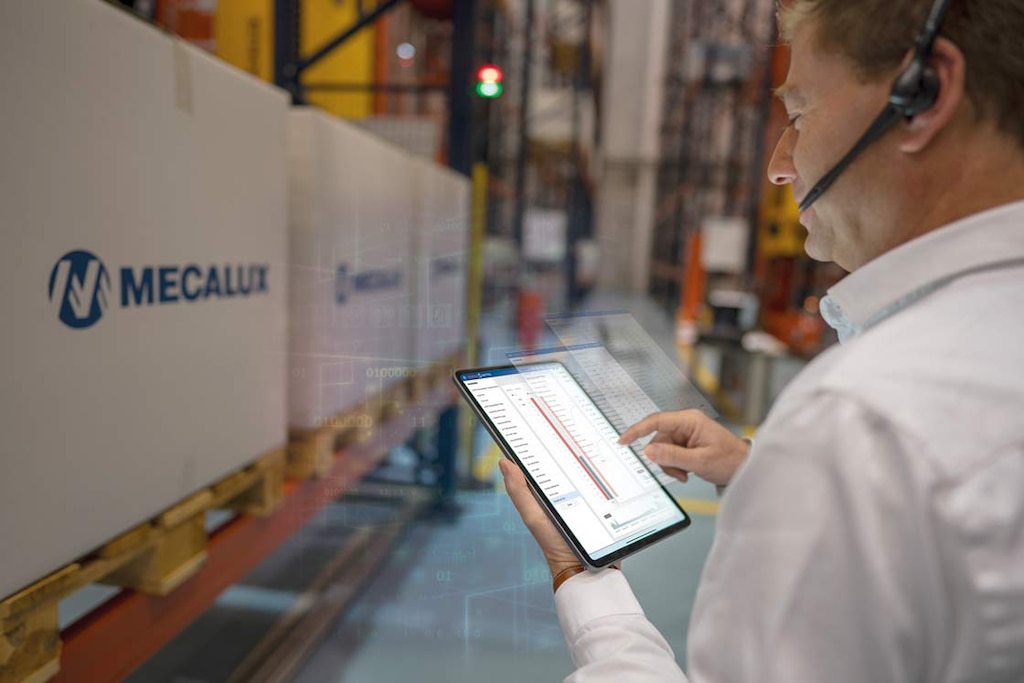
Stratégies adaptées aux exigences de la logistique de production
Gérer l’approvisionnement et surveiller efficacement le processus de prévision de la demande et son impact sur les stocks sont les principaux défis logistiques pour tout fabricant, même si les spécificités de ces exigences sont déterminées par la stratégie de production.
Si vous envisagez de mettre en place un système de production push ou pull et que vous pensez que votre intralogistique n’est pas prête pour cela, contactez Mecalux. Un expert vous conseillera pour trouver la solution la mieux adaptée à vos besoins.