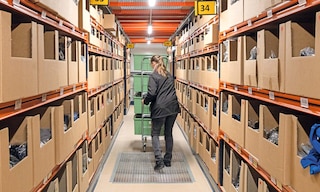
45 conseils pour optimiser la préparation de commandes en entrepôt
La préparation de commandes est généralement l’une des opérations qui cause le plus de soucis dans un entrepôt, en raison de sa complexité, de son coût élevé et du risque d’erreur, entre autres. Dans cet article, nous vous donnons 45 conseils qui, correctement appliqués, peuvent aider à réduire les coûts du processus de préparation de commandes, en l’accélérant et, surtout, en limitant les erreurs dans cette étape logistique.
1. Agencer efficacement son entrepôt
L’agencement d’un entrepôt doit permettre de bien délimiter les zones de picking et de les organiser selon l’ordre de préparation d’une commande : de la réception au stockage, en passant par le réapprovisionnement, la préparation de la commande ou les zones d’emballage. Il est important de coordonner les opérations afin d’éviter les déplacements inutiles.
2. Séparer la zone de picking de la zone des retours
C’est une erreur fréquente d’installer les postes de traitement des retours produits à proximité des zones de préparation des commandes. La séparation des deux zones permet d’éviter les pertes de stocks et la mauvaise gestion des stocks.
3. Mettre en œuvre un WMS pour digitaliser la gestion des stocks
La mise en œuvre d’un logiciel de gestion d’entrepôt garantit une traçabilité totale des produits et un contrôle rigoureux de la préparation des commandes. Le programme organise les différentes stratégies de picking, tout en indiquant à l’opérateur les étapes à suivre dans cette phase.
4. Stocker les marchandises à des emplacements stratégiques
Le responsable de l’entrepôt doit déterminer un ensemble de critères et de règles de stockage des marchandises en fonction de la demande réelle des marchandises (rotation, type de produit, etc.). L’installation d’un logiciel de gestion d’entrepôt minimise les risques d’erreurs dans cette opération et optimise le slotting, c’est-à-dire la gestion des emplacements dans l’entrepôt.
5. Choisir des systèmes de stockage adaptés à l’entrepôt
La planification logistique doit inclure les systèmes de stockage qui correspondent le mieux aux caractéristiques de l’entrepôt, au type de produits stockés ou aux flux de marchandises et stocks qui se trouvent dans l’installation.
6. Installer des rayonnages dynamiques pour différencier les opérations
Les rayonnages dynamiques pour picking sont la solution idéale, car ils augmentent le nombre de lignes de picking et réduisent les déplacements des opérateurs. Ces systèmes de stockage augmentent l’efficacité du picking d’unité en vrac.
7. Le picking dans des rayonnages à palettes
Le picking sur palettes est une solution optimale lorsque chaque palette ne contient qu’une seule référence. De même, pour préparer les commandes directement dans un rayonnage à palettes, il est recommandé de placer les références les plus commandées aux niveaux inférieurs.
8. Concevoir des itinéraires de picking visant à maximiser la rapidité et l’efficacité
Les déplacements des opérateurs représentent une grande partie des coûts de préparation des commandes. Un logiciel d’entrepôt (comme Easy WMS de Mecalux) optimise les itinéraires des opérateurs en tenant compte de la méthode de picking et du slotting prédéterminé par le responsable logistique.
9. Allouer plus d’espace au picking
Les systèmes de stockage compacts, tels que les rayonnages par accumulation drive-in, Movirack ou Pallet Shuttle, réduisent la surface dédiée au stockage pour réserver une plus grande partie de l’entrepôt à la préparation des commandes.
10. Identifier les goulets d’étranglement
Il est essentiel que le responsable logistique soit à l’écoute de ses collaborateurs et détecte les goulets d’étranglement, ainsi que les améliorations possibles des méthodes de picking. Un logiciel tel que le module d’Easy WMS Gestion de la Main d’Œuvre peut aider à détecter les inefficacités et à équilibrer la charge de travail entre les différents opérateurs.
11. Intégrer le WMS à l’ERP
Les opérations supervisées par un WMS doivent être alignées sur les stratégies de l’entreprise. Le WMS doit être synchronisé avec l’ERP pour échanger automatiquement les informations de la commande ― références ou conditions de livraison ― assurant ainsi une communication bidirectionnelle entre le service logistique et les différents départements de l’entreprise.
12. Suivre le stock en temps réel
Le contrôle des stocks est l’une des opérations clés pour une préparation de commandes efficace. La digitalisation de l’inventaire à l’aide d’un WMS est la meilleure façon de contrôler ses stocks en temps réel.
13. Réapprovisionner les stocks à temps
Il n’y a rien de plus inefficace pour le picking que d’arriver à un emplacement et constater qu’il est vide des marchandises nécessaires à la commande. Pour optimiser les déplacements des opérateurs, il est nécessaire de toujours garantir des niveaux de stock minimums (stock de sécurité), en assurant un réapprovisionnement continu des emplacements de stockage.
14. Digitaliser et automatiser la documentation
La préparation de commandes manuelle implique la gestion d’une documentation de base tels que les bons de livraison, les picking lists ou les feuilles de route. La gestion papier augmente les risques d’erreurs. Un WMS par exemple, automatise la gestion des picking lists ainsi, l’opérateur n’a qu’à suivre les instructions du logiciel.
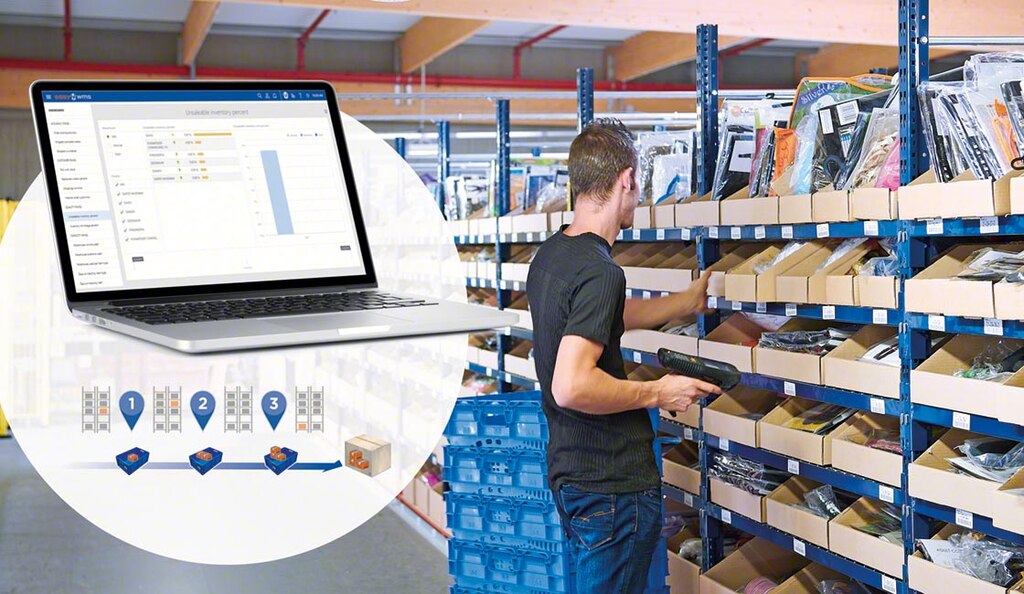
15. Définir des KPI pertinents
Le responsable logistique doit sélectionner les KPI logistiques liés à la préparation de commandes qui correspondent le mieux au type d’activité, aux caractéristiques du produit ou aux différentes stratégies de picking mises en place dans l’entrepôt.
16. Automatiser la mesure des performances de l’installation
Pour atteindre une productivité maximale dans la préparation de commandes, il est fondamental de pouvoir compter sur un outil qui automatise l’analyse des données. Un programme tel que le module Easy WMS Supply Chain Analytics donne au responsable logistique une visibilité complète et en temps réel sur la performance de l’entrepôt.
17. Calculer le délai de traitement des commandes
Cet indicateur de performance détermine le temps nécessaire à l’exécution d’une commande, entre le moment où elle arrive dans le système (via ERP ou WMS) et celui où elle est prête à être expédiée. Ce calcul permet de contrôler le stock de l’entrepôt, l’efficacité de la préparation des commandes et la qualité du service client.
18. Anticiper l’évolution de la demande
Les critères et les règles préétablis pour le stockage des produits doivent être constamment revus afin de détecter les changements dans les tendances du marché, la saisonnalité de certains produits ou les pics de demande. La prévision des scénarios possibles, grâce à des outils d’analyse prédictive, permet de prendre des décisions en fonction des performances réelles de l’entrepôt.
19. Automatiser le flux des marchandises
Le remplacement des engins de manutention manuelle par des systèmes de transport automatisé comme des convoyeurs pour bacs accélère les flux des marchandises, notamment vers les postes de picking.
20. S’équiper de dispositifs d’aide au picking
La clé pour maximiser l’efficacité du picking est d’opter pour des méthodes de préparation de commande semi-automatiques. Des systèmes comme le pick-to-light ou le voice picking permettent au logiciel de gestion d’entrepôt de guider l’opérateur, en lui indiquant étape par étape les tâches à effectuer.
21. Etudier les solutions robotiques
Les robots pick and place assistent les opérateurs réalisant le picking dans le but de réorienter les opérateurs vers des tâches à plus grande valeur ajoutée telles que la préparation de commandes personnalisées. Les cobots (robots collaboratifs) sont des solutions qui facilitent le travail des opérateurs, en interagissant avec eux et en prenant en charge les tâches les plus physiques et les plus pénibles de la préparation des commandes.
22. Automatiser le picking avec un système « goods-to-man »
Le goods-to-person est une méthode de préparation de commande dans laquelle les marchandises parviennent à l’opérateur au moyen de systèmes de transport automatisé comme des convoyeurs pour palettes ou pour bacs. Le WMS coordonne l’ensemble de l’opération pour assurer un picking efficace.
23. Améliorer les réceptions
Un processus de réception des marchandises bien organisé et efficace simplifie la préparation des commandes. Dans la zone de réception des marchandises, les opérateurs sont généralement équipés de terminaux mobiles connectés au logiciel de gestion d’entrepôt pour mieux contrôler les réceptions et la vitesse des flux de produits vers les différentes zones de stockage ou de picking.
24. Mettre en place des stratégies de picking adaptées
Déterminer à l’avance les stratégies de picking en fonction des flux de marchandises et du type de produit améliore l’efficacité de l’installation. Les principales méthodes de préparation de commandes sont par exemple, le wave picking (picking par vagues), le batch picking ou le picking par zone.
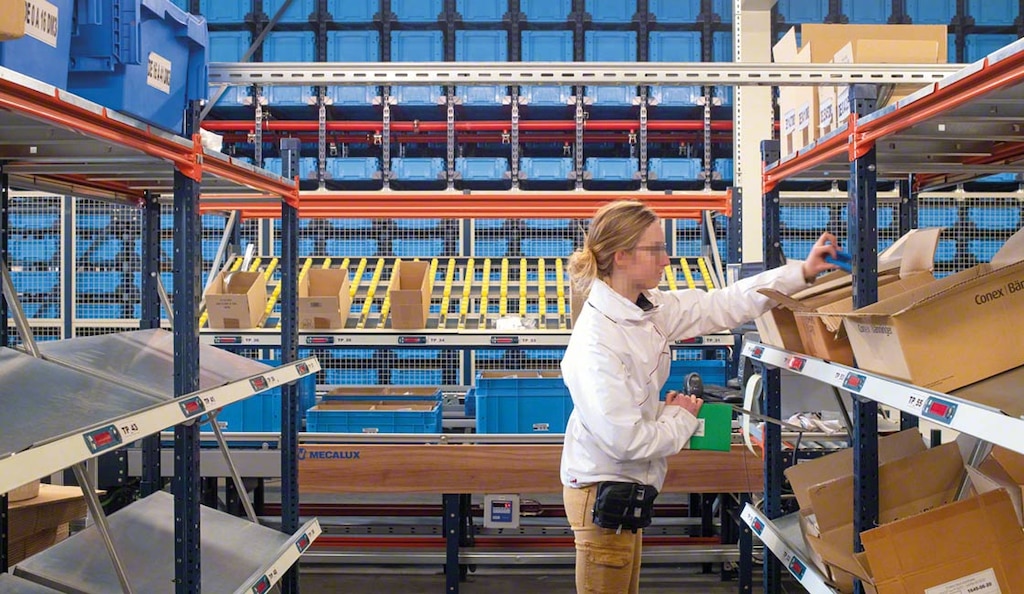
25. Essayer le « pick-to-box »
L'une des méthodes de préparation manuelle des commandes très rentable est le "pick to box", une technique de préparation qui consiste à retirer les marchandises des rayonnages et à grouper plusieurs commandes en même temps, intégrant ainsi trois phases différentes de préparation des commandes en une seule phase, à savoir : le picking, la consolidation et l'emballage des articles.
26. Évaluer les avantages du « cross-docking »
Le cross-docking est une technique de préparation de commande qui consiste à expédier les marchandises directement au client final sans passer par une période de stockage. Cette méthode nécessite la conception de zones de transit spécifiques ou de systèmes de stockage qui servent de tampon de stockage temporaire pour les produits reçus.
27. Étiqueter correctement les marchandises
Un mauvais étiquetage peut ruiner la meilleure stratégie de préparation de commande. C’est pourquoi, il est crucial que le responsable logistique valide le processus d’étiquetage pour s’assurer que le système fonctionne correctement.
28. Adopter la philosophie « Lean »
Le lean logistics est une philosophie d’organisation des opérations dans laquelle est recherchée l’efficacité maximale de chaque opération, en éliminant celles qui n’ajoutent pas de valeur. Il est nécessaire d’analyser les processus de préparation des commandes et de déterminer quelles étapes sont dispensables pour atteindre une productivité maximale.
29. Éliminer les déplacements inutiles
Pour améliorer le picking, tous les mouvements et les prélèvements ou picks effectués par un opérateur dans l’entrepôt doivent être optimisés. Tout déplacement inutile peut entraîner une augmentation du coût logistique du produit.
30. Structurer les listes de picking
Lors de l’élaboration des listes de picking, il est important de considérer dans quel ordre placer les produits de la liste afin qu’ils rentrent dans le colis d’expédition. Un WMS peut séquencer les mouvements de sorte que les plus grands produits soient collectés en premier.
31. Intégrer les dimensions des produits dans le WMS
Les mesures et le poids des marchandises peuvent être intégrés dans le système de gestion d’entrepôt pour augmenter la précision dans la préparation des commandes. Si, par exemple, une unité d’un produit est manquante, le logiciel signalera que la commande est toujours incomplète.
32. Évitez de placer plusieurs références pour différentes commandes dans le même chariot
Placer différents produits de différentes commandes dans le même chariot augmente le risque d’erreur, en particulier lorsque l’opérateur n’est assisté d’aucun dispositif d’aide au picking. Toute erreur au cours de cette opération peut entraîner un allongement du temps de préparation de la commande et une augmentation des coûts.
33. Réaliser le « kitting » avant le picking
Pour optimiser la préparation des commandes, l’assemblage des kits doit être fait avant le processus de picking. Si le nombre exact de kits requis ne peut pas être calculé, il est recommandé d’en préparer à l’avance.
34. Minimiser les retours
Le logiciel de gestion d’entrepôt est l’outil idéal pour éliminer le risque d’erreur et minimiser les retours de produits résultant d’un picking incorrect.
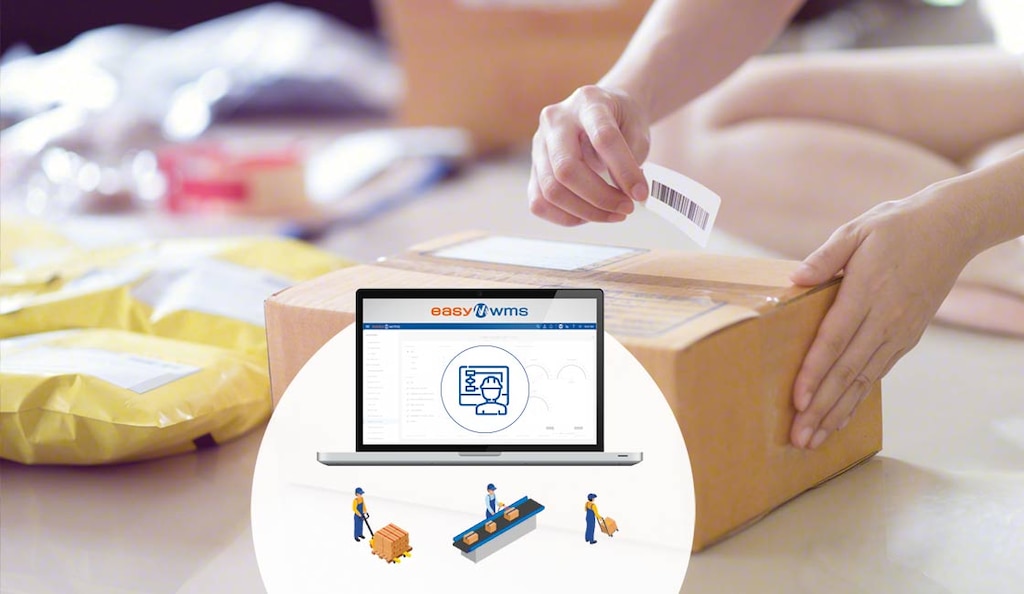
35. Garantir l’équipement nécessaire à tous les employés
Les opérateurs doivent disposer de tout ce dont ils ont besoin pour accomplir leurs tâches dans les plus brefs délais : terminaux mobiles, chariots, transpalettes, chariots élévateurs, etc.
36. Aménager des postes de travail ergonomiques
Les postes de préparation des commandes nécessitent une conception ergonomique pour le confort de l’opérateur. Ils doivent également être équipés de tous les éléments nécessaires pour éviter les déplacements inutiles.
37. Assurer la sécurité de l’installation
Tout processus est plus fluide et plus rapide si l’on favorise un environnement industriel sécurisé pour l’installation, les marchandises et les opérateurs dans lequel l’ordre et la propreté sont une priorité.
38. Le marquage au sol dans l’entrepôt
Pour un entrepôt efficace et surtout sécurisé, il est nécessaire de signaliser correctement les différents secteurs de l’installation. Cet espace est partagé entre les opérateurs, les marchandises et les engins de manutention ― manuels ou automatiques ― et un mauvais marquage pourrait augmenter le risque d’incidents.
39. Eclairer correctement l’installation
Un bon éclairage dans les entrepôts aide les préparateurs de commandes à identifier les emplacements de stockage, et renforce la sécurité dans l’installation. L’éclairage est un facteur particulièrement important dans les installations logistiques où circulent des engins de manutention manuelle.
40. Former les opérateurs
Pour une préparation des commandes efficace, il est essentiel de former les opérateurs à l’utilisation des différents systèmes de stockage, des engins de manutention et même des produits. Les pickers doivent parfaitement connaître l’installation, les modifications dans le slotting c’est-à-dire l’emplacement des produits, et le marquage dans l’entrepôt.
41. Informer en interne de la stratégie en place
Il est recommandé d’expliquer au personnel la stratégie de gestion de l’entrepôt, en justifiant la raison de l’exécution de chaque opération dans l’installation.
42. Intégrer des techniques de gamification
Comme dans tous les environnements de travail, le renforcement de la motivation et de la compétitivité sont un pilier de la performance maximale. L’utilisation de techniques de gamification ― concours, challanges, picker du mois, etc. ― est de plus en plus courante pour renforcer l’engagement des employés.
43. Évaluer le bénéfice de faire appel à un 3PL
Pour faire face à des hausses inattendues de la demande, les entreprises peuvent faire appel à un prestataire logistique externe (3PL) pour les accompagner dans les opérations de stockage et de préparation de commandes.
44. Diversifier les stratégies à mesure que l’entreprise se développe
Les nouvelles tendances du marché exigent que les entrepôts soient flexibles, capables de s’adapter à toute modification de la demande ou à toute interruption de la chaîne d’approvisionnement. Il est nécessaire de disposer d’une logistique élastique et de préparer les opérateurs à tout événement imprévu.
45. Examiner périodiquement les processus logistiques
Les entrepôts nécessitent une planification logistique flexible, capable de revoir constamment les flux de marchandises dans la préparation de commandes afin de s’adapter aux changements de type de SKU, aux flux de la chaîne d’approvisionnement ou à la consolidation des commandes.
Un picking hautement efficace adapté aux nouveaux enjeux
Les tendances de consommation actuelles nécessitent de multiplier l’efficacité de toutes les opérations logistiques, en particulier les plus coûteuses, comme la préparation de commandes. Les standards logistiques du commerce électronique (délais de livraison courts et retour gratuit des produits, entre autres) forcent les entrepôts à augmenter les performances aux postes de picking. La mise en œuvre d’un logiciel de gestion d’entrepôt garantit une augmentation de la productivité de l’entrepôt.
Chez Mecalux, nous sommes experts en solutions de stockage et intralogistiques qui favorisent l’efficacité et la productivité d’un entrepôt. Si vous souhaitez optimiser votre logistique et vos processus de picking, n’hésitez pas à nous contacter ; nous vous proposerons la meilleure solution adaptée à vos besoins.